Materials play on Xerox's copier/printer team
July 6, 1998
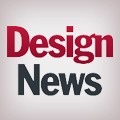
West Henrietta, NY--Most new products are the result of teamwork, and two new digital copiers/printers from Xerox Corp. are no exception. The copier/printer's development brought together worldwide partners to develop and design various parts of the machine.
Xerox 212 and 214 digital copiers/printers can print at 12 and 14 pages per minute (ppm), respectively. Xerox's Extended Enterprise created them, bringing together companies from all over the United States and the world with various specialties.
One of the main partners was Mack Design Inc. (Rochester, NY), a non-automotive injection molding company. Xerox moved engineers from Mack Design, as well as engineers from other companies within the Extended Enterprise creating parts for the copier/printer from their various locations, into its West Henrietta, NY, building to work on the copier/printer.
"The companies we were working with were right here. We were involved in almost every phase of the machine, so we were able to work very closely with companies who were literally sitting next door," says Bruce Ginder, president of Mack Design.
Ginder adds that since Mack had dimensional outputs or inputs of the copier/printer that affected other subsystems, the company could accommodate the design requirements of other companies within the Extended Enterprise, without dealing with companies in other locations and experiencing the usual communication problems of time differences, etc.
Xerox says it decided to create the printer/copiers from Cycolac(reg) acrylonitrile butadiene styrene (ABS) and Cycoloy(reg) polycarbonate blend (PC/ABS), made by General Electric Plastics (Pittsfield, MA), because of the materials' fire-retardant qualities, resistance to yellowing, and recyclability.
The copier/printer's cover top, rear cover, electronic console, and copy input module are made of Cycoloy, as are the platen cover and paper tray. All of the materials were injection-molded, Ginder says, and part of the reason they were selected is because they tolerance and mold well.
The material's resistance to yellowing and ultraviolet light is also important, Ginder adds, because the copier is painted in white and light colors.
Other applications for the materials include other business machines and consumer products such as children's toys.
Cycolac ABS characteristics
Here's a quick look at some of Cycolac GPM6300's properties
Melt temperature400 to 475F
Drying temperature180 to 190F
Drying timeTwo to four hours minimum,
eight hours maximum
Maximum moisture content0.1%
Tensile strength6,400 psi
Hardness on the Rockwell scale110
About the Author(s)
You May Also Like