Powder Metal Gets Parts in Shape
June 26, 1995
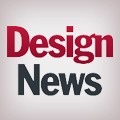
Princeton, NJ-What metal-forming process brings your part closer to final net shape, saves money, and lets you tailor performance characteristics? Powder metallurgy.
In the design of rifles, automotive fuel-injection systems, and computers, engineers are discovering the process efficiency and cost benefits of powder metallurgy (P/M).
The P/M parts business is maturing into a more solidly financed industry investing in new and more-sophisticated production equipment and improved quality control systems. The conventional P/M parts business, including in-plant operations, recorded an estimated $1.5 billion in sales in 1994.
More and more P/M parts are being designed into engines, transmissions and anti-lock braking systems (ABS). With a strong automotive year in 1994 when light-vehicle sales reached 15.1 million units, P/M experienced a substantial increase in business. GM, Ford, and Chrysler are all designing more P/M parts in North America and around the world. Hot spots include bearing caps and powder forged (P/F) connecting rods.
About 38 pounds of P/M parts go into the average Ford auto. This is expected to increase to 50 pounds by the year 2000.
Zenith Sintered Products, Inc., Germantown, WI, recently negotiated a five-year contract with GM for a new P/M steel bearing cap for its V-8 engines. Zenith has produced more than 10 million caps since the summer of 1993 for 3.1- and 3.8-l V-6 engines. Chrysler and Ford will join GM in designing with P/M bearing caps.
Ford is developing an engine bearing cap for the 3-l V-6 Vulcan engine. V-6 and V-8 engines can use between 4 and 14 pounds of powder in bearing-cap applications.
Near net shape. "One of the biggest benefits of powder metal is that the part is significantly closer to the final net part shape," explains William Jandeska, manager of P/M Technology for General Motors Powertrain division in Pontiac, MI. "Because of that, the part is less expensive overall, even though the blank is more expensive."
Powder forged connecting rods are replacing both cast and conventionally forged rods at the "Big Three." Twenty-five million conrods have been used in Ford engines without a failure-an enviable record.
P/F connecting rods are growing in popularity. Engineers designed P/F rods for the following Ford engines: 1.9- and 2.0-l 4 cylinder; 2.5-l 6 cylinder; and 4.6-l 8 cylinder 2-valve and 4-valve. In addition, P/F rods are slated to go into the new six-cylinder, 3.0-l engine for the 1996 model year and the Sigma engine to be made in Europe. GM uses P/F rods in the 4.6-l and 5.7-l V-8 engines, both operating in 1995 cars. GM is also considering P/F rods in its V-6 engines. Chrysler uses P/F rods in its 2.0-l and 2.4-l engines and is considering P/M in several new engines.
General Motors uses P/F conrods for the Premium V 4.6-l V-8 engines. The rods have an ultimate tensile strength of 110,000 psi, a yield strength of 50,000 psi, and an endurance limit of 40,000 psi. Powder metal contributes to important characteristics such as straightness, uniform microstructure, dimensional control, and superior machinability. P/M also eliminates surface defects inherent in conventional forgings.
Automotive parts such as bushings, filters, and oil-impregnated materials also benefit from P/M, says Jandeska. "With P/M, you get controlled porosity and other characteristics that can't be achieved with other processes," he adds.
P/M processes allow engineers to combine materials that can't typically be mixed together, such as aluminum with silicon carbide as the reinforcement for metal matrix composite. "This can be done by casting, but with the P/M process, you can have much finer-size silicon carbide to enhance the machinability and properties," says Jandeska.
For example, in GM valve guides, engineers use a ferrous material with hard phase formers for wear resistance and solid-state lubricants for lubricity. The materials are mixed together, pressed into shape, and sintered in an oven. "P/M accommodates a variety of different phases to offer different properties-in this case wear-resistance and lubricity," says Jandeska. "You can tailor the properties by mixing various different alloys or constituents."
Stainless-steel P/M applications are growing, especially for ABS sensor rings, which use 400-series grades. There is also a resurgence of interest in aluminium P/M among auto engineers as a way of meeting fuel-economy goals.
New techniques. Metal powder manufacturers are offering new products and improving the quality of materials. Many powder producers are pursuing ISO 9002 certification.
Several iron powder companies are pursuing warm-pressing technology for high-performance applications, which should open up new markets for P/M.
Water-atomized fine powder in many alloys is now available with higher tap densities. Engineers have developed new sizing technology to make very narrow size distributions for metal injection molding and other fine-powder applications.
P/M intermetallic iron alloys that resist high-temperature oxidation and nickel aluminides offer high-temperature strength and excellent corrosion resistance. Interest in better corrosion-resistant 300-series stainless steel continues to grow, and auto engineers are considering P/M for exhaust-system parts.
Equipment suppliers are in the forefront of upgrading P/M technology through improved or new production equipment or processes.
For example, engineers are using nitrogen-generated sintering atmospheres at customer sites. The technique is becoming popular because of its cost-effectiveness and convenience.
Compacting press suppliers are working more with powder and tool makers and customers to increase densities through higher-temperature sintering and improving densities through warm pressing.
MIM applications growing. The worldwide market for metal injection molding (MIM) is growing rapidly. U.S. sales of MIM parts are currently more than $60 million, with Europe at $15 million and Japan in the $35-50 million range. Japan is estimated to have as many as 100 companies involved in MIM. New automotive applications include parts for fuel-injection systems, anti-lock brakes, and airbag units. Additional markets include firearms, computers, and biomedical products.
For instance, Remington Arms Co., Ilion, NY, recently designed a .22 rifle around the advantages of metal injection molding. The rifle uses a MIM bullet magazine, trigger, and sight components. The one-piece complex magazine has a tensile strength of 55,000 psi and a 25% elongation. The part has sufficient strength in the feed lip area (open end of box) to resist deformation from .22 caliber cartridges while under pressure from the spring.
P/M will continue to erode the low- to medium-density machined forgings market by using new density-enhancing processes. With each gain in cost-effective density above 7.4 g/cm 3 a new range of applications opens up.
Engineers are also exploring brazing of P/M assemblies in new applications. There should be an increase in the use of brazed P/M assemblies which could open up more applications in 1995, especially competing against small castings.
All sectors of the P/M industry in 1994 recorded outstanding results. Metal powder shipments exceeded expectations with North American iron powder shipments soaring by 17.4% to 337,847 tons-a record. Overall iron powder shipments have increased by about 50% in the last three years. Copper and copper-base powder shipments experienced a much less dramatic increase of about 4% in 1994. The P/M business climate in 1995 looks equally good, with new parts being designed in many industrial and consumer products.
"Everything I see and hear is very, very positive about the current state of the P/M industry," says Armour Swanson, chairman of Zenith Sintered Products and president of the Metal Powder Industries Federation. "Most companies are increasing capacity to prepare for additional growth for applications now being tooled."
Powder metallurgy will continue to provide creative solutions to design and materials problems as engineers search out new and better ways to manufacture precision components.
About the Author(s)
You May Also Like