Automation comes to India's railway
July 22, 1996
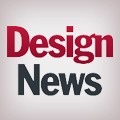
New Delhi, INDIA--On the Indian Railway, where bare-footed "key men" walk eight miles of rail a day, knocking bolts into place with sledge hammers, manual labor is the norm. Most of the country's railway laborers can only dream of the levels of automation in other areas of the industrial world.
Now, however, that's changing. This summer, a hulking 118-foot-long, automated machine will arrive in India, where it will take up the task of cleaning the mud and debris from thousands of miles of Indian track bed. The 200,000-lb machine scoops up the stone, or ballast, on the track shoulders, sifts out the dirt and debris, and redeposits the clean product. It's an extraordinary process, one that eliminates the need to close down sections of track for prolonged periods. "A tremendous amount of work is accomplished and a lot of track is treated in a very short period of time," notes Royce Kershaw, Jr., president and CEO of Kershaw Manufacturing Co., Montgomery, AL, the machine's manufacturer.
Indeed, the ballast cleaner needs only three hours to accomplish a task that used to take weeks. And it does so with only two machine operators, rather than 50 men with shovels. In the process, the machine offers the potential to streamline railroad operations around the world. It reduces the need for costly strip mining to obtain crushed limestone or granite for new ballast. And it cuts costs for the transportation of such material.
In that sense, the famed Indian Railway has placed itself at the cutting edge of railroad technology. "The idea of recycling ballast has grown more appealing in recent years," Kershaw says. "As the reliability of these machines is proven, we're optimistic that the technology will be widely accepted around the world."
Cheaper to recycle. Bringing the technology to its current level has been no easy task. Kershaw's father, Royce Kershaw Sr., invented one of the first ballast cleaners during the 1940s. Then, as now, the machines removed trapped mud, water, and debris from the ballast, enabling it to more effectively support the weight of passing trains.
When the technology was introduced in the 1950s, however, railroads were generally slow to accept it. During the 1980s, that changed. As ballast costs climbed and technology costs plummeted, ballast recycling looked like a more viable option. At the end of the decade, Kershaw worked with British Rail on the development of a High Output Ballast Cleaner (HOBC)--a step that many railroad managers considered necessary for the technology to reach its ultimate acceptance.
The HOBC concept formed the foundation for the Indian Railway machine, which Kershaw Manufacturing started designing in the fall of 1994. From the outset, the Indian machine was intended to operate and travel at higher speeds. Engineers wanted the machine to clean ballast at a rate of 600 cubic meters per hour. And they wanted it to transport itself at a top speed of 55 mph, twice as fast as earlier counterparts.
But, when Kershaw engineersset out to design the new unit in 1994, they wanted to do more than endow it with high speed. They wanted it to be simpler, more reliable, and easier to assemble than earlier versions. And they had to produce a design that would overcome specific environmental challenges in India, such as searing heat, widegauge track, and low bridge clearances.
Accomplishing all that required the incorporation of a number of new technologies--a stiff challenge for engineers building such a large machine. They began by specifying technology that would enable them to eliminate the vast amounts of plumbing and wiring, as well as the large number of actuators required on previous machines. Still, their new ballast cleaner would eventually employ more than 50 hydraulic cylinders, 10 pumps, and 67 control valves.
System simplicity. In the past, Kershaw's ballast cleaners had used fixed diplacement-type pumps and manually operated, open-center valves to operate the excavating wheels, conveyors, and hydraulic cylinders. This required numerous adjustable flow control valves and relief valves to control the oil pressure and flow to various hydraulic motors and cylinders. Since the valves were manually operated, they needed to be within easy reach of the operators. As a result, the machines typically used large bundles of hoses, which ran for long distances.
Kershaw engineers worked with Vickers engineers to simplify the machine by employing PVH variable displacement load sensing pumps. The conveyors and excavating wheels are controlled with solenoid-operated Vickers CMX-160 valve banks. Cylinder operations on the machine are controlled with Vickers DG-Series (CETOP-3 and CETOP-5 Series) stack valves. The combination of valves and pumps eliminate most of the flow control and relief valves, which, in turn, significantly reduce the required number of hoses and fittings.
Use of an Allen-Bradley SLC 5/02 Programmable Logic Controller permits remote operation of input/output modules. One rack, located near the machine's primary operator, houses I/O modules and the PLC. Another rack, at the secondary operator's console nearly 80 feet away, houses only I/O modules. A two-conductor shielded cable provides the sole link between the racks.
Using a PLC with remote I/O, instead of conventional hard-wired controls, console switches needed only to be wired to a nearby input. Valves and relays are wired to a nearby output module. In contrast, conventional hard-wired controls would have required wires running the full length of the machine, from the valves and relays on one end, to the switches on the console at the other end.
