November 3, 2003
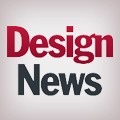
Those who have pumped up large pneumatic tires by hand know that a lot of effort is expended, most of which is stored as PV work. This work is best dissipated by slow deflation. The breaking of a tire bead or the expulsion of the ring on a split rim leads to sudden decompression and possible loss of vital body parts of those unfortunate enough to be nearby. The internal pressure also gives a large overturning moment against the flanges of a single piece rim. An ensuing fatigue failure will give sudden, possibly catastrophic deflation.
Years ago in Oregon a sudden tire deflation sent a truck head-on into a passenger car, with disastrous results. Post accident analysis showed the one-piece rim to have a circumferential split where the flange meets the bottom of the rim. The widow of the deceased sued the manufacturers of the tire and rim, both major corporations. The manufacturer of the rim retained me.
Radial tires flex differently than bias ply tires, a difference reflected in the loading of the rim. The rim manufacturer claimed that the radial tires gave too high stresses, hence must not be used on their rims. The tire manufacturer pooh-poohed this stricture, claiming that its tires were entirely suitable for the rims in question.
The lawsuit boiled down to two questions: One, was the rim of acceptable materials, design, and manufacture and, two, was use of the radial tire acceptable practice? The rim manufacturer hired me to investigate the metallurgy of the rim.
Most dynamic failures are due to fatigue. The repeated application of a stress creates a crack, which lengthens with each cycle. At some point the crack is so long that sudden fracture occurs. Fatigue failure is usually associated with a relatively smooth fracture surface with so-called "beach" or "clam shell" marks and typically occurs at a stress a bit under half that which gives failure after one application. Good engineering design of components subject to repeated loads must factor in this reduced strength.
The rim had fractured at the angle between the flange and bottom, where the stress was the greatest. Plentiful markings on the fracture surface indicated a fatigue failure. Magnetic particle examination revealed numerous other cracks, which would, in time, have caused failure. But a tire rim is designed to resist fatigue failure: Why did this particular one fail?
An opposing expert found a nonmetallic inclusion in a polished section of the rim. Such inclusions form during de-oxidation of the molten steel and are unavoidable. They are simply part of the steel. But this expert treated the inclusion as the Antichrist, accusing it and its ilk of responsibility for the failure.
My client opted to pay for fatigue tests on the rim material. A student did the actual testing, which is arduous and expensive. The steel displayed excellent fatigue resistance.
The trial was in Eugene, Oregon, a rural area. My client's attorney used an ingenious strategy during my direct examination to eliminate any impression that I was some high-toned Eastern expert flown in to lord it over the country folks. Without warning me, he proceeded to ask about my upbringing on the family farm and helping out my father even after going off to college. With the snob factor out of the way, my extensive fatigue testing was far more convincing than the opposing expert's single microscopic observation. Other experts testified to the quality of design and manufacture and to the unsuitability of radial tires for the subject rim. My client came out of the case in good shape.
Ken Russell ([email protected]) is Professor Emeritus of Metallurgy and Nuclear Engineering at MIT. He specializes in physical metallurgy, forensic metallurgy, and failure analysis. Cases presented in this column are drawn from his actual files.
About the Author(s)
You May Also Like