February 8, 2011
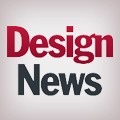
A retrofit of the Army's MLRS vehicle, arocket launcher which carries up to 12 rocket pods, involves the insertion ofelectric drive technology into an existing hydraulic application that requireshigh torque and fast dynamic response. The new electric system also provides astrategic advantage by offering silent operation and eliminating the need torun the vehicle's diesel engine to operate the launcher.
"What we were able to demonstrate is that electric drives,historically considered small and limited in load carrying capacity, coulddrive a system which has to move approximately 12,000 pounds," says KevinEschner, senior project engineer for Moog Inc.
Electric Drives Power Rocket Launcher_C |
The MLRS is a high-mobility automatic system based on the M270weapons platform manufactured by Lockheed Martin Missiles and Fire Control.Without leaving the cab, a crew of three is able to fire up to 12 GMLRS (GuidedMultiple Launch Rocket System) rockets in less than 60 sec from a distance of42 miles or two ATACMS (Army Tactical Missile System) missiles from a distanceof 180 miles.
Moog took the lead on the systems integration of the MLRSretrofit project, converting the launcher drive system from hydraulic toelectric over the course of six months. The new system eliminates existingproblems on the MLRS including leaks, complex troubleshooting, repair andmaintenance work.
"The new system uses two motor controllers and three electricdrive motors to control the rocket launcher that sits over the back of thevehicle," says Eschner. One drive controls the Azimuth to rotate the launcher,and two motors in series control elevation or lift to generate the requiredloads."
Redesign with FewNoticeable Changes
In the Army'straining, war fighters under fire are taught not to think about what they'redoing. The goal is reacting and letting the training take over, so the soldiersfunction at optimum speed and efficiency. Since the crew had experience withthe existing MLRS, few changes to the interface were desired. Therefore, thedesign constraints for the retrofit project included using existing interfacesand minimizing maintenance once the system was switched over to the electricdrive system.
"We kept exactly the same controls and exactly the same manner ofoperating the system," says Eschner. "Effectively, the user doesn't know thereis an electric drive system except that the system has the significantadvantage of silent operation."
The existing hydraulic design required running the large dieselengines on the vehicle, at all times, to operate the launcher. Because the crewsits over the top of the engine, heat becomes a major factor, especially if thecrew is in Iraq or Afghanistan in the middle of summer, with no built-in airconditioning in the vehicle. Studies show that crew performance drops off withhigher temperatures, especially when they are in the vehicle anywhere from 10 to 12 hours a day.
Silent operation is also very useful from a strategic standpoint.With the ability to move the launcher electrically, the Army can move thevehicle without running the diesel engine and creating a heat signature. Butonce they fire a rocket, they expose their position and the launcher becomes atarget. So the mode of operation becomes "shoot and scoot."
"What they liked about ourdesign is that they could actually deploy the vehicles months ahead of anyinitiative and never fire the diesel up, so they had no heat signature on thevehicle," says Eschner. "We drive completely off a set of batteries, and thefire control computers also run on a secondary set of batteries. Once in place,the system can become totally silentand blend into whatever background with no heat signatures."
Motion Control Design
The major challenge in designing the motor/drive systemis the size of the load to lift. In addition, the application was locked into a28V motor performance system. Unable to take a white sheet approach to thedesign, the engineering team had to work within the confines of a restrictedspace for the motors, drives and mechanical linkages. The goal was to keep mostof the existing mechanical linkages and substitute the electric drives for thehydraulic drives.
"If we had designed the system from the ground up, we would haveintegrated most of the transmissions and gear boxes within the actuators anddelivered an overall smaller package. But this would have been a more costlydeliverable from a retrofit standpoint," says Eschner.
In the final solution, two electric drives used in seriesgenerate the required elevation torque. To achieve that within the Moog productline of both single- and dual-axis motor controllers, they modified one oftheir dual-channel commercial boxes. By linking channels together in software,two units drive together to achieve thehigher torque requirements. The Azimuth axis uses a single-axis controller.
The system also required redundant braking beyond what would benormal for an electric drive system. Extra electric brakes engineered by Moogcould be controlled with the same motor controllers. The result was a compact motor controller using parallel channelsand coordination between the two control boxes.
An added advantage to the use of electric drives is eliminatingthe need to transport, use and store hydraulic liquids. Leakage is always anissue with hydraulic systems, and contamination is a major concern especiallywhen maintenance on vehicles is done out in the field. Electric drives, on theother hand, are sealed and a line replaceable approach means that if componentsfail there isn't a huge amount of troubleshooting needed.
Even with those advantages, the primary goal of the retrofit wasto make the operation of the electric system invisible to the crew. Eschnersays that when they brought in a colonel and a number of soldiers at the end ofthe demonstration project, the gunners who drive and operate the vehicleprovided the best compliment. They told Eschner, "If you didn't tell me thiswasn't one of my hydraulic systems, I wouldn't have known."
With the motion system itself, engineers worked to meet therequired velocities, while contouring the acceleration curves and reducing someof the stresses on the elevation cage. The existing hydraulic system hadprovided a power dense solution, but there was less flexibility in controllingthe motion profiles using the hydraulic system.
"It's more difficult to adjust velocity curves and accelerations,and there are some very violent moves within the operational constraints of thevehicle," says Eschner. "We were able to mimic those moves to get the desiredrates and velocities but, near the end of the accelerations, we had to lowersome of the g levels to help with reliability and uptime."
Moog created simulations using MatLab Simulink to initiallycharacterize the cage motions, and downloaded optimized tuning parameters fromthe simulations into the controllers. This provided a good start for the finaltuning which was done with a group of engineers. All of the interfaces werealso designed to integrate with the hydraulic launcher drive's interlocks,including weapons ready for firing, and also locking in GPS signals. All of theinterfaces were developed using a modified off-the-shelf version that pluggeddirectly into the existing system.
About the Author(s)
You May Also Like