By configuring the control system in this way, Kershaw engineers used only 20,000 feet of wiring. In contrast, similar machines had previously used about 60,000 feet of wiring. What's more, this vastly reduced the number of control relays, as well as the jumper wiring between them, by the use of PLC programming.
To make the transition from relay logic to the PLC design, Kershaw engineers worked with Allen-Bradley's technical staff. An existing relay logic ladder served as the basis for the PLC program.
Close work with suppliers. Throughout the design process, Kershaw engineers stayed in touch with engineers from Vickers and Allen-Bradley. By working closely with Vickers' staff, they could determine optimum flow rates and pressure drops. Allen-Bradley's technical staff helped with the vast number of inputs and outputs, the hardware switch settings, and the programming of the controller's software.
Although software programming was more extensive than in previous projects, Kershaw engineers say that configuring the machine in this way was still to their advantage. "We saved so much time on hard wiring that we still came out ahead in terms of time," explains Andy Loftis, engineering manager for Kershaw.
Major modifications. While Kershaw engineers laid out the new electro-hydraulic configuration, they also worked on a series of problems specific to the Indian machine. Foremost among those were the size changes: The Indian Railway used a wider-gauge track (66 inches) and minimum bridge clearances that were about 21/2 feet lower than those of the U.S. railroads.
For Kershaw's engineering team, the new sizes meant that the excavating, conveying, and screening units had to be redesigned. What's more, they now had to accommodate the higher ambient temperatures of India's searingly hot desert regions. "When we embarked on the design of this machine, we knew we would have to change many of our existing designs," notes Al Wimbish, a Kershaw project engineer.
To solve the size problems, Kershaw engineers produced concept designs of new screening units and worked with Telesmith, Inc., Mequon, WI, to resize the shaker screens. They also worked with the technical staff at Vickers to check hydraulic fluid heat. Finally, they teamed with engineers at Cummins USA and American Industrial Heat Transfer, Inc., Zion, IL, to resize the oil cooler for the machine's VTA-28, 800-hp engine. As a result, the modified engine can stand up to the 130F heat of India's plains.
Building a foundation. By the first quarter of 1996, when Kershaw engineers began assembly of the finalized concepts, it became clear that the new machine was a significant step forward. The machine's wiring had been reduced from 60,000 to about 20,000 feet. It cut the number of elec-trical relays, hydraulic pumps, hydraulic hoses, and hydraulic fittings. The result: elimination of a vast numbers of potential leak points, fittings, hy-draulic pumps.
"Overall, we estimate that we reduced the number of hoses and fittings by 30%," Loftis says. "And if you reduce hoses and fittings by 30%, it means that you have eliminated a lot of assembly time."
What's more, Loftis says, Kershaw's engineering team had implemented improvements to the machine's excavating wheel, screening system, conveyors, and ballast box. Those innovations, he promises, will carry over to the design of future machines.
This summer, a Kershaw operator will drive the machine down the tracks from the assembly plant to New Orleans, where it will be loaded on a ship for its one-and-a-half month journey to India.
Back in the U.S., meanwhile, engineers are already describing the machine as a 21st cen-tury version of ballast recycling concept. "From the previous machines to this machine, we can see a light-year jump in technology," concludes Loftis. "This is a good foundation for all of our future projects."
The basics of ballast cleaning
The wheel of a typical train car can create loads in excess of 50,000 psi, all of which is transferred to the gravely ballast beneath the rails. To effectively support those loads, the ballast must be clean--that is, free of mud, dirt, and debris.
To perform this task, Kershaw's ballast cleaner is powered by an 800-hp Cummins engine and a variety of hydraulically actuated components. The main implements include the excavating wheels--spinning, eight-foot diameter steel wheels located on both sides of the 118-foot-long machine. The wheels scoop ballast from the track shoulder, then place it on a series of conveyors that transport it, screen it, separate it, and replace the clean material.
Hydraulics power the in-out, up-down, and tilt motions of the excavating wheels. They also raise and drive the conveyors, open and close a ballast distributor box, move the ballast wings and broom, and operate a device called a scarifier, which cuts material from beneath the railroad tie ends.
During the process, mud, dirt, and debris are removed from the ballast, allowing it to be recycled. As a result, railroads can reduce their material and labor costs, as well as increasing their up-time.
Timeline for Design
Fall 1994 Concept drawing done for Indian Railway machine
Spring 1995 Engineers settle on hydraulic,electrical, and structural concepts
Summer 1995 Engineers begin subsystem designs
Fall 1995 Finalized development of subsystems
Summer 1996 New ballastcleaner shipped to Indian Railway
Spring 1996 Assembly of finalized concepts
About the Author(s)
You May Also Like