Rebirth of lean-burn technology
November 3, 1997
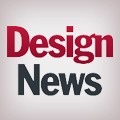
Without cupping your hands around it, a match in a hurricane quickly blows out. Today's ignition systems present engineers with a similar challenge. Piston motion, even at moderate engine speeds, induces flow velocities that easily quench the spark before the fuel mixture ignites. That's why engine designers typically locate spark-plug electrodes in a crevice protected from the combustion chamber's flow field.
Michael Ward, president of Arlington, MA-based Combustion Electromagnetics Inc. (CEI), has a different take on things. He says flow should actually be an asset when lighting the lean-fuel mixtures that provide the engine efficiencies and low NOx emissions that automotive engineers desire.
Now, Ward has a patent for flow-coupled spark discharge which one Chrysler engineer says could be the enabling technology for the next generation of lean-burn engines, once the Holy Grail for those seeking to improve fuel economy. Test results at GM, Mazda, Lucas Industries, and Chrysler highlight the advantages of Ward's high-energy, flow-resistant spark. With average U.S. fuel economy at its lowest level since 1985, according to The New York Times, and car companies entering the penalty phase for missing CAFE( Corporate Average Fuel Efficiency) requirements, lean burn and Ward's high-flow spark may offer a panacea.
Key to the patented technology: a low-cost ignition system that, he says, delivers three to five times more spark energy, higher ignition efficiency, more spark power, and greater flow resistance.
The spark actually thrives in the engine's flow field, Ward asserts. Components enabling the high-powered spark:
A power converter that steps up battery voltage to 42V from the standard 12V.
Higher switching currents from standard 600V IGBTs (insulated gate bipolar transistors).
A proprietary false-firing arrestor.
A low-loss snubber that reduces switching losses and sends coil leakage energy back to the battery.
Taken together, these components produce a spark with current in the range of 300 mA to 500 mA and with a triangular shape. Ward had discovered in several years of research into plasma physics that a spark with such characteristics was optimum.
New spark plug. Although the system operates with any existing engine, Ward has designed a new spark plug to maximize its benefits. Called the Halo Disc, it uses erosion-resistant tungsten-nickel-iron. A recessed insulator minimizes fouling of the insulator end, and a thin, suspended ground-ring electrode minimizes electrode obstruction and quenching. An inductor rather than a resistor suppresses electromagnetic interference.
CEI's coils use only half the standard coil windings to boost the rate of energy delivered to the fuel mixture by four to six times, while increasing spark energy three to five times. Ward uses 36 vs the standard 42 AWG wire in the coils to lower costs and ease handling. They are open E-core coils instead of the standard two-piece welded design with air gap.
Other elements of the coil design: no welding on one-piece laminations; easy assembly and access to electrical terminals; 20% less weight; 40% fewer primary wire turns; 50% fewer secondary wire turns.
The ignition coils have three times the energy density (mJ/g) of the best state-of-the-art ignition coils, and deliver 150 mJ compared to SI's 50 mJ, according to the recent tests at Chrysler.
HBI delivers a spark that actually thrives in the engine's flow field, enhancing ignition effectiveness to burn lean fuel mixtures, and impacting future coil, plug, and combustion chamber design. |
Ward's spark thrives in high flows and won't go out even at 10m/sec flow velocities through the spark gap, he says.
Test results. Early tests at G.M., Mazda Motors, and Lucas Industries revealed that Ward's system increases fuel economy up to 20%, and reduces NOx emissions by up to 90% over standard ignitions operating at stoicheometry.
The ignition reduces emissions by using high EGR or burning very lean fuel mixtures, as lean as 28:1 in the presence of high flow, says Ward. In tests on a Ford Escort engine, on a flow test rig at General Motors Corp., and on Mitsubishi Motor's vertical vortex engine, Ward's ignition system operated as lean as 8 air-fuel ratios (AFRs) above what standard ignitions can obtain.
