Engineering Materials Expand Potential for Digital Manufacturing
February 27, 2009
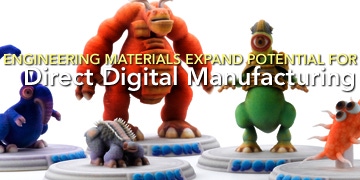
Thepotential for direct digital manufacturing is heating up as leading players addhigh-level engineering thermoplastics to their materials' lineups.
Stratasys,the leading supplier of rapid prototyping equipment by volume, is now teamingup Ultem 9085 poletherimide with new machines designed for direct digital manufacturing, which is theproduction of parts directly from CAD files. EOS is now offering PEEK(polyetheretherketone) polymer from Victrex for its laser sintering systems. Othermanufacturers, such as Z Corp. and 3D Systems, are developing strongerproprietary materials.
Ultemextends the digital manufacturing process into the aircraft market in a majorway. Until now, Ultem 9085 was only available for use in conventional processingmethods, such as injection molding, which require expensive tooling.
Manufacturingusing equipment originally developed for rapid prototyping createsopportunities for design engineers to make parts even more complex than ispossible with injection molds. The cost of the materials coupled with processingtime, however, will limit adoption, at least for now to low-volume parts.
"HavingUltem 9085 available for the FDM process will allow aerospace manufacturers toadopt direct digital manufacturing on a larger scale," says Jeff DeGrange, vicepresident of direct digital manufacturing at Stratasys (and formerly atBoeing). Ultem is strong, flexible and 5- to 15-percent lighter than interiorparts made with other plastics. It's an obvious fit for the new models such asthe Boeing Dreamliner where light weight is particularly valued.
""DDM caneven allow the production of parts that couldn't otherwise be manufactured withtraditional methods," says DeGrange. "This can improve the assembly, design andperformance."
Ultem 9085is heat-resistant up to 320F (160C) and is inherently flame-retardant, meeting important compliance standards such as OSU (OhioState University) heat release of less than 55/55, or 55 kw min/m2 for heatrelease and 55 kw/m2 for peak heat release.
Othertarget markets include the marine-product and automotive industries.
Special machinery too
Thematerial will be used on the FDM 900mc that was developed specifically fordirect digital manufacturing.
Stratasyssays the 900mc has an accuracy rating of ±.005 inch (or ±.0015 inch per inch,whichever is greater). "This rivals injection molding for accuracy andrepeatability," says Product Manager Patrick Robb. "For low-volume production,it's a more cost-effective technique than traditional manufacturing."Achievable accuracy, of course, is dependent on part geometry.
TheStratasys systems also work with polycarbonate, polyphenylene sulfone and ABSas well as other materials.
EOS is alsotargeting aircraft markets with the first PEEK polymer than can be processed onits high-end P 800 machine that was introduced at the end of last year in Germany.
"Thedevelopment of this system was a logical step forward into the future becauselaser-sintering is ideally suited for premium and complex applications whichare frequently based on high-performance polymers," says Dr. Hans Langer, thefounder and CEO of EOS, which is based in Kralling, Germany.
DesignatedPEEK HP3, the new material is fire-resistant and light, while possessing high tensilestrength. Besides aircraft applications, the polymer will also be aimed atmedical applications because of its biocompatibility.
Look forother new developments in the rapidly developing DDM market.
Web-made creatures
In one ofthe interesting spins, players can design unique creaturesusing the Spore Creature Creator withhundreds of flexible drag-and-drop body parts and a virtually infinite numberof possible configurations. Players can then digitally paint their creatureswith unique patterns. Players can then upload their digital creations towww.sporesculptor.com and place their order. The ZPrinted models (up to 4inches tall) will be shipped directly to consumers.
Electronic Arts sells the Spore Sculptures for $49.50.
Z Corp.uses various powder/binder/infiltrant systems to make parts. The strongest forindustrial uses are high-performance composites, such as zp 131. Z Corp. usesan inkjet printer system that combines binders and powders.
About the Author(s)
You May Also Like