More Composites for Cars?
November 16, 2010
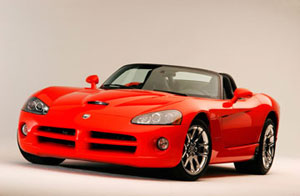
Theemergence of electric cars like the Chevy Volthikes the bar for materials requirements for automotive applications. Mostimportantly, cars must become much lighter to reduce power demand. A 10 percentreduction in vehicle weight permits about a 10 percent reduction in batterysize.
One of themost practical short-term solutions is increased use of glass-reinforcedcomposites, particularly for structural components such as underbodies now madeof steel. Longer term, the answer may be carbon-fiber-reinforced composites,such as those used in the Boeing Dreamliner787.
GM, Ford andChrysler have formed a research group called the USCAR Automotive CompositesConsortium (ACC) to develop automotive structural components.
"The goal ofthis is the development of composite automotive underbody that requiresstructural performance including crash loads with equivalent or superiorperformance to existing components and with reduced mass and acceptable cost,"says Libby Berger, staff researcher at the General Motors' Chemical Sciencesand Materials Lab, and co-chairman of the ACC Focal Project Four.
Systemrequirements for the materials under study include:
They must be manufacturable within a 150 sec cycle time. Two-shifts must be able to produce enough parts for 100,000 vehicles per year.
Methods for joining underbodies to the steel body-in-white (BIW) must be developed. BIW refers to a bare, welded body shell prior to painting.
Fabric reinforcements for sheet molding compound must be manufactured quickly.
More Composites for Cars? |
Two of thethree requirements refer to long-term concerns with composites: their abilityto be assembled and manufactured quickly. Steel parts can be stamped rapidly,but composites require assembling of the fabric structures that form the shapeof the part, and then the curing of the resin matrix system that impregnatesthe fabric.
Airbus andBoeing have both invested significant time in at least partially automatingmanufacturing systems for their carbon composite aircraft.
But automotiveproduction requirements, at least in terms of speed, are much more demanding thanare those for giant aircraft. Progress, however, is being made.
The ACCgroup has studied three types of composite materials: sheet molding compound(SMC) using vinyl ester as a matrix with glass fabric and chopped glassreinforcement, long-fiber thermoplastic, and urethane long-fiber injection.Carbon fiber is not being considered now because of its high cost. Existignresources are also strained by booming demand for the Dreamliner and the AirbusXWB, now in production.
"Based onthe ability of each to meet program requirements and a technical cost model,glass-fabric SMC with a low-density SMC core was selected as our material andprocess system," Berger says.
Today, SMCcomponent manufacturers use chopped fiberglass and resin to mold a variety ofparts such as wheel housing supports, instrument panels, and appearance-gradeparts, such as trunk lids and doors.
The SMC systemenvisioned in the ACC analysis, reinforced with ribs, replaces up to 17 steelstampings and reduces weight by 25 lb.
Adhesive Bonding
Acombination of spot welding and adhesive bonding is used to join the compositeunderbody to the steel body-in-white. Quasi-static and dynamic tests are beingperformed to determine key parameters to be modeled by finite element analysis.
The ACC groupand the University of Massachusetts Lowell are conducting research to see howfabric weaves and directions may allow fiberglass fabric to be used mostoptimally. Fiberglass fabric is the preferable reinforcing material overchopped fiberglass because it will allow a large panel to withstand structuraland potential crash forces during the life of the vehicle.
Onechallenge is understanding how fiberglass fabric will deform as it takes theshape of a part in the molding tool. While chopped fiberglass SMC flows easilywithin the heated tool, fiberglass fabric performs differently.
UMass Lowell Professors James Sherwood andJulie Chen are using computer simulations of the sheet molding compound tostudy the deformation of the glass reinforcement fabric, both without resin andas compounded, into fabric SMC.
"They foundthat the simulation of the complex fabric SMC deformation behavior
is possiblewith certain simplifying assumptions," says Berger. "We also performed experimentsto determine the shearing, tensile and frictional behavior
of the material, aswell as drapeability of multiple layers of the fabric SMC."
FEA Modeling
As a resultof the study, design engineers will be able to better predict how the forces ofmolding the component will affect the glass fabric SMC, thus understanding whatgeometries can be used to design a lighter weight structural underbody.
"Being ableto predict the behavior of the fabric SMC is extremely useful in developing theprocessing of the structural underbody," Berger says. "This technology willplay an important role going forward with the underbody project and in thefuture use of structural composites in crash-critical automotive components."
Bergerreviewed progress of the research at the SPE Automotive CompositesConference & Exhibition (ACCE). The goal of USCAR, founded in 1992, is to furtherstrengthen the technology base of the domestic auto industry throughcooperative research and development.
The ChevyVolt shown as a conceptcar in 2007 made significant use of lightweight materials, but most ofthose ideas were abandoned in favor of conventional materials to accelerate thelaunch of the vehicle, now scheduled for this month. If the Volt is acommercial success, it's expected to become a test bed for innovative materialstechnologies, such as increased use of composites.
About the Author(s)
You May Also Like