Separate tests at Chrysler on the new spark plug showed that it improved fuel economy all by itself (5-7%). The latest tests of an early version of CEI's ignition took place in 1995 at Chrysler Corp. A prototype improved capacitive discharge ignition (ICDI) system on a 4-cylinder engine was operated under relatively cold conditions to simulate the early part of the car's drive cycle--when engine stability, emissions, and fuel economy are at their lowest. The test results showed best engine stability and a remarkable 3% to 20% improvement in fuel economy.
"After changing over the coils and controller on the test rig," recalls Chrysler's advanced product development supervisor Anson Lee, "I've never seen an ignition like this before." The CEI ignition showed significantly smoother engine operation, especially at cold idle as exhaust gas recirculation (EGR) was increased. "The engine equipped with a production ignition died, while Ward's system just kept running," he adds.
Lee notes that it's a very capable high-power, high-energy system, higher than anything on the market. "He's got something here that nobody else has, and maybe, after extensive testing, this will prove to be an enabling technology for the lean-burn engines of the future."
The concept of fuel-efficient, leaner, cleaner burning cars is nothing new. While most modern-passenger vehicles use three-way catalyst technology to reduce emissions, Ward and Lee both point out current catalyst limitations. Requiring relatively rich fuel mixtures to operate effectively, Ward says that "Catalytic converters make lean burn impossible, by design." The catalytic reaction demands stoicheometric-engine operation at AFR of 14.7, meaning the engine must burn a comparatively-rich mixture of 14.7 parts air to one part fuel.
While engine designers typically locate the spark-plug electrode in a crevice to protect it from the combustion chamber's flow field, high-energy flow (HEF) ignition is enhanced with extended-gap spark-plugs that position the spark directly in the flow region. |
For a car engine to be efficient and clean, under part load where almost all driving is done, the engine must burn as much of the fuel as fully as possible; burn it at as low a temperature as practicable; burn it as quickly as possible; and burn it with as much air dilution (or EGR) as possible.
A central problem with burning lean fuel mixtures, explains Ward, is controlling the speed at which the flame propagates through the fuel-air mixture in the cylinder. The leaner the mixture, the slower the flame moves from the electrodes, and the more susceptible it is to quenching. If the flame burns too slowly, the piston moves down before harnessing the combustion energy. And if the flame moves too quickly, it combusts before the mixture is properly compressed and does negative work on the piston. Either condition results in poor engine performance.
Ward's company, CEI, discovered that high spark energy, spark power in the range of 100 watts, and high flow resistance give the best lean-burn results. It was to meet these requirements and others that Ward upgraded both standard and racing-car ignition systems. His "HBI" system is the upgrade for the standard inductive system used in passenger cars. "ICDI" upgrades the capacitive discharge ignition used in racing and specialty applications.
The previously distinct systems are now similar in more ways than they differ under Ward's paradigm. The peak output voltage, current, spark shape, energy, circuit and spark discharge efficiency, and other parameters are similar. Only the coil designs differ. The reason: For HBI, coil primary inductance is the key parameter, and for ICDI the coil leakage inductance is key.
Engines need more squish. While both HBI and ICDI designs improve lean-burn capability in existing engines, burning even leaner fuel mixtures results from flow-enhanced ignition. "To stretch the spark kernel and improve lean-burn capability, combustion chambers need more flow and high turbulence, particularly squish," Ward says. Squish, he explains, is the squeezing of the air towards the center of the combustion chamber as the piston moves upward. By designing the ignition in conjunction with the combustion chamber, engineers could optimize engine efficiency.
Because flow-enhanced ignition changes the rules of combustion chamber design, Ward urges automakers on the verge of retooling for a new generation of high-tech, electronically controlled, over-head cam (OHC), multi-valve engines to reconsider. Ward notes that while OHC multi-valve engines may breathe easier, the domed shape at the top of the combustion chamber limits squish.
