Mentor Graphics Steers FloEFD toward Concurrent CFD
November 12, 2009
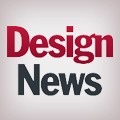
One year after its acquisition of Flomerics,a leader in CFD (Computational Fluid Dynamics) software, Mentor Graphics is building out its mechanicalanalysis capabilities to accelerate what it sees as a forthcoming paradigmshift in the market: The ability for concurrent CFD analysis as part of thecore mechanical design process.
In particular, Mentor is advancing its FloEFD software withnew features to accommodate this transition. FloEFD is CFD software that isfully embedded in the MCAD environment. A new release, targeted foravailability by end of this year, will incorporate a new feature for predictingcavitation effects in industrial liquids such as fuels and oils. Cavitation isthe formation and instantaneous collapse of innumerable tiny voids or cavitieswithin a liquid subjected to rapid and intense pressure changes. Cavitation isan extremely important condition in high pressure systems such as fuelinjectors, thus it lends itself to applications in the aerospace and automotiveindustries.
Mentor essentially sees two user profiles forFloEFD. The traditional profile, the CFD analyst, is formally trained in thediscipline (usually with a PhD), typically resides in R&D and runsdifferent models 10 to 20 times annually. This user type typically wants acomprehensive set of features packaged in a highly customizable fashion. Thesecond user type is where Mentoris targeting much of its latest efforts. This user, typically an engineer ordesigner, is formally trained in fields other than CFD and resides in design orengineering departments. This user will model many designs of the sameapplication over the course of the year, thus is looking for a highlycustomized set of features packaged in a highly-automated fashion.
That's where FloEFD comes in. The software is designed fromthe start to be fully embedded in an MCAD solution - the environment that ismost familiar to mechanical engineers and designers. "What an engineer ordesigner expects from CFD is a real-time, push-button, highly automatedsolution," says Erich Burgel, the new general manager for Mentor's Mechanical Analysis Div. "They wantsomething that is MCAD-embedded - a designer or engineer doesn't want to use orlearn a second language."
That's not the case with conventional CFD, which istypically not only a separate technology and application, but also a separateprocess. Because conventional CFD is a lengthy process, typically separate fromthe core design, companies perform fewer what-if variants and encounterpotential design problems when it is costly and time consuming to make changes.As a result, companies face longer design cycles, which means they could missout on market opportunities and they're building multiple prototypes, leadingto respins and higher development costs, Burgel says.
By embedding CFD analysis capabilities directly into thecore MCAD environment, FloEFD will address many of those inhibitors associatedwith traditional CFD and pave the way for that forthcoming paradigm shift."This is comparable to the shift we've seen over the last five to 10 years onthe FEA side, where people were asking for integrated and embedded FEAsolutions," says Burgel.
Mentor Graphics Steers FloEFD toward Concurrent CFD A
About the Author(s)
You May Also Like