Linear motors propel geonomic "printer"
July 22, 2002
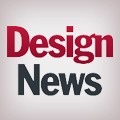
Imagine an office printer, with a print head that races across a page at speeds that are a blur to the human eye, placing characters within a millionth of a meter of their desired locations.
Improbable as it sounds, such a machine now exists. Admittedly, it's not an office printer. But the DotBot Microarray Printer, as it's known, combines the precision of a micro-surgical tool with speeds far faster than those of office printers. It can cross a four-by-four-foot work envelope in a quarter of a second, then can do a "move, stop, and drop" of its cargo in one-inch increments at a rate of 25 times per second. And, incredibly, the DotBot makes all of its high-speed deposits within a micron of their desired locations.
|
Engineers who helped developed the machine say that its "move, stop, and drop" actions are so fast, and so accurate, that they had to deliberately slow it down. "It was like a machine gun," says Mike Everman, president of Bell-Everman, Inc. (Goleta, CA), the company that integrated the power transmission and control elements into the machine. "We had to tone it down so that it didn't scare anyone."
Indeed, the likes of the DotBot have never been seen before, even in the high-tech world of genomics. Like a super-automated eye dropper, the DotBot lifts DNA-rich fluids from a trough, then delivers them in a flash of motion to 25 separate glass slides, all in under a second. Then it keeps doing that...second, after second, after second...until thousands or even tens of thousands of drops have been placed.
The technology enables genomics researchers, whose data requirements could choke a supercomputer, to collect far more information than they could ever gather by hand. As a result of such technology, they say they expect to advance their efforts from the study of a few genes a day to thousands per day.
Ultimately, the ability to quickly collect so much data could enable pharmaceutical companies and human genome researchers to come closer to mapping human genes and developing drugs to cure a host of deadly diseases, ranging from malaria to various cancers. And the key to that effort is the ability to extract mounds of raw data using extremely high-speed automated machinery, like the DotBot.
"To start, stop, and settle 25 times per second is awesome enough," says JoeBen Bevirt, president of a firm involved in the development of the DotBot. "But to do it within one micron is unheard of."
|
Engineers who helped develop the machine say that its ability to successfully combine high speed with high precision bodes well, not just for genomics, but for pick-and-place machinery, test devices, measurement systems, and assembly equipment.
"A lot of systems have employed one or two of this machine's technical features," says Curt Wilson, vice president of engineering for Delta Tau Data Systems, Inc. (Chatsworth, CA) "But up to now, no one has combined all the latest and greatest in the way this machine has."
Motion control showcase. Although the company that built the DotBot says it does not plan to pursue commercial development of the machine, engineers say the technology serves as a showcase for the capabilities of next-generation motion control and power transmission systems. The system, they say, integrates an array of state-of-the-art technologies, including linear motors, non-Cartesian actuators, fast DSP-based (digital signal processor) control, full digital control schemes, and very high-resolution feedback.
|
In essence, the DotBot consists of a four-by-four-foot work envelope with a linear motor-powered gantry robot spanning its X-axis. The gantry robot is built atop two linear motor stages, one at each end, which serve as the foundation for Y-axis motion. Traveling within SSR-Type linear motion caged ball bearings from THK America, Inc. (Schaumburg, Ill.), the gantry positions the machine's "print head," which drops the nano-liter samples of DNA material onto a table containing the glass slides. Analog encoders from Renishaw, Inc. (Hoffman Estates, IL) provide the system's position feedback.
"The object is for the machine to print a nano-liter drop onto a slide and then move an inch over to the next slide, and then to the next and the next," says Everman. "The hard part is to do it fast and accurately."
DotBot's linear motors, supplied by Trilogy Systems (Webster, TX.), are the enablers of its high-speed motion. Known as the LM310 Linear Motors, they offer peak force of about 40 pounds and use an "overlapping winding" configuration that is said to offer more power in a smaller package.
|
"Because of the overlapping windings, you get about 15% to 20% more copper turns in the flux space," notes Bruce Beakley, Trilogy Systems founder and developer of the patented overlapping concept. As a result of the overlapping concept, the linear motors are said to be about 20% more efficient that those of competitors, Beakley says. For system integrators, that translates to more force for 20% less power draw, or the same force in a smaller, lighter-weight package.
