High-Tech Parts Planned for Joint Strike Fighter
February 22, 2011
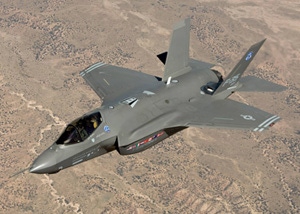
Additive manufacturing of plastic parts is expected to playa role in reducing costs of the F-35 LighteningII, also known as the Joint Strike Fighter Program.
"As many as 1,600 parts per plane have been identified thatcould be made from high-temperature laser sintered PEEK(polyetheretherketone)," says Scott Killian, a business development manager at Royal Engineered Composites of Minden,NE.
Possible applications include duct work and brackets thatattach sections. PEEK would replace aluminum.
High-Tech Parts Planned for Joint Strike Fighter_A |
Killian says that hundreds of the parts can be produced in asingle build with an EOS P800, which has a build envelope measuring 27.6 x 15.0x 21.7 inch (700 x 380 x 550 mm). High-temperature laser sintering (HTLS) is asystem in which parts are melted or sintered together from many thin layers ofpowdered material. It allows design complexities that are not possible withtraditional machining or injection molding processes.
Electro Optical Systems (EOS) of Munich Germany and Victrexof Lancashire, England announcedin late 2009 the development of PEEK as an HTLS material, partly because of itspotential for demanding aerospace applications.
PEEK has outstanding mechanical properties, good chemicalresistance and flame and temperature resistance.
Before PEEK was developed for HTLS systems, only standardnylons were available for engineering applications. Killian said that some ofthe JSF applications may be located near high-heat generating areas such as theengine or near the outside of the aircraft. Specifications require the capabilityto withstand temperatures ranging from -60 to 300F.
Some of the PEEK parts used in the JSF may be carbon-fiberreinforced.
Three companies now have the capability to provide high-performancepolymers for HTLS: Victrex, Arkema and Evonik. Emerging materials' capabilitiesfor the HTLS process were a hot topicat K2010 held late last year in Dusseldorf, Germany because of the tremendouspotential of the process. In a press conference, Jean-Pierre Marchand, directorof marketing and innovation for Rhodia's Engineering Plastics, announced thelaunch of polyamide (PA) powders for SLS.
The F-35 Lightning II is a family of fighters underdevelopment to perform ground attack, reconnaissance, and air defense missionswith stealth capability. Thirteen test models have been built to date.Large-scale production is still two to five years off.
The United States expects to buy a total of 2,443 aircraftfor an estimated $323 billion.
Cost estimates have risen sharply, prompting efforts to findnew technologies, such as HTLS, that can reduce costs.
Lockheed Martin Aeronautics is the prime contractor. NorthropGrumman provides center fuselage, weapons bay, and arrestor gear. Partners withRoyal Engineered Composites include Boeing and Northrop Grumman.
About the Author(s)
You May Also Like