Racing designers improve the breed
May 3, 1999
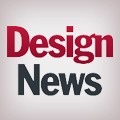
WHAT'S THE MOST IMPORTANT PART OF A RACE CAR?
According to car developer Reeves Callaway, it's the tires--"The car exists as a way to make the tires work. How well it uses its tires is the single most important part of an automobile." This ex-race driver and head of Callaway Cars (Old Lyme, CT) knows--both from experience and, for the last 20 years, from developing performance engines and cars. The firm's latest creation is the Callaway C12, a sportscar that goes from zero to 60 mph in under 4.3 sec and tops out at 188 mph. Built as a road car, it will race in the world's premier 24-hr endurance race at Le Mans, France, most likely in the GT2 (Grand Touring) class, which requires that entries be based on street-legal production automobiles.
The C12 is derived from the latest, fifth-generation Chevy Corvette, effectively using the widespread base of GM performance components. It is powered by a 440-bhp Callaway SuperNatural(R) LS1 engine, a naturally aspirated V8, itself based on the Corvette powerplant that puts out "only" 345 horses. In the race car, the engine is further modified (with changes to the head, manifolds, exhaust, compression ratio, porting and combustion, and cam timing) and pumps out 610 bhp.
But despite such performance, Callaway emphasizes, "The engine is not the most important part of the equation. Sure it must be reliable so that you don't even have to think about it--you're stupid or unlucky if it fails in an endurance race." The reason he says is this: In Le Mans racing, as in most racing classes, engines are restricted in order to boost competitive racing that keys on driver skills. At Le Mans, installation of venturi-shaped restrictors of differing contours, depending on engine size and whether the motor is turbocharged or naturally aspirated, govern the engine air inlets. The result: Engines have a longer life and lower stresses.
Meeting (and holding) the road. Callaway started out to design the C12 around what Reeves Callaway calls the "phenomenal technology" developed by Pirelli, the aggressive-handling 295/30 ZR19 tires--wide-tread (295-mm), low-sidewall (a width-to-height ratio of 30) "shoes" mounted on whopping 19-inch wheels. The lower the sidewall, the less tire flexing when cornering, resulting in tighter directional control--so much so that the C12 can pull 1.65 lateral gs with racing tires (1.2g, in mufti).
Taking advantage of this tire capability meant "putting the wheels on the floor to the maximum allowable track width distance," says Bill Prout, another ex-driver and Callaway director of marketing. "You build everything around tire location for maximum cornering ability." Thus Callaway planted these tires at the maximum 2m width allowed for the racing car, while most others in this class are slightly under because of the size of their street-legal counterparts. And Prout adds, "The longer the fore-and-aft wheelbase, the more stable the car in high-speed turns and the faster it can corner."
With the wheel positions set, the vehicle drivetrain and suspension geometry and kinematics had to be tailored to the track, while at the same time designed to fit the original Corvette attachment points and volume. Designers and fabricators working on both sides of the Atlantic pulled off the feat, taking only four months from start until the car's debut at last year's spring Geneva auto show. Key to quick turnaround from concept to parts was the CAD modeling and design done with Pro/ENGINEER software from Parametric Technology Corp. (PTC, Waltham, MA), (Design News 1/4/99, p. 55).
One example of vehicle dynamics redesign is the transverse composite-material single leaf springs used on the original Corvette. These light and corrosion-proof springs mount on top of and parallel to the axles. Callaway notes they produce a lower spring rate when used over the wider C12 axles, which extend farther from the spring ends, and are thus not as effective. The solution: Use the original springs but replace the dampers with shocks that are surrounded by a small coil spring to compensate for the longer axle moment arms on the original spring. But care had to be taken to account for any greater loads on the shock mounts due to the coil springs.
Designers used Pro/ENGINEER's surfacing software to develop both the styling and aerodynamics of the Callaway C12. |
The large-diameter wheels provide volume for brakes with a large swept rotor area. The road C12 has single-piston caliper brakes, while the racer has four-piston units on the front wheels, allowing more symmetric gripping of the rotor via pistons on both sides of the disk. The rear brakes are the same as on the stock car because the aero downloads add to road gripping. A large brake on the rear would only lock up under heavy braking when the inertial downforce shifts to the front wheels. If there is any question about the effectiveness of this arrangement, how does a deceleration of 1.21g sound?
Aero to go! The development team used PTC's Pro/SURFACE software to design the composite body panels and fabricate the molds to make them. These are all new, except for the Corvette's greenhouse area, which Callaway says would be difficult to change. He adds, "The body is contoured to handle the airflow and have a modicum of good taste." Key are the horizontal overhangs at the lower front and rear of the body, which define the shadow or planform area of the road car--and within which any features on the racing vehicle must fit.
"Starting out front, the shelf of the front overhang governs the airflow ahead of the wheels and sets it up through and around the vehicle," according to Callaway. This horizontal splitter creates a high-pressure area, killing lift at high speeds to hold the car to the road. The center of the oval mouth above the overhang is the minimum area necessary for radiator airflow. The sides of the oval feed ducts that furnish cooling air to the front brakes. The minimum amount of air captured for cooling translates as reduced drag.
The C12 incorporates integral headlights and covers, thus eliminating the trademark Corvette popup headlights. Callaway says the drag from the extended lights would amount to a reduction of 4.5 mph at racing speeds of 200 mph. At Le Mans, racing around