Crash Project
August 21, 2000
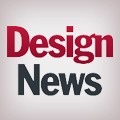
Facing a federal mandate that 40% of their average vehicle production meet new side-impact regulations starting September 1, auto-makers now have a new tool to help them test car interiors for compliance.
But at 7,000 lbs, it won't fit into the standard tool box.
Pacific Bearing's first drawing for the base unit. Via immediately accepted it. |
The nine-foot high by nine-foot wide, multi-axis Free Motion Head Form Impact System, from Brighton, MI-based Via Systems, uses bearings, hydraulics, pneumatics, and a host of other technologies to smack a 10-lb crash-dummy "head" into 16 different targets inside the car at 15 mph. The goal: to check if the design of the A and B pillars and other parts of the car's interior will soften the blow as required.
The Millbrook Proving Ground, an independent testing facility in Bedford, England, is the first to use the system. It's performing tests for a tier-one supplier to a major automaker. Tier-one suppliers are commissioning the bulk of the tests for complying with the federal regulations.
Design of the impactor system is a great case study in quick design response and coordination of outside resources.
"We need the system in 10 weeks," Millbrook engineers told Via.
"Right," said Via owners Dave and John Cheyne. When they regained their breath, they immediately launched a crash program of their own to design and build the system.
"We were used to eight-to-ten week turnaround on smaller projects, but not on anything this big," says Dave Cheyne. "It was a real test of engineering project management."
Pacific's final design of the base unit. |
The company relied on some 10 separate suppliers for everything from accelerometers to seals. But the most critical element of the system was the base unit and linear slide, supplied by Pacific Bearing (Rockford, IL). Via gave Pacific six weeks to complete its phase of the project, a short lead time even for a standard system of the size required.
But, as Pacific learned, a standard system wouldn't do the job. This project required a special linear-slide design.
Via wanted a system with a rotary beam attached to the Z axis of the base unit. The beam would have a hockey puck-shaped disc that would hold the "head," which itself would have eight degrees of freedom. The design called for a base unit that would position the impactor beam and head inside the car, be heavy enough to remain stable while the impactor flies around the inside of the car, and hold speed and accuracy at 1% repeatability, Millbrook's maximum requirement.
"I thought the schedule was crazy and impossible," says Dale Thorstens, chief engineer at Leidemaul, Ltd., the company that builds Pacific's slides. "Especially since we knew a standard product would not handle the load. We had to design a special." So he and the Pacific Bearing team honed in on a clear definition of just what the unit was supposed to do.
Leidemaul's design of the top section of the Z axis. The "head" attaches to the disc, itself attached to the master gear. |
The design called for a system that would develop 600 lbs of thrust at 3g in 50 milliseconds, 80 inches from the center line of the Z axis. Speed had to be 15 mph over 5.5 inches.
"The killer for us," says Thorstens, "was that when the Z axis was in the full down position, the impactor had to be 20 inches off the floor, or at the center line of the rotating plate. We had to build a carriage behind that with a length and width that would do the job."
Via wanted 52 inches of vertical stroke and five feet of horizontal stroke. Thorstens and his team started sketching solutions, taking care to use as many standard components as possible to save time.
"We knew we couldn't get enough bearings in there to do the job with two guide bar shafts," Thorstens says. So, they used four guide-bar shafts for the X axis, four for the Z axis, and 20 bearings per axis, which is two twin bearings plus a single bearing on each of eight shafts. Leidemaul used Pacific's Simplicity bearings. "They have good vibration- damping, shock-loading abilities, and high load-carrying capacities," says Thorstens, "and were the only bearings that would do the job."
The design team wanted to use a worm gear set to ensure the accuracy and repeatability Millbrook required, but knew they didn't have enough time to order the parts. Instead, they used a gear-and-rack system, which they could get faster. To strengthen the system, they added idler gears to double the amount of gear-tooth engagement. Engineers also added clamps to stabilize the rotating motion of the X axis.
Partners in design Accelerometers: Endevco |
How did they align the shafts? Leidemaul inspected and pre-qualified components to get matched sets, then aligned them with gage blocks and indicators.
"Pacific's design assistance and response was critical to this project," Via's Dave Cheyne says. "We communicated by phone, fax, and in person, but truthfully, once we agreed on the design there was little need for communication."
Acen Jordan, Via's founder, did the original design sketches for the base unit and propulsion system by hand. Dave Cheyne quickly put them into Pro/ENGINEER from PTC (Waltham, MA). "We depended heavily on Acen's experience, and Pro/E saved us on the machining end because it would tell us if things lined up," he says.
Leidemaul used Mechanical Desktop, a 3D solid modeling package from Autodesk (San Rafael, CA).
Millbrook is now conducting about 15 to 20 tests per day with the Via system vs six with its previous system, which Millbrook engineers had to basically tear down to reposition it for each test.
How the Free-Motion Head Form Impact System works Via Systems' Free Motion Head Form Impact System includes a pneumatic/hydraulic impactor that sends a head form into various parts of the interior of the car. Both the base unit and the "head" have eight degrees of freedom. |
About the Author(s)
You May Also Like