Technology rides the French rails
July 24, 1995
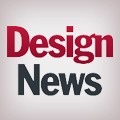
Take a trip on Amtrak, if you can find a train going your way after all of the proposed federal budget cuts. More than likely, here's what you will experience. Late arrivals. Infrequent schedules. Aging coach cars that are uncomfortable and somewhat unsanitary. Less than courteous service. And, for the most part, stations that are dank, dirty, and provide only a minimum of security for their customers. Chances are that, with some exceptions, you won't find conditions much different on the local transit scene either.
In contrast, ride on a French rail system--urban, suburban, inter-urban, or cross country--and you are in for a treat. The trains are modern, clean, and on time. Stations, old and new, are well maintained, wonderfully designed, and easily accessible. Train and station attendants are delightfully uniformed, courteous--and most speak English. Security is tight, but unobtrusive. Platforms are well illuminated, while closed-circuit TV and two-way communications keep a watchful eye and ear on passengers and traffic problems.
Changeable message signs direct you to your track, tell you where the next train is coming from and where it is going, or if any delays are expected. Automatic ticket dispensers spit out ducats in seconds and let you enter and exit trains just as speedily.
This reporter experienced the French touch first-hand. At the invitation of the French Technology Office, a small group of journalists from the U.S. and Canada toured several French systems to observe what makes them tick. It proved to be an eye-opening week.
High-speed comfort. No review of French transport systems would be complete without first taking a quick look at France's "Train a Grande Vitese" (TGV) high-speed rail system, already in service for more than a decade. From our vantagepoint in the cab of the engine, we watched the French countryside wisk by at speeds of up to 290 kph (180 mph) on the mostly automated trip from Paris to Lille, where the last ten miles or so were spent coasting to a just-opened, ultra-modern TGV station.
The trip back, this time in the comfort of a well-appointed coach, was effortless, smooth, and very quiet. In fact, if you didn't look out the window, you hardly got the sensation you were moving.
However, it's the technology behind the TGV system that makes it run so smoothly--the ability to bridge gaps in a high-speed rail network, for instance. The electric-powered trains operate at 360 km/hr (186 mph) on the 25-kV, 50-Hz ac of the French National Railway's (SNCF) newer lines, at 200 km/hr (124 mph) on refitted lines, then continue on over conventional track. This enables the system to retain time gains won on the high-speed rails.
Moreover, the system continues to improve. GEC Alsthom has signed an agreement for the research and development of a "New Generation" TGV. Among the project's objectives: reduced infrastructure costs, lighter cars, an improved driving and maintenance assistance network, more dynamic control of pressure waves in tunnels, and a four-current operation. Targeted for a 350-km/hr (217 mph) speed, these trains should start service in 1998.
However, it's at the local level that France has given its citizens the ability to create exceptional networks of mass transit. A brief look at two such systems visited by this reporter typifies how this came about, as well as how various technology approaches help make this possible.
The first system took birth only a short distance from the TGV station in Lille about ten years ago. Initially designed as a single line between a new town and the center of Lille, the automatic, driverless Vehicule Automatique Leer, or VAL for short, has evolved into a high-performance, fixed-guideway transit network.
The system incorporates technical solutions designed to meet new standards of passenger safety and quality of service, while minimizing capital expenditures and long-term operating costs. Helping make this happen: complete system automation, rubber-tired vehicles, changeable message signs, closed-circuit TV surveillance, and automated ticketing.
The initial 13-km (8.08-mile) line, opened in May 1983, gradually became the main artery in the regional capital's transport network. This was followed by a second 12-km (7.46-mile) line in April 1989. In this short period of time, some trains have traveled nearly one million kilometers (620,000 miles). More than 450 million passengers have been served.
The high frequency of trains allowed by the fully automatic control helped reduce the size of the rolling stock. Two cars with a total length of 26m (85.30 ft) and a width of 2.06m (6.76 ft) operating every minute can comfortably move up to 10,000 passengers per hour in each direction. Reduction in the rolling stock size also lowered capital expenditures 15 to 20% compared to a standard-rail system.
Service to the max. Quality of service encompasses several criteria, but the principal ones in Lille include: waiting time, travel time, comfort, and safety. Automatic control certainly addressed the quality of service. Waiting times can be adapted at a moment's notice by remote control at the central control room. This makes possible short waiting times, even on busy holidays.
From the central, computer-operated control center, train commands issue forth that not only regulate the train operations, but monitor the service for any possible conflicts or to permit schedule changes by center operators. The center also monitors CCTV and communications links among the stations and maintenance facilities, and keeps changeable message signs current. Only in the case of extreme emergencies does human intervention enter the picture, and such instances have been few and far between, relating mainly to security problems, rather than actual train operations.
