Is DFMA the Way Forward for Reshoring Efforts?
August 21, 2015
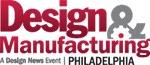
Just as there are varying opinions about the pace of reshoring of US manufacturing, there are different theories on how to create the efficiencies and economies without the industry to bring manufacturing back from overseas locations like China and Mexico. One expert believes the way forward for reshoring US manufacturing jobs lies in a combination of Total Cost of Ownership (TOC) and Design for Manufacture and Assembly (DFMA) analyses.
DFMA tools drive product simplification and early cost estimating to help determine and lower total cost of ownership (TCO). Pairing DFMA with TCO could help get US manufacturing back on track and jobs back on domestic soil, said John Gilligan, president of Boothroyd Dewhurst, the first company to commercialize software and methodology for DFMA.
“TCO and DFMA combined allow companies to measure corporate/product efficiency at each stage in the life of a product,” he told Design News. “Reshoring is based on the knowledge that total-cost-of-ownership analysis will reveal the hidden costs of foreign manufacture and pinpoint areas for domestic savings. Current research shows that efficient products manufactured in tight, cooperative, domestic supply chains are more profitable than exporting manufacturing.”
MORE FROM DESIGN NEWS: DFMA Takes a Back-to-Basics Product Simplification Strategy to Cut Costs
Moreover, the reason many companies offshored in the first place was low foreign labor rates and piece part costs — not the whole cost picture of delivered goods — which DFMA can provide, Gilligan said. “DFMA specifically helps manufacturers design out the labor in products based upon quantitative data of assembly operations and its minimum parts count criteria."
He said DFMA drives product simplification and early cost, guiding engineering teams to consolidate parts and assemblies into single, multi-functional designs and systems and then costing out those designs against competing materials and manufacturing processes.
“All this leads to highly efficient, quality products,” Gilligan said. “Because product simplification reduces the cost footprint of designs from CAD drawing archives, to inventory management, and on to manufacturing — including reduced service and warranty exposure — it is the ideal tactical approach for also achieving lower TCO.
Boothroyd Dewhurst recently held its international forum on DFMA in June. There, John Biagioni, president of Dynisco, a manufacturer of temperature and pressure sensors and instruments for plastic extrusion, led a presentation on the topic, unveiling an internal program for deciding where to manufacture globally and how to estimate and remove costs from product, corporate-wide organization, and supply chain.
MORE FROM DESIGN NEWS: Now Hear This: Wal-Mart Wants More US-Made Products
That program includes a methodology called “clean sheeting” or “should costing,” which breaks down the cost components of a product — including raw materials, transportation, direct labor, indirect labor, scrap, productivity-enhancing technologies, overhead, energy, regulations, and other relevant components. It then builds these components into a simple, quantitative model that companies can use to understand the magnitude of costs and how they can be reduced.
Dynisco has made the program available to manufacturers to help them in their reshoring assessments and build-where-you-sell strategies, Biagioni said.
That leads to the question of whether all of these efforts to reshore manufacturing are actually worth it -- whether it actually benefits companies to keep manufacturing facilities close to home. Gilligan said that research and experience shows that it does, from cost, quality, and innovation standpoints.
“Lack of collaboration, declining innovation, and disruption of supply chains is now a well-documented risk and familiar outcome of offshoring,” he said, adding that MIT and many of the large consulting firms have released studies to this effect.
Elizabeth Montalbano is a freelance writer who has written about technology and culture for more than 15 years. She has lived and worked as a professional journalist in Phoenix, San Francisco and New York City. In her free time she enjoys surfing, traveling, music, yoga and cooking. She currently resides in a village on the southwest coast of Portugal.
About the Author(s)
You May Also Like