March 3, 1997
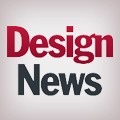
Sheboygan, WI--Conventional reciprocating wobble-piston pump/compressors work well in a host of applications. But the wobble-piston inevitably creates radial loads on the compression/pump chamber, and the arrangement can generate unwanted noise. Also, the axis of rotation of the motor driving the piston must remain at 90 degrees to the plane in which the piston moves. This setup requires a crank arm to drive the piston, and bearings that must be kept lubricated to make the system work properly.
William Harry Lynn, division manager, product engineering, at Thomas Compressors & Vacuum Pumps, sought to find a means of improving the basic wobble-piston technology used in the company's well-known Wob-L AETM pump/compressor. His approach combines swashplate, wobble-plate and wobble-piston pump technology to produce Thomas' recently patented Swob-L pump/compressor.
Lynn and his colleagues set out to eliminate the bearing surfaces and mechanisms required by wobble-piston pump designs. "The main challenge in developing the Swob-L pump involved eliminating as much as possible of the radial motion experienced by the piston as it moves axially in its cylinder," explains Lynn. "We also had to develop a method of dynamically balancing the new mechanism."
Engineers met these design challenges by reconsidering the classic wobble-piston layout. They positioned the Swob-L compressor's rod and eccentric assembly so that the motor shaft's axis of rotation intersects the axis of nutation of the eccentric assembly. It also intersects the eccentric's axis of nutation along the plane that passes through the piston seal's line of contact with the cylinder.
Designing the rod and eccentric assembly so that the center of mass also lies in this plane greatly reduces radial unbalance. Only the angular accelerations caused by the tilting of the rod and eccentric assembly require counterbalancing.
If you examine the drawings, you'll see that the motor shaft's rotation drives the nutation of a plate. Secured to the pistons, the plate causes them to reciprocate as the motor runs. In a double-ended Swob-L pump, with its opposite ends timed to move in exactly opposite directions, the tilting accelerations cancel out, resulting in a very good dynamic balance.
Dynamically balancing a single-ended Swob-l pump simply requires a rotating tilted mass that creates an equal and opposite acceleration to that of the nutating rod and eccentric assembly. As long as the product of angular acceleration and mass moment of inertia of the rotating counterbalance member equals that of the rod and eccentric assembly in all planes, the design achieves dynamic balance. "A simple disk with a tilted hole through the center, attached to the shaft and arranged to move opposite to the acceleration of the rod and eccentric assembly, is all that's needed for nearly perfect dynamic balance," Lynn insists.
Another advantage inherent to the Swob-L design, according to Lynn, arises from the flexibility involved with having multiple cylinders driven by one rod and eccentric-bearing assembly. Multistage compressor and/or vacuum-pump ar-rangements can be achieved by interconnecting a unit's intake and exhaust cavities, or completely separating the cavities to achieve various combinations.
Cylinder sizes, the distance from the central axis, and the eccentric's tilt angle can all vary to achieve a specific set of flow versus pressure requirements or vacuum requirements. "Design mods to satisfy niche OEM markets would not require major retooling to adapt a Swob-L pump," says Lynn.
The most recent prototype employs a single-ended, three-cylinder layout. Performance expected from this three-cylinder design is 3.5 scfm at 15 psig, using 1.70-inch-OD pistons. Stroke is 0.32 inch for the two-pole motor version and 0.64 inch for a four-pole motor version.
Additional details...James J. Kregel, Director of Marketing & Sales, Thomas Compressors & Vacuum Pumps, 1419 Illinois Avenue, Box 209, Sheboygan, WI 53082 (414) 457-4891.
About the Author(s)
You May Also Like