Coating help for highly-loaded parts
December 2, 1997
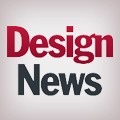
North Tonawanda, NY--Demanding performance criteria related to weight reduction and fuel consumption can subject engine components to exceptional loads and wear. The most important wear mechanism which occurs on highly-loaded sliding or rolling parts is adhesive wear, or cold welding.
To prevent metal transfer from one sliding face to the other, wear surfaces require abrasion resistance as well as a low coefficient of friction. At the same time--despite the hardness demand--such surfaces must also be deformation resistant.
Coating load-bearing components of an axial piston pump with WC/C improves performance with less lubricant. |
Carbon coated components, when compared to nitrided, nickel-, and chromium-coatings, exhibit improved wear-resisting performance. In particular, Balinit(R) C Tungsten Carbide/Carbon (WC/C) coatings are claimed to offer the proper combination of low coefficient of friction and high hardness needed by highly-loaded automotive and machine parts.
Developed by Balzers Tool Coating Inc., Balinit C WC/C coatings are made of hard tungsten carbide particles in a soft amorphous carbon matrix. Ion bombardment of a tungsten carbide target removes coating material for deposition onto component surfaces under controlled conditions. Several applications demonstrate the material's ability to solve wear problems:
Hydraulic pumps
Coupling performance needs with environmental considerations can create situations where something's got to give. Consider axial piston pumps. Designing for higher pressures and velocities, while at the same time accommodating environmentally friendly lubricants and pressure fluids, may promote wear and lead to eventual leakage or seizure problems. Components most affected: pistons, valve plates, and sliding shoes.
Unfortunately, the tribological load-bearing capacity of nitrided steels or bronze--conventional material pairs used in hydraulics--do not always meet today's conflicting performance demands. Add-on solutions like optimized filter configurations can help, but usually at more cost and maintenance.
A coating of tungsten carbide/carbon, specifically developed for highly-stressed machine components operating under less-than-optimum lubricating conditions, gives design engineers a way out of such predicaments. Produced by physical vapor deposition, WC/C is said to improve seizure resistance and reduce failure due to particle-contaminated hydraulic oils.
Increasingly, anti-friction (AF) coatings are used to supplement standard lubricating oils, greases, and pastes. Dry-running tests with pin-disc-tribometers show superior performance of WC/C coatings when compared to organic resins, sputtered MoS2, or blasted WS2 coatings. |
"Pump pistons coated with Balinit C," claims Fred Teeter of Balzers Wear Protection Division, "operate longer than nitrided pistons or nickel- and chromium-coated pistons." Teeter adds that replacement of sliding shoes made from bronze with Balinit C coated steel also cuts down on wear.
Application results in a low coefficient of friction and "smoothing" of the part's surface. Hardness measures 1,000 VHN (25g); thickness is approximately 3 microns.
When measuring seizure load capacity on a standardized FZG-A test bench, Balinit C reaches the highest possible level without significant wear marks. |
Gear and gear drives
Different wear mechanisms occur at gear flanks. Gears operating under severe loads are subjected to both cold welding and pitting. While the low coefficient of friction of a WC/C coating (0.1 - 0.2 against steel, dry) increases resistance against cold welding, the more severe wear mechanism is pitting.
Pitting, or surface fatigue, occurs under high loads or after long working periods. The damage starts on surface notches or small inclusions beneath the surface by crack formation under the cyclic load of a running gear. Growing cracks cause particle flake-off leading to the typical pitting structure.
In tests comparing an uncoated, case-hardened gear to a Balinit C-coated gear, Balzers reports that the WC/C coating increases service life by a factor of two. This, says the company, corresponds to an increased load bearing capacity of 10 to 15%. Improvement is attributed to the excellent running in and smoothening properties of the Balinit C coating, lowering the actual hertzian pressure.
Balinit C WC/C coatings, with a maximum working temperature of 300C (570F), are presently used in racing, as well as industrial gear systems.
For more information, contact Frederick Teeter, Balzers Tool Coating Inc., 661 Erie Ave., North Tonawanda, NY 14120. Call 1-800-828-6344 x011
About the Author(s)
You May Also Like