May 20, 1996
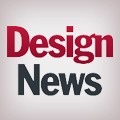
Indy Car racing is a game of inches and thousandths of seconds. Scott Pruett and Patrick Racing know. Last year, Pruett edged Al Unser Jr. in a photo-finish to win the high-speed Michigan 500.
The victory was due to more than Pruett's obvious driving skills. Engineering support before and during the race propelled him into the winner's circle.
This year, once again, the Patrick Racing team is banking on technology. Leading the list of high-tech tools is Unigraphics CAD software from EDS Unigraphics, ADAMS kinematics analysis from Mechanical Dynamics, and the Pi data-acquisition system from Pi Research, Ltd.
Focus on speed. "We're a small team (19-20 people), we only run one car," says Chassis Engineer Roy McCauley, one of Patrick Racing's three engineers. "We try and focus on making the car go faster and not get sidetracked on projects that we aren't likely to see quick returns on. We focus on achieving the end result: (lowering) lap time."
The competitive pressures of racing drive product design cycle times down to days and sometimes hours. States McCauley, "On a micro scale, this is what happens every day in industry. Our time constraints are, as one machine shop told me, ridiculous!" Over a season, the iterative racecar engineering process will involve the gathering and analysis of hundreds of megabytes of on-car data and then the adjustment or modeling, redesign, and manufacturing of new components.
For example, "out of the box," a Lola chassis only approaches 85% of its capability, estimates McCauley. Deriving the next 15% on road courses, ovals, and superspeedways keeps him and the other engineers busy all season. They start by tearing the chassis apart and measuring every component. Then, they "massage" every component to their specs.
They add more heat shields to protect the carbon fiber from melting. They may optimize the header layout and attachments, change the suspension pushrod design and instrumentation, or add or remove bearings.
Why is this necessary? "Lola has good data, but they don't have our data," says McCauley. "We have more access to data that describes the operating conditions of the car," adds Vehicle Dynamics Engineer Tom German. "Typically, we are the ones providing them with the information on what loadings the car actually sees."
Occasionally, they discover minor design flaws or oversights that might cost a race. These they fix and keep secret for a competitive advantage. If a flaw were ever found that might make the cars unsafe, they would inform the appropriate manufacturer immediately.
Tools of the trade. McCauley is an expert at designing stiff, light parts. His designs are often based on the chassis analysis German does. Their work is symbiotic and sophisticated. Both use Unigraphics (UG) V.10 CAD/CAM software and Pi Research data-acquisition hardware and software.
When McCauley modifies or redesigns and optimizes components, the full benefits of Unigraphics kick in. "UG is a fourth engineer to us. It's something I can control, and it helps me do my job faster," McCauley says. He doesn't like programming and learned to use three modules of UG in just four and a half days of training. He runs the software on a Sun Sparc20. Along with Firestone and EDS, Sun is also a team sponsor.
By pointing and clicking his mouse and using menus, McCauley uses UG to create and analyze 3-D, solid models. He redesigned a complex rear-wing mounting plate with many pockets in just three and a half hours. Three years earlier, he'd have built and tested many different parts, a process that could have taken an entire week.
With geometry in place, UG instantly calculates the new mounting plate's weight, moments of inertia, centroids, and moduli of elasticity. After a few easy manual iterations of pocket shapes, patterns, wall thicknesses, and taper, he has designed a part with a much better stiffness-to-weight ratio. He can rotate and view the solid model from any angle.
To test its integrity, he uses a spreadsheet model to stress the lighter part against actual loading conditions gathered through data acquisition. A passing buckling test means the part can be built. With some labeling and a few more mouse clicks, McCauley quickly and automatically generates NC code and a drafting model that a machine shop can work from. Sometimes, he sends a floppy disk to an outside machine shop. In the future, engineers will use the NC code to program an automated machining center in Patrick's own shop, saving still more time.
Over the next year, McCauley says, he will use UG to build a model with 2,000 or more components and associated subassemblies that will describe the entire car. Such a "master model" will make UG the central repository of component geometry, materials, and assembly--in effect, a product data management (PDM) system. While Patrick will likely adopt PDM methods in the future, UG's ability to check part clearances and port part information into kinematics, stress, and other engineering analysis modules or software packages is a key benefit today, states McCauley.
McCauley also extensively uses ADAMS kinematics analysis software. UG automatically generates ADAMS-compatible models.
McCauley took a damper design and converted it into an ADAMS model. The geometric model reappeared in two dimensions with mechanical symbols for springs and damping parts. First, he defined the links between each part that makes up the damper assembly and then he constrained each moving joint's freedoms of motion to one. Next, he set up a forcing function based on true track-loading data and drove the model damper through a simulation. A plot of force versus displacement appeared on the screen almost instantly.
Then McCauley iterated and simulated the damper design by varying orifice, piston, and outer-diameter sizes until he was happy with the results. He says this process eliminated much rig testing, and he estimates automation saved him three days (~30%), assuming that the project would normally occur over a 7-10 day period.
Before this season's first race, McCauley analyzed numerous damper shim-stack/valving combinations to provide a set of "best-bet" suspension tuning options. He rig-tested the most likely pairs on a shock dynamometer to verify his analysis. One combination reduced bumpiness through certain turns in the course, while another produced better handling over smooth sections of the track.