And just as most automakers are dismissing the two-valve pushrod engine as obsolete, Ward once again defies convention. He contends that just as the standard ignition system was never used to its full potential, neither has the two-valve pushrod engine been fully exploited. The pushrod engine has many advantages over more expensive OHC, multi-valve designs, he says: It's more compact, economical, weighs less, and has 1/3 fewer parts. But, Ward notes, even more importantly, its combustion-chamber geometry naturally creates the high squish flows and high turbulence that HBI's spark thrives in.
Ward proposes that automakers meet their short-term economy and efficiency goals with the two-valve, pushrod engine equipped with the enhanced ignition system. Low-cost modifications--such as relocating the spark plug's position to the edge of the squish flow region, or piston face or cylinder head redesign to optimize squish--could further enhance ignition performance.
Various versions of HBI and ICDI are currently being bench tested, and plans are being considered for a more complete set of engine tests at Chrysler.
Additional details...Contact Elaine Ward, Combustion Electromagnetics Inc., 32 Prentiss Rd., Arlington, MA 02174, (781) 641-0520
4 benefits of flow-enhanced spark
A higher peak voltage of 38 to 42 kV allows larger spark-plug electrode gaps that improve ignition and reduce electrode erosion.
Faster rise times, higher discharge energy, and higher circuit efficiency give greater resistance to spark-plug fouling.
Faster coil-charge time (1/10th that of SI) eliminates computerized dwell and makes HBI (the new system) universal. Retrofitting is easy on many different types of powerplants such as racing and performance, stationary natural gas, production vehicle, and other engines.
Rapid coil-charge time and a low-loss snubber substantially reduce switching losses and dissipation, despite HBI's higher energy and peak currents.
Two regimes of spark discharge
"Since the invention of the automobile, ignition-system theory hasn't moved beyond what I call the 'match-model,'" explains Ward. "The electric spark is just there to light the mixture and the subsequent dynamics of the combustion process depend on a relatively low AFR to develop power."
Standard inductive (SI) and capacitive discharge ignition (CDI) systems deliver only 30-60 mJ spark energy. That's about the same as Charles Kettering's first system introduced in 1910. Although SI spark ignites well-prepared, easy-to-combust mixtures, it does little to ignite highly dilute, and high EGR mixtures that provide the engine efficiencies and low NOx emissions that automotive engineers desire.
According to Ward, two regimes of spark discharge are associated with the release of inductive energy stored in the coil's core: "glow" discharge, that typically occurs for spark currents below 200 mA, and the "arc" discharge that occurs for currents greater than 200 mA.
Glow discharge, a low efficiency and low-electrode erosion "voltage-maintained discharge," has a relatively high voltage drop of 350V adjacent to one of the electrodes. The arc discharge, a higher efficiency "temperature-maintained discharge," typically has only 30 to 50V at the electrode.
Both discharges have a voltage gradient due to plasma between the electrodes. Voltage is a function of the flow impinging on the spark, because in a flow field the spark kernel is stretched and the spark-gap voltage rises with flow velocity in order to maintain spark discharge. This combined stretching and voltage rise continues until the spark segments, breaks up, and a new spark is struck. Voltage rise is much faster for glow discharge than arc discharge, and generally rises more slowly with higher arc currents. For instance, with a 300-mA spark current, the arc discharge may be able to sustain flows five times greater than what the 50-mA glow discharge can maintain.
How flow coupling works
Here's how Michael Ward's patented flow-coupling system works:
Steers the spark and initial flame front to increase the spark's effectiveness and reduce engine cycle-to-cycle variations.
Spreads and stretches the spark kernel creating microscale turbulence that distributes the spark energy over a larger volume. The higher the spark energy, the greater the spreading effect and the larger the initial spark/flame kernel.
Increases the ignition circuit's efficiency, so that more of stored coil energy is delivered to the fuel mixture.
Emission Standards & Car Test Results 10/9/92 |
EPA PROPOSED 2004 STANDARD |
1986 ESCORT 1.9l TEST CAR |
Ignition |
CDI |
SI |
ICDI |
HBI |
About the Author(s)
You May Also Like