October 29, 2015
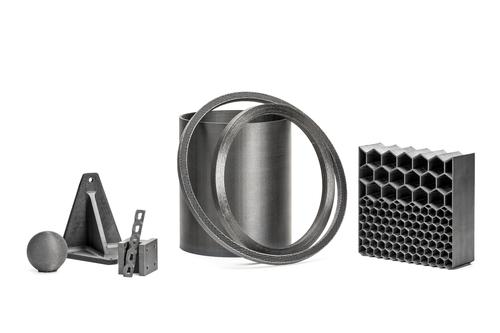
Several companies have used 3D printing (3DP) to make carbon composite parts, with different levels of quality and success. Arevo Labs, which we told you about last year, is developing proprietary 3DP technology to create better thermoplastic carbon composite materials and end-use components. The company was in R&D mode until this week [[October 13]]. Now it's offering a commercial on-demand service for manufacturing 3D printed, optimized, PEEK- and PAEK-based carbon composite production parts.
The aim of the company's Reinforced Filament Fusion Technology is to serve extremely demanding end-use applications like aerospace, single-use medical devices, oil & gas, and factory automation, Arevo Labs CEO and founder Hemant Bheda told Design News. The company has already created end-use parts in all these application areas, and is now working with OEMs to scale up production.
Matternet 3D prints its drone's arms with SLS, but the company also had an arm printed with Arevo Labs' process, said Bheda. That processes depends on fused filament fabrication since it produces stronger parts. "I can confirm that the drone arm printed with Arevo's Katevo-CF material with no internal structure is much stronger than a carbon fiber-filled SLS arm with inner ribs," said Ido Baruchin, head of design at Matternet, in a press release. The Matternet ONE is billed as the first smart drone for transportation in last-mile logistics. The Katevo-CF material is a carbon fiber-filled PEEK composite.
The composites unusually combine a high-performance polymer matrix like PAEK or PEEK, filled with carbon nanotubes, carbon fiber or glass fiber. As Bheda and his colleagues explained last year in a Design News article, to make this possible they've reinvented how the 3DP process works. The new technology is primarily materials and software, including a printer head design and firmware optimized for use with reinforced materials.
READ MORE ARTICLES ON 3D PRINTING:
Currently, two types of printers the company built for its Reinforced Filament Fusion Technology 3DP process are producing parts. The first, with a 12 x 12 x 8 in build volume, is for medical parts. A larger one, with a 30 x 30 x 30 in build volume, produces larger components, such as for aerospace, said Bheda.
Making carbon fiber composite parts using additive methods has several advantages over traditional methods, such as being able to control fiber orientation more precisely than is possible with processes like injection molding. Each layer can be constructed with a different fiber orientation. Materials can be tailored to optimize various combinations of thermal, mechanical, and electrical properties for a particular application, said Bheda. This tailoring is done with Arevo Labs' intelligent, cloud-based design optimization software, using its finite element analysis (FEA) algorithm to evaluate part geometry, material properties, hardware capability, and toolpath orientations.
These tailored materials achieve high performance thresholds for strength, stiffness, durability, wear resistance, chemical resistance, thermal stability, and ESD characteristics. You can find out more about them, including a graph showing tensile modulus and strength, on this page.
Factory automation-related applications are starting to see more traction, said Bheda. One customer has used the service to make jigs and fixtures for automotive assembly on the factory floor. Another, a large electronics firm, has used it to produce test fixtures for use in an automated line. In both of these applications parts are made from Arevo's Quantevo-ESD material, a carbon nanotube-filled PAEK composite.
Design News will be in Minneapolis and Orlando in November! Design & Manufacturing Minneapolis will take place Nov. 4-5, while Design & Manufacturing South will be in Orlando Nov. 18-19. Get up close with the latest design and manufacturing technologies, meet qualified suppliers for your applications, and expand your network. Learn from experts at educational conferences and specialty events. Register today for our premier industry showcases in Minneapolis and Orlando
Ann R. Thryft is senior technology editor, materials & assembly, for Design News. She's been writing about manufacturing- and electronics-related technologies for 27 years, covering manufacturing materials & processes, alternative energy, and robotics. In the past, she's also written about machine vision and all kinds of communications.
About the Author(s)
You May Also Like