Data doctors. Engineers wire the cars much as doctors wire patients in a critical-care unit. Tom German gathers the hard facts that become the inputs that inform design work on suspension components and set-up at the race track.
He uses the data acquisition and analysis system from U.K.-based Pi Research, Ltd. Pi provides most of the analog and digital sensors, while German buys simple thermocouples from Aeromega and strain gauges locally. He says Pi modifies some of the sensors it purchases and resells to withstand the harsh racing environment.
What does he measure? About 45 engine and chassis parameters are stored in 4 Mbytes of on-board memory, including: ride heights (pitch and roll), wheel speeds and loads, suspension positions and loads, engine plenum pressures, engine throttle and butterfly-valve positions, exhaust backpressure, engine oil and coolant temperatures and pressures, transmission temperature and pressure, rpm, fuel consumption, and accelerations. Engineers mechanically damp the three-axis, yaw-rate accelerometer to filter out vibrations that would mask the signal sought.
While the car is on the track, the Pi Research system continuously downloads data via microwave telemetry at about 50,000 baud to a trackside portable PC. Once a lap, a light-sensitive beacon triggers special downloads when the car passes, providing German with data on max/min and average lap data on engine rpms, fuel use, and other parameters.. Simultaneously, the system logs channel data at a higher frequency to the on-board memory. When the car pits, engineers download this data through a cable hook-up to the PC.
During track testing, qualifying, and racing, German uses data from the Pi system to monitor how the car is performing. Pi's V6 Pro Windows-based analysis software can automatically update and display graphs, histograms, or X-Y plots after the car completes each lap. This enables him to compare the car's performance from lap to lap and spot problems. It also allows him to track down problems that Pruett relays over the radio. Hopefully, he and his colleagues can have a solution waiting when Pruett makes his next pit stop. Often, these "real-time" engineering chassis tweaks involve nothing more than a slight wing or damper adjustment.
Of all the race data collected, German says ride heights and wheel loads are the most critical parameters because they indicate how well the critical aerodynamics are working. The aerodynamic efficiency of the front wing and underbody venturi are highly sensitive to changes in ride height, so engineers monitor them closely. Since tire grip increases with loading, the front and rear downforces determine cornering speeds and any understeer or oversteer handling bias. Their proper control are therefore crucial to racing success.
"The software and hardware is in general off-the-shelf stuff," German says. "The advantage comes from understanding what you're measuring, knowing what to measure and look at, and really applying it. We've designed some stuff that's better and provides us with a competitive advantage from the standpoint that we have more understanding and can control more aspects of the car than we have before."
German, McCauley, team Patrick, and Pruett must do it all well. Firestone is the team's main sponsor and chose them to test its prototypes before its return to Indy Car racing last year. After this season's first two races, Pruett and team Patrick have a fourth and a third to their credit, and lead in the points standings. Firestone tires have been on both races' winning cars, as have the Honda engines Design News covered in last year's Indy Car article (See Design News, May 22, 1995, p. 58).
Safety the driver in Formula 1
FORMULA 1 ENGINEERS have had to cope with several new rules changes this year that reflect the safety concerns of the sport's governing body. Those changes include higher and stronger cockpit sides, foam padding at key points to lessen impact injuries, a larger opening for easier emergency exit, a ban on small wing sections fitted at the rear, and aircraft-type "black boxes" on all cars.
"Probably the most visible change is the nose," says Gary Anderson, technical director of Jordan Grand Prix. Their model 196 is the car that will carry the Jordan Peugeot name in this year's challenge.
Changes in nose design, claims Anderson, result from modifications to the regulations that determine the front of the chassis. "The '96 regs," he says, "dictated a larger cross-sectional area for safety reasons. One of the simplest ways of accomplishing that is by raising the nose." The latest Benetton, McLaren, and Williams cars also exhibit raised-nose sections.
Underbody alterations. Raising the nose allows a better flow of air under the car. Since FIA placed very strict limits on the dimensions of front and rear spoilers a few years ago, attention has switched to underfloor design for aerodynamic gain.
Even more effort has gone into underfloor design with the outlawing of winglets in 1995. Tailoring the gap between the stepped curve of the floor and the road surface creates a venturi effect for better road holding. Engineers calculate the gap for speed on straight, flat track, but they make tradeoffs with the suspension when considering corners and bumps.
The new rules on driver protection, requiring higher cockpit sides and a larger entrance, have also affected aerodynamics. The basic design requirement is a 220-mm (9 inch) offset from the diagonal between the roll hoops. This generally means raising the rear edge of the cockpit. The rule makes backward vision worse.
Gearbox changes. Gearboxes are a constant source of problems, leading to several changes this year. Tyrrell, for example, swapped to a new six-speed, longitudinal design for a better underfloor profile. Benetton has also switched to a longitudinal gearbox. It is a seven-speed design.
Over at McLaren it was a similar story. Their new gearbox design is also a longitudinal, six-speed unit. This will be fitted to an entirely new engine from Mercedes, the V10. As an indication of the pace of development work in the Formula 1 environment, design of this engine did not start until October 1995.
"Our people did a very good job, working day and night," announced Norbert Haug, head of Mercedes-Benz Motorsport. With Germanic precision, he stated that the new engine "ran for the first time on 3rd February 1996 at 7:36 pm." This same engine achieved fifth place at Melbourne.
--Norman Bartlett, European Editor, UK
About the Author(s)
You May Also Like