Automation also enables the trains to stop within 15 cm (5.91 inch) of their station position. This, in turn, enabled the stations to be fitted with doors at the edge of the platforms. This door system ensures a very high level of passenger safety--passengers can't fall onto the line. In addition, it reduced the platform-width requirements, again reducing capital costs at stations.
The system also offers another comfort factor--the trains run on rubber tires. Not only does this result in a smoother ride, but it significantly reduces the noise level. On sections of the line that run above ground, the noise generated by VAL trains is lower than the ambient noise, with no noticeable system vibrations. Moreover, the rubber tires allow acceleration and braking rates of 1.35 m/s2 (4.43 ft/s2), permitting the system to maintain a scheduled speed of 35 km/h (21.75 mph), including stops. System operators say the rubber-tired vehicles not only outperform their steel-wheeled counterparts, but they also require less maintenance.
The VAL vehicles, produced by Matra Transport, Paris, consist mainly of aluminum alloy to keep weight to a minimum. Equipped with simple axles, they have an empty weight of no more than 31 metric tons, or 624 kg per square meter of floor space. That compares with 865 kg for a conventional modern urban rail car.
A two-car train set measures 26m (85.30 ft). It can hold 154 seated passengers and as many as 208 during rush hours. Frequency of service helps deter crime in stations. Close to 400 CCTV cameras assure rapid response to any threatening passenger situation.
In the ten-plus years of VAL, public transit ridership has more than doubled. But perhaps of more importance, especially to U.S. transit observers, the system has made an operating profit since 1989.
Riding in Rouen. Rouen, a city of about 400,000 inhabitants located 120 km (74.56 miles) to the northwest of Paris, has grown up on both banks of the Seine. Tourists probably remember it best as the place where Joan of Arc was burned at the stake. However, it was the city's light-rail transportation system that left a lasting impression with this reporter.
In 1988, the Syndicat Intercommunal a Vocation Multiple (SIVOM), the area's transport organizing authority that covers 33 municipalities, decided to create two dedicated public transport routes as the first phase of a skeleton network serving the area's most densely populated residential and business districts. The system voted most likely to get the job done: the tram, or light-rail, vehicle. SIVOM entrusted the four-year, 2.6 billion franc ($517 million U.S.) project and 30-year operating license to a concessionaire company. Operation began in December 1994.
The 11.2-km (6.96-mile) network includes 23 stations, five of them located underground. The first phase consists of two branch lines on the south bank of the Seine that meet over a common section that crosses an existing road bridge. Part of this line on the north bank includes a 1.8-km (1.12-mile) tunnel that runs under the "hypercentre."
The above-ground infrastructure embraces platforms separated from vehicular traffic. Lush, green grass covers some of the railbed areas. All of the stations can accommodate double trains. A 4.4-km (2.73-mile) extension to the network is scheduled to come online at the end of 1997.
Train-set technology. A key feature of the rolling stock, made by GEC Alsthom, encompasses a low floor accessed through the car's central section. This makes it possible for passengers or those in wheelchairs to simply walk or roll directly from the platform onto the cars.
The 20 Rouen trains are virtually identical to those operating in Grenoble, France, which this reporter also had a chance to inspect. The Grenoble cars made such an impact with the transit community that they have become synonymous with the city.
A train set consists of two articulated cars mounted on two motor bogies, plus a low intercommunication floor on a central carrying bogie. The cars run over normal-gauge track, can operate with total reversibility, and require no compressed air. Adding an integral coupling enables the formation of automatic multiple units.
Two self-ventilated traction motors supplied by two thyristor current choppers provide the electric transmission. Microprogrammed processing of the traction/braking setting optimizes adhesion.
The long, low floor in the central part of the body measures 17.85m (58.56 ft). A three-step stairway leads to the raised platform at each end that accommodates the two motor bogies. Research into the intercommunicating low central floor led to the design of the independent-wheeled, extra-low central bogie. It incorporates elbowed axles that enable movement between the articulated vehicles.
All bogies have resilient wheels and two suspension stages. Elastomer and rubber pads help cut down on noise. The monomotor-type motor bogie design places the motors longitudinally and suspended in the center of the frame. Cardan shafts and two-stage reduction gearboxes transmit the power.
The cars are equipped with two 275-kW engines that provide acceleration rates of 0.92 m/s[super{2}] (3.02 ft/s2). Regenerative electric and dynamic braking, coupled to electrohydraulic discs, bring the trains to smooth, effortless stops. Magnetic pads add to the efficiency of the system in the case of emergency stops. An anti-slide microprogrammed device that's electronically controlled helps ensure the comfort and security of passengers when the cars are in the braking mode.