Engineers involved in the development of DotBot's motion control system said that the LM310's size advantages were the motivating factor in the decision to use it. "It gave us more torque per motor size," notes Scott DeLarvin, who served as an application engineer for Bell-Everman during the development of the DotBot. "And we wanted to strip out as much inertia as we could."
DSP-based control. Even with the system's low inertia linear motors, engineers say they couldn't have achieved the machine's extraordinary speeds without a, tight, highly-integrated, DSP-based control system.
The key to the system's control, engineers say, is its use of a UMAC Turbo controller from Delta Tau Data Systems. It employs an enhanced microprocessor CPU and an 80-MHz Motorola 56303 DSP, which is said to be inherently better-suited to serve the needs of machines like the DotBot than ordinary microcontrollers.
The reason they are said to be more suitable for such applications is that DSPs are optimized for fast and repeated mathematical calculations. The highly-pipelined math capabilities easily run repetitive algorithms designed to handle streams of data. Also, DSPs accomplish that without the need to employ costly state-of-the-art processors, and therefore can cut control costs by hundreds of dollars.
Most important, DSPs provide applications such as the DotBot with a level of servo feedback control that prevents the occurrence of natural instabilities, which can sometimes crop up at slower processing speeds. In particular, they allow a system to apply greater restoring force in response to position errors, without fear of a large overshoot.
"In general, the faster you can close the loop digitally, the higher your gains can be," says Wilson of Delta Tau. "And the higher your gains, the greater the stiffness of your overall system."
As a result of that stiffness, engineers say that they were able to employ the full speed of the Trilogy linear motors without fear of positioning problems. "If the processor is looking at the system 10 times every millisecond, then you can apply a higher restoring force because you can always catch the system before it overshoots," Wilson says.
Similarly, Wilson says, engineers reduced delays through the integration of fully digital control schemes and direct pulse width modulation. Unlike conventional control schemes, which typically pass data back and forth between the controller and the drive, Delta Tau's control system does all of its calculations in one central processor.
"By doing all the tasks in one processor, and by tying the output signals directly to the power transistors, we've minimized the delays," Wilson says.
What's more, engineers also reduced delays by doing as little analog-to-digital and digital-to-analog conversion as possible. Such conversions typically cause delays to build up, Wilson says, thus affecting control loop performance. "Delays like those are death in a servo loop," he says. "The longer the delay, the lower the system gain. And the lower the gain, the slower your reaction to positioning error."
Engineers say they also improved the system's resolution by employing Delta Tau's ACC-51 interpolator accessory card. The card, which accepts the sinusoidal input from the Renishaw encoders, essentially "chops up" the signal, creating 4,096 steps per sine wave cycle. As a result, the 20-micron sine waves coming out of the analog sensors are broken into 5 nm counts, which account for the system's unusually high resolution.
"There are very few controllers that were good enough to make a system like this work," says Beakley of Trilogy Systems. "They tried other commercial digital drives, but they flat out weren't good enough."
Precise servo control. Although the DotBot Microarray Printer isn't yet planned for commercial release, engineers who designed it say that it has provided a lesson in the development of fast, precise motion control systems. Some of the engineers who worked on the machine claim it could operate even faster than it does now, possibly in excess of 30 Hz or more. The intelligent use of linear motors, together with tight control and high servo stiffness have resulted in a machine that they believe is the fastest and most accurate in its field.
"When you push on this robot, it's like pushing on a piece of granite," says Everman of Bell-Everman, describing the system's servo stiffness.
Engineers say such qualities make DotBot's technologies applicable for a wide array of other automated machines that need high speed and precise servo control. Moreover, they say, the new technologies could serve in future gene sequencing applications, where high speed will always be crucial.
"The primary job of this machine was to move from slide to slide as quickly as possible," concludes DeLarvin. "And it's accomplished that; I can't imagine anything moving faster."
About the Author(s)
You May Also Like