A Speedy Machine for Wafer Makers
August 18, 2003
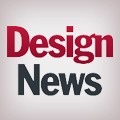
Modern photolithography machines must deliver extraordinary precision on a repeatable basis, and in high volume production. In response to demands for increased throughput in the semiconductor industry, ASML (www.asml.com), a Veldhoven-based Dutch equipment maker, recently launched its Twinscan photolithography machine. The $10 million device can process two 300-mm wafers simultaneously, but in separate operations: metrology on one side, exposure on the other.
Two-Step Process
All photolithography processes require two steps: metrology first, followed by exposure. During the metrology stage, the machine automatically constructs a nanometer-scale 3D map of the wafer surface, using laser interferometers to measure reference points implanted on its surface. Without the surface map, the wafer can't be exposed precisely, but this step almost doubles the amount of time the wafer spends at the lithography station.
The most important part of the photolithography process-the reason why the machine is there in the first place-is to expose the wafer to the reticle pattern of the chip to be produced. "The step-and-scan sequence has already been perfected on previous generation machines, but it now moves into high gear on the dual-stage Twinscan," says ASML Sales Engineer Stein Kurstjens.
|
The exposure operation resembles what goes on in a photographic darkroom, with some important differences. Lithography lenses are massive structures, 1m long and 30 cm wide, consisting of a dozen or so glass elements. The laser light source is in the deep ultraviolet part of the spectrum, and invisible to human eyes. The photographic "negative" is actually a reticle, or photo- mask-a 6 x 6-inch quartz plate with the image of what the semiconductor manufacturer wants to print on one layer of the chip. If the final wafer has 30 layers, then there will be 30 photomasks. The quartz plates each cost about $10,000 or more, so a multi-layered chip will involve significant investment in photomasks even before the first chip is made.
Scanning and stepping are complete, high precision motion operations. During exposure, both the wafer and the reticle are constantly in motion. The system is either "stepping" between one die position and the next, or it's following the scanning position of the die image. Hundreds of die positions are stepped and scanned in less than a minute. Thirty seconds is typical.
The lithography system scans the image because the image on the reticle is too large to send through the lens at one time. Instead, the reticle is moved past a rectangular slit that allows only one part of the image to go through the lens. At the receiving end, the wafer has to move in perfect coordination with the scanning operation going on one meter above it to capture the constantly changing image as it comes through the lens. The reticle and the wafer must accelerate and decelerate in millisecond intervals with almost perfect synchronization.
Economical Motion Control
|
Why is it necessary to have such precise coordination in the scanning operation? The answer is simple: motion control is cheaper than optics. The lenses are the single most expensive component in the machine, costing over $1 million each. Making the lens larger is cost prohibitive; it is cheaper to design a complicated motion control system to work around the limitations of the optics.
Layered on top of the step-and-scan motions is yet another set of servomotors coupled with laser interferometers that continuously adjust its x, y, and z positions. These motors are in fact tracking the 3D "wafer map" that was made during the previous metrology stage of the process and are working to accommodate distortions in the wafer itself. The machine has to keep the wafer surface in the focal plane during exposure because the depth of focus of the lens is only on the order of a few hundred nanometers.
In previous generation step-and-scan systems, leveling information required to focus the image was determined while scanning the image. The big advantage of the Twinscan is that the wafer plane height is measured prior to exposure and the height information is used during exposure to position the wafer surface exactly in the focal plane.
Good Vibrations
Doing two motion control operations simultaneously, and then passing a large silicon wafer between internal stations, is bound to send ripples of vibration into machine areas where zero tolerance is the absolute requirement. Even minute vibrations can have a detrimental effect on the ultimate imaging performance of a lithography system. Boudewijn Sluijk, a development engineer who worked on the project, says ASML engineers overcame this problem with a novel "force balance" technique.
Two separate frames-the metrology frame and the base frame-form the basis of the design. To ensure a stable image and stable measurements, the lens and the metrology equipment are mounted on a metrology frame that is fully isolated from outside disturbances. The metrology frame sits on three actively controlled air mounts. Hardware that could disturb the stability and integrity, such as moving parts and heat sources, are supported by the base frame.
"The rapid accelerations required by the scanning operation are exerted on a balance mass, rather than being dissipated into the base frame," says Sluijk. "If these forces would be exerted on the base frame, the ultimate scan accuracy would be limited despite the vibration isolating air mounts."
The long-stroke motor that drives the stage operates between the stage and the balance mass. The motor force moves the stage in the desired direction, while the reaction force moves the balance mass in the opposite direction. The external forces from this sub-system on the base frame are negligible. To prevent the balance mass from drifting away, a low bandwidth drift control loop can make small corrections. This cancellation of reaction forces from scanning and stepping motions not only improves the dynamic behavior of the system itself, but also limits the vibrations that could lead to disturbance of other step-and-scan systems and other sensitive equipment on the fab floor.
Actuators operating in the millimeter range provide the ultimate positioning accuracy of the stages. (Long-stroke actuators, which can travel distances of up to one meter, do not provide sufficient accuracy to control the stages at nanometer levels.) Stages are positioned relative to the optical axis by taking differential interferometer measurements from the lens-bottom (for the wafer stage) and the lens top (for the reticle stage). The stage positions are measured in six degrees of freedom, and the stages are positioned with contactless actuators (Lorentz, or voice coil motors), also with six degrees of freedom. These short-stroke motors isolate the stages and exert a force that is to a first order independent of the relative position of the stationary magnet and the magnetic coil.
Ultimately, this attention to basic system dynamics sets the stage for the next step in the semiconductor industry's basic roadmap: 70-nm circuit-feature size manufacturing.
About the Author(s)
You May Also Like