Stopping power
October 16, 2000
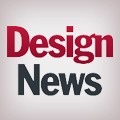
Mequon, WI-Give us a brake! That's exactly what Harley Davidson asked engineers at Hayes Brake to do. Only they wanted Hayes to develop a braking system that could be applied across all product lines-from the biggest bike to the smallest.
Hayes' solution was a compact, dual-opposed caliper brake system, robust enough for Harley's biggest bikes, and compact enough for its Sportster model. In fact, the brake is so streamlined that Hayes engineers were even able to adapt this concept for use on mountain bikes.
Meeting the requirements on the two ends of the spectrum posed a major challenge for Hayes. In particular, engineers puzzled over how to fit a brake caliper that could manage the kinetic energy of the biggest bike into the restrictive wheel package of Harley's compact Sportster bike. "The real crunch is in the horizontal spacing from the spoke profile to the inside of the disc, and the brake disc to where the brake mounts on the slider suspension, leaving us very little room to mount the back half of the brake caliper," says Phil Gould, vice president of engineering.
|
A typical solution would have been to use a floating mount caliper with no pistons on the inside. But this approach could result in increased drag, potential noise, and inferior response time and performance issues.
Thinking out of the box. Conventional wisdom in brake design calls for a single-diameter bore, which maximizes the piston's length-to-diameter ratio in order to prevent the piston from cocking in the bore of the caliper. "The problem results from the tapering of brake pads over time, causing the piston to work at an angle that can potentially cause it to bind," says Jim Buckley, president of research and development. Constrained by size, engineers had to do some thinking out of the box.
Ultimately, they came upon the idea of a ball joint piston. It has larger undercut diameters in both the front and rear ends of the bore, allowing the piston to cock without jamming. This feature enables the piston to cock or be misaligned up to 7 degrees , which can help minimize tapered pad wear and compensate for misalignment between the caliper, rotor, and suspension mount. The taper of the pad as it wears can cause the piston to cock on the internal flange at an angle less than the angle at which it would touch two sides of the bore. These undercut features thereby prevent the piston from contacting the bore and jamming in the cylinder.
|
The size constraint also impacted the design of the rotor. Typical rotors are either solid, one-piece designs, which are susceptible to warping, or expensive, two-piece designs consisting of a hub and a ring attached with pins. The two-piece design allows the outer ring, which is in contact with the friction pads, to naturally expand as it heats up without adding stress to the hub area.
Challenged to maintain cost targets without compromising styling appeal and performance, Hayes committed to making a one-piece design work. Engineers grappled with how to cope with the high temperatures (up to 1200F) that the surface of the rotor experiences. "Normally, we'd just make the rotor thicker, since the delta T is inversely proportional to the thickness, but again the small envelope we had to work within did not allow for that," says Gould.
Instead, engineers came up with an unusual geometry, which allows the rotor to expand radially without compromising braking integrity. As a traditional one-piece rotor attempts to expand from the thermal energies, it becomes susceptible to warping. The problem is that the outer rub area expands at a quicker rate than the hub or center area, resulting in thermal stress that can crack and warp the rotor.
A two-piece rotor gets around this problem by insulating the heat to the outer ring only. The ring is permitted to float on the pins, which enables it to expand and contract freely from the hub of the rotor. However, there is a cost and higher-weight penalty. Two separate rings and several mount pins can double the price of a typical rotor. Furthermore, minimizing the weight in the front end of a motorcycle improves handling. As a consequence, engineers typically try to minimize the amount of unsprung weight.
The key to success for Hayes' one-piece rotor is its non-symmetrical pattern. Its overlapping arms are designed to permit radial expansion up to nearly 0.080 inch in diameter. These arms act like a spring, allowing the rotor to expand and then contract to its original size without warping. By eliminating the possibility of warping the rotors, Hayes engineers were able to use a fixed mount caliper, which improves the brake's responsiveness and helps to eliminate both pad drag and noise.
In turn, the narrow spacing precluded the use of traditional brake pad materials. Engineers had to go with a thinner pad, which required development of a special, sintered copper material embedded with ceramic particles that provides sufficient pad longevity. The increased specific wear rate of the friction material enabled them to reduce pad thickness and usable volume.
From bikes to bicycles. With a small brake system in hand, it was only logical for Hayes to consider approaching the mountain bike market. Easier said than done.
In fact, previous attempts at adapting hydraulic disk brake technology to bicycles had fallen short. In cars and motorcycles, the brakes are always below the master cylinder-so gravity guarantees that any air in the system typically remains above the fluid in the master cylinder reservoir. Bike riders, on the other hand, routinely go through motions (crashing, storage, etc.) in which the brake calipers have the potential to be above the master cylinder, producing a situation that would trap air in the system.
As a result, design engineers were challenged to create a system that ensured the fluid does not backflow and introduce air into the line, creating compressibility in the system and compromising the brake's functionality. Simply sealing the system wasn't the solution, because any remaining air above the fluid could potentially be ingested. Further, the brake fluid, if heated during hard braking, still requires room to expand or contract without creating internal pressure that would move the pistons.
Features |
Mass of typical vehicle |
Full system mass |
Material of caliper |
Material of rotor |
Mass of rotor |
Material of |
Max deceleration |
Max system pressure |
Clamp force for |
Clamp force |
Torque requirements |
Cost |
While wrestling with the issue, one engineer was drawn to the concept of a baby bottle with a collapsible liner. "He realized that if we were to take a membrane like that and surround the master cylinder, it could expand or contract like a balloon as needed, yet function as a closed system," says Gould. The patented bleedable fluid reservoir also allows the brake caliper piston to self-adjust for pad wear without the potential of air ingestion. This is accomplished by evacuating all the air. The system is then back-filled with brake fluid and sealed with a strategically placed bleeder cap in the reservoir of the handle bar's master cylinder.
The other major modification involved figuring out how to eliminate the small amount of brake drag inherent in most cantilever and free-floating rotor systems. A little bit of drag is not as significant for a motorcycle, because of the amount of power and noise it generates. Mountain bikes, on the other hand, can't tolerate any, so engineers devised a way to retain and retract the pads through a special post-and-piston assembly.
The pad retention system is created by coupling the friction pad to the piston with a wire-formed spring that secures the pad to a post projecting from the piston. This ensures that the disk-to-friction material clearance is maximized and eliminates any brake drag through instant retraction of both piston and pads simultaneously. It also avoids any rattling noise by holding the friction pad tightly to the piston face, and it prevents the pads from falling out while transporting the bicycle with the wheel (and therefore the brake disk) out of the front fork.
With the exception of having two pistons instead of four, the mountain bike caliper is essentially the same as the motorcycle brake-only more compact and lighter in weight (0.251 lb versus 4.2 lbs.) And the mountain bike brake has been equally successful in its target marketplace. "Go to a typical race, and you'll see 90% of the downhill racers running our brand," says Gould.
Not often has a new product with so much stopping power had so much going for it.
Underlying engineering concepts: brake rotor design When designing the rotor for a brake system, engineers worry about the amount of heat generated during a quick stop. Excessive heat can potentially warp the rotor, causing free-running drag, loss of the brake itself through face and fluid compression, as well as compromising the effectiveness of future braking and brake life. Though many variables govern overall brake design, the basic equation brake engineers use to calculate the Delta T generated is: |
About the Author(s)
You May Also Like