Testing Is Key to Turning an Innovative Idea into a Successful Commercial Medical Device
Are you performing these 4 tests during medical device development?
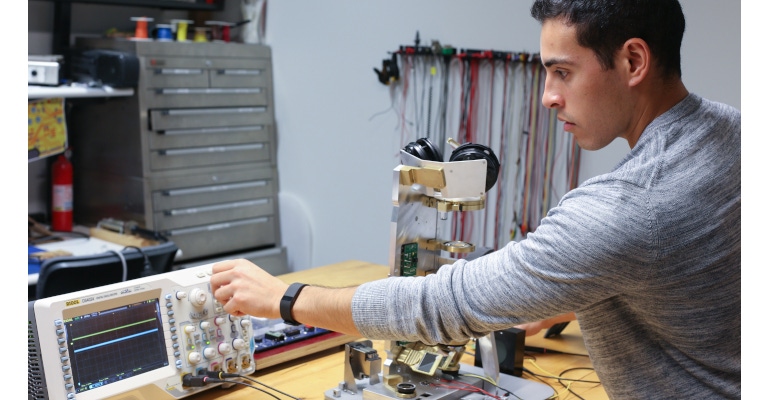
Formulating an innovative idea is only the first step in creating a successful commercial product. Design and engineering teams make countless decisions as they bring the idea to life. Testing provides an objective way for these teams to assess progress and improve the design at each stage of development.
Creating a successful commercial product is a challenging endeavor. It requires marketing insight, design creativity, and technical expertise. Whether a team is developing a complex laboratory instrument, a novel medical device, or an innovative consumer product, the effort is a dynamic process that requires the team to make a thousand decisions (or more!) as they work to bring the product to market. How can a team ensure that all those decisions result in a product that will excite customers and create a profitable business? Purposeful testing at each stage of development is the key.
Different types of tests are needed at each stage of development. These tests serve as objective “gates” to the next development stage. It’s important to learn from each test and to resolve significant issues before moving on to the next stage. From early R&D work, to first functional prototypes, and then to initial manufacturing, here are four types of testing to help turn your innovative idea into a commercial success.
1. User Testing
Creating a compelling product requires a true understanding of user needs. Start by interviewing users to gain insight into unmet needs and priorities. Conduct early user tests with simple concept mock-ups to learn user preferences and perceptions. Test with more-refined mock-ups to assess product form, user interactions, and feature options. Conduct user tests with basic functional prototypes to confirm the product is easy to use and does its job well before moving forward with full product development. By improving the product design with the learnings from each test, you can be confident your product will delight customers.
2. Core Technology Testing
Innovative instruments, devices, and other products are often based on a novel core technology. Some combine existing technologies in a unique way, while others require invention of a new technology. Before committing to a specific core technology, it’s important to thoroughly test the technology to determine whether it’s as functional and effective as envisioned. Recommended tests typically include functional performance, reliability, and user tests. Commercial success often depends on the core technology. Identified issues should be addressed by the team to be confident the technology meets user needs and is ready for product development.
3. Engineering Testing
Equipment and device designs are often composed of dozens, even hundreds, of individual mechanical components. Printed circuit board assemblies may have a similar number of electronic components and copper traces. Software may contain thousands of lines of code. All those components, circuits, and lines of code must combine to form a cohesive system. Engineering testing of initial prototypes is used to ensure that the engineered product design is easy to assemble and functions as intended. Given the complexity of the work, it’s common to identify needed design modifications. Making those improvements before moving into production is essential to prevent costly redesign work and reduce time to market.
4. Verification Testing
Profits will suffer if a new product can’t be efficiently manufactured at scale. Efficient manufacturing requires a product that has been engineered for ease of manufacturing and assembly as well as capable manufacturer and suppliers. While product prototypes are typically hand built and can be reworked and adjusted to make them function correctly, production units are built in an automatic fashion. Verification testing is used to determine whether products built on the manufacturing line meet the expected cosmetic and functional product requirements. Identifying and resolving manufacturing issues before scaling to full production quantities prevents costly scrap or rework of production units, or worse, shipping defective products to customers.
Developing an innovative product is challenging. Conducting purposeful tests at each stage of development and addressing issues before moving to the next stage is the key to turning an innovative idea into a successful commercial product.
About the Author(s)
You May Also Like