Synchronous Belt Drive System
January 5, 2011
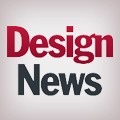
Baldor Electric Company's synchronous belt drive system have Dodge HTRand HTRC Tracker belts. The belts have aReinforced Parabolic Profile (RPP) tooth design allowing the belt teeth to sitdeeper in the sprocket compared to standard belts.
The angle ofthe RPP Tracker belts allows synchronous transmission of power to eliminateslippage and speed variation on high torque applications. TapeLock sprockets are machined to match thesprocket and belt and the new synchronous drive system delivers 5 percent moreenergy efficiency over properly maintained V-belt systems.
The neoprenerubber belts are manufactured with a fiberglass cord for tension stability andprevents moisture from being absorbed. With no belt shrinkage or stretch, Baldor says this belt will not haveto be re-tensioned making it virtually maintenance free and the beltconstruction also helps reduce the belt installation tension, increasing thelife of the other mechanical components.
Baldor says when compared with a QD style product, the Dodge Taper-Locksprocket design requires less shaft length, offers more bore sizes per bushingsize and delivers more torque. The Dodgesprocket system also minimizes overhung load by positioning the belt's centerline closer to the motor, reducer and bearings. An anti-corrosion coatingprovides rust prevention and can achieve power ratings up to 1,200 hp.
Synchronous Belt Drive System
About the Author(s)
You May Also Like