Model Makers
March 15, 2004
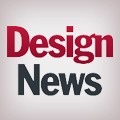
Divide and conquer. That's exactly what engineers at Medtronic Sofamor Danek did when they prototyped the company's latest surgical tool, a counter-torque ratchet that drives in spinal implant screws and then removes their heads. Rather than settling for a single rapid prototyping method, they divvied up the ratchet's eight parts and assigned each one to either a fused-deposition-modeling (FDM) or uv-jetting machine.
Both of these rapid prototyping technologies build physical prototypes by depositing modeling materials in thin layers that correspond to cross-sectional slices of a CAD model. But they do so very differently. FDM machines from Stratasys Inc. use computer-controlled extrusion heads to deposit thermoplastic modeling materials. The uv-jetting system, developed in Israel by Objet Geometries and now distributed by Stratasys, shoots droplets of a photocurable acrylic through a bank of heads that resemble those found on an inkjet printer. When exposed to uv-light, the acrylic cures and solidifies.
Why use both machines on a single project? "Each one has its strengths and weaknesses," explains David Freeman, rapid prototyping designer at Sofamor Danek's Memphis, TN development center.
Almost Functional
The main strength of FDM in this, and many other, applications comes down to its ability to turn out robust prototypes. Because it relies on commonly used engineering thermoplastics, including ABS and polycarbonate, an FDM machine can sometimes produce truly functional prototypes for plastic products. Sofamor Danek's ratchet, however, will ultimately be crafted in stainless steel, not plastic. Still, FDM did manage to turn out prototypes that might be described as "functional enough."
Sofamor Danek engineers used the company's in-house FDM machine to produce the surgical tool's six handle and internal ratchet components in polycarbonate. According to Richard Franks, senior product development engineer, the polycarbonate parts don't have the stiffness or strength to go into a fully functional model capable of generating enough torque to twist the heads off of the spinal implant screws. "Polycarbonate wouldn't break the screw," he says. "It would be something like tightening the bolts on your car with a toy wrench."
Yet Franks adds that the polycarbonate, unlike the majority of rapid prototyping materials, has enough robustness to serve in ratchet models that work well enough to be actuated and evaluated for human factors. He puts these nearly functional, "touchy-feely" models in the hands of surgeons who will ultimately use the tool. "It's better than having them try to visualize what the instrument will look like," he says.
The ratchet application ultimately required two FDM iterations. The first prototype seemed too big when Franks saw surgeons giving it a try, and his experience with stainless steel instruments told him it would have been too heavy as well. "So we went back to CAD and scaled everything down for the second iteration," he says, noting that the turnaround time for each iteration was about a day versus weeks in steel.
Beyond providing an early glimpse of how surgeon-friendly the tool will be, the prototype also plays a role in manufacturing. Franks says the FDM models serve as a good guide for the machinist when it comes time to produce the stainless steel prototypes that Sofamor Danek still relies on for its more stringent functional tests.
Fast Modes
While the bulk of the ratchet was prototyped in FDM, the extensions that connect the ratchet to the screws went onto the Polyjet machine. Freeman has a one-word reason why this pair of 6-inch-long concentric tubes were better off on the uv-jetting machine: "Speed."
Because it can squeeze more parts on the build envelop than the one-up FDM machine, the Polyjet machine does inherently have a throughput advantage, though not necessarily an edge when building a single part at a time. Freeman says he often gets five or six parts off the Polyjet machine in the time it takes to build one FDM model.
But he had another kind of speed in mind for this job. Support structures, which most rapid prototyping machines apply during the build cycle to support overhanging or hollow features, take valuable time to remove-sometimes more time than the build cycle itself. And supports inside tubes or any high-aspect-ratio hole take the most time.
|
With the Polyjet models, the supports break off when hit with a water jet, enabling a quick clean up of even inaccessible areas. FDM doesn't yet offer water-soluble supports for polycarbonate-though it does for some of its other materials. For Freeman, the difference really matters since the polycarbonate models would require a solvent bath and lots of bench work to clean up. "Every minute counts when you're trying to turn around models in a day," he says.
Material choices | ||
---|---|---|
Technology | Fused Deposition Modeling | Polyjet (uv-jetting) |
Material type | ABS | ABSi |
Tensile strength, MPa | 34.45 | 37.21 |
Elastic modulus, MPa | 2,495 | 1,963 |
Elongation at yield, % | >10 | >10 |
Notched Izod Impact, J/m | 107 | 176 |
Heat Deflection Temperature | n/a | n/a |
To learn more about these technologies and see footage of Medtronic -Sofamor Danek engineers, go to http://www.stratasys.com/BestOfBothWorlds
For more information on Stratasys' FDM and uv-jetting machines, go to http://rbi.ims.ca/3846-571
About the Author(s)
You May Also Like