Battery Chargers and Monitors Conserve Power
May 14, 2010
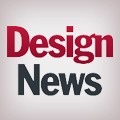
Proper attention to battery-management circuits in medicaldevices can extend battery life, reduce power loss and ensure devices use everybit of available energy. But to obtain these benefits, engineers must thinkabout battery management at the start of a product's design.
"Start with a plan that specifies thevoltage rails and currents the circuits will need, along with the availableinput power sources," says Trevor Barcelo, batÂtery-management product linemanager at Linear Technology. "If you need a 5-volt rail, one Lithium-ion celland a boost converter might work well. You also might consider two Lithium-ioncells that nominally produce 7.4-volts to replace the boost converter with amore common buck converter. However, if the system must be charged from a5-volt source, the stack of cells might create a challenge because you'll findfew, if any, boost chargers on the market. Those are the types of things youmust investigate."
Most engineers familiar with Lithium-ionbatteries know when they charge a 4.2V battery to 4.2V, they maximize itsshort-term capacity - the amount of energy a battery can deliver specÂified asamp hours, or Coulombs. "But after a year in storage, a Lithium-ion batterycharged to 4.2 volts will have less capacity than a battery charged to only 4.1volts," explains Barcelo. "At 4.1 volts a battery reaches between 80 and 85percent of maximum capacity, but it retains more of its capacity over time thana battery charged to 4.2 volts, so you can extend battery life and reduceoperating cost." Many charger ICs provide the option to charge Li-ion batteriesto 4.2 or 4.1V.
Engineers also can extend Li-ion batterylife by avoiding overcharging and high temperatures. To help engiÂneers avoidthese conditions, the Japan Electronics and Information Technology IndustriesAssn. (JEITA) and the Battery Assn. of Japan created guidelines and chargingprofiles for Li-ion batteries. High temperatures decrease battery life and cancause battery failure.
The LTC4099 from Linear Technology, forexample, has an over-temperature battery-conditioner option. "When the chargerdetects a temperature above 60C and a battery voltage close to 4.2 volts, itactively discharges the battery through an internal load that draws 180 mA,"says Barcelo. "When the battery voltage drops to 3.9 volts, or the thermistorreading drops below 58C, the IC turns off the internal load."
"Designers might not know a chargercircuit draws some bias current all the time," continues Barcelo. "If you usean energy-harvesting technique to charge a battery, say, with a piezo-electricgenerator, you want a charger that draws only a few microamps. Otherwise the‘free' harvested energy powers the charger and doesn't charge the battery."
Li-ion batteries aren't the sole choicefor engineers. Nickel-metal-hydride, or NiMH, batteries look attractive, too.
"Designers will choose NiMH because theylike the low cost," says Len Sherman, senior scientist at Maxim InteÂgratedProducts, a manufacturer of many lithium-battery and other types of charger ICs. "But then they realize it's moreexpenÂsive than expected to design a charger that detects a NiMH battery'snegative-delta-V or zero-delta-V termination point. As you charge a NiMHbattery, the voltage across it rises. But as it gets close to full, the cellvoltÂage falls slightly. So the charger must detect a 10- to 20-mV drop as itadds charge. A good ADC can measure that drop, but you won't get useful valuesif you charge at less than C/4 or even C/2." For a double-A 2900 milliamp-hourbattery, C/2 represents a charge current of 1.45A. The higher the chargecurrent, the greater the delta-V at the 100-percent-charged point.
"Engineers don't want tospend money on a high current adapter," says SherÂman. "Instead, they mightrely on a timer and run at a low charge current from a basic wall-plug adapter.But if someone unplugs it before the end of a cycle and plugs it in again, thetimer will reset and run for another full-charge cycle. The first generation ofNiMH batteries got a bad reputation, mainly because the chargers were so poor."
Also, standard NiMHbatteries self discharge to about 65 percent of capacity in a year, whereasSanyo's new Eneloop NiMH batteries, for example, retain about 85 percentcapacity over the same period. "Newer technologies in NiMH batteries offerlonger shelf life and can save energy by elimiÂnating charge cycles needed tomaintain battery capacity," explains Sherman. "The longer shelf life, however,comes at the expense of a bit less battery caÂpacity. Nonetheless, new types ofNiMH batteries might prove attractive in medical devices."
According to Rich DelÂRossi,product marketing manager for TI's battery-management solutions group, by usinga "fuel gauge," product designers can get the most energy out of a battery."When you monitor a battery's voltage, you see a fairly flat voltage for mostof the discharge and then the voltage drops to a point at which a medicaldevice can no longer operate. The discharge curve changes shape at differentdischarge rates and temperatures, so it's not someÂthing you can confidentlypredict."
"If a medical device hasdata in RAM, you will lose it if you suddenly remove power when the voltagedrops," continues DelRossi. "But a battery fuel gauge can tell the equipmentwhen the battery will reach that threshold voltage so the system knows when tocopy information and settings into Flash memory. Without a fuel gauge, theequipment would have to guess when to make that transfer. More complexequipment could use a fuel gauge to control power. In a handheld instrument,for example, it might dim an LCD or tell a processor to run slower to savepower."
Texas Instruments uses animpedÂance-track technique to account for the different discharge rates andbattery conditions. "We store a model of the open-circuit voltage of thebattery, from 100 to zero percent without a load across it," explains DelRossi."Then we store resistance as a function of delivered battery capacity. So forevery voltage value, we also have a resistance value. A fuel gauge such as thebq27541 for single-cell battery packs measures voltage and current, andcomputes the cell's resistance. We use that resistance throughout the entiredischarge cycle to derate the open-circuit curve into a curve that accuratelydescribes the actual battery conditions. The curve also accounts for resistancechanges at different temperatures."
"Then a host controllercan query registers to determine remaining capacity, time to empty, and othercharacteristics based on measured values," says DelÂRossi. "The controller thendetermines the time at which battery voltage can no longer power a device andthus, when to back up data and settings. Essentially, the fuel gauge acts likea Coulomb counter and it monitors electron flow to and from a battery."
About the Author(s)
You May Also Like