Living up to its name. The network's logo, "Metrobus," recalls the key concept behind the project--cohesion and complementary service between two transportation modes, the metro (rail system) and the bus. The bus network has been totally restructured around the two metro lines to serve as a feeder system.
Electronic displays mounted inside both trains and buses provide up-to-the- minute routing information. Video information points at metro stations and principal bus interchange stations also help facilitate the combined use of the two transportation modes.
All below-ground metro stations have lifts accessible to the physically handicapped. Platform edges, luminous studs opposite each door, bright destination signs, and voice announcements ensure that people with visual, auditory, or motor handicaps can make good use of the system.
Riding on the system convinced this reporter that the Rouen region made the right decision. In fact, Metrobus has become so popular that other area residents will have a chance to find out just how convenient the system is when a 4.4-km (2.73-mile), eight-station extension to the network opens late in 1997.
The week-long French trip left this reporter with this impression. Yesterday's solutions cannot be extended indefinitely or they inevitably reach a point beyond which efficiency is lost. The end result is likely to be just the opposite of what is required.
Urban areas in France have addressed this problem up-front and found a practical solution through modern, convenient, attractive transportation systems. The U.S. could learn a lot from the French transportation revolution.
An OSCAR for automated bus fueling
Urban public transportation systems with large bus fleets might take a tip from OSCAR when it comes to efficient fueling. The automated fuel-server robot, developed by Robosoft S.A., Neuilly-Plaisance, France, operates at a bus maintenance facility in Toulouse, France. Now, freed from refueling chores, drivers can use the time for checking tires, lights, turn signals, levels of engine oil, brake and transmission fluids, and help account for fares collected.
Key to OSCAR's operation is a robotic and sensing device that finds the fuel-tank filler caps, unscrews them, then replaces the caps once the fueling is finished. Data acquisition, such as the vehicle ID, date, and location of the tank filler, remains totally automatic, thanks to an electronic onboard label system. The robot requires no specific programming: The only data needed are coordinates of the fuel cap and bus identification, recorded into the tag when installing the system pad. OSCAR also can accept manual data from the driver, including badge number and odometer readings.
OSCAR's technology makes possible similar adaptations for everything from ambulances, postal vehicles, and railroad locomotives to police, taxi, and automotive fleets. The system costs about $70,000, plus $550 for vehicle components.
Transporting people to new heights
Avid skiers around the world no doubt can tell you who Poma is. Many have made good use of cable systems designed by the Grenoble, France, company that have lifted them to their favorite ski slope. But how many people know that Poma is also a major player in the transit world?
The fact is that Poma offers a total of three transit technology systems:
The People Mover for shuttle operations.
Poma 2000 for network applications.
Trasse for transit corridors.
The People Mover is a fully automated, cable-propelled system with rubber tires or resilient steel wheels controlled by a central computer. The system uses a patented fixed-grip technology to provide a permanent attachment between the passenger vehicle and the rope that horizontally propels and guides the vehicle. The design principle resembles vertical elevators. The fixed-grip arrangement makes the system ideal for shuttle operations between various activity centers. The major equipment elements of the system include: guideway, propulsion system, vehicles, and automated control and communication systems.
The Poma 2000 Automated Guideway Transit, also a fully automated, cable-propelled system, is designed for transit network applications that encompass several intermediate stops in a variety of alignment configurations, including loops. Unlike the People Mover, the Poma 2000 employs a patented detachable cable grip technology that provides a controlled, removable attachment between the passenger vehicle and the cable that propels and guides the vehicles. In operation, the system resembles cable-propelled gondola systems currently operating throughout the world, such as in mountain environments with extreme weather conditions. However, contrary to the "gondola principle," the Poma 2000 is bottom-supported and runs on a separate "active track" guideway.
Like its two counterparts, the Poma Trasse system is fully automated and cable propelled. Its design, however, lends itself to more demanding transit corridor applications, especially where availability of the right-of-way for more conventional systems is limited or too costly. This aerial passenger system uses a very light cable guideway with long spans. It can be installed in densely populated urban areas with no need to displace existing structures and traffic arteries.
GEC Alsthom-built train sets for the Rouen system feature a low floor accessed through the car's central section, making it easy for passengers or those in wheelchairs to walk or roll directly on and off the cars. Elbowed axles enable movement between the articulated vehicles.
Matra-built VAL cars for Lille include computer-operated controls and rubber tires that quiet the ride.
About the Author(s)
You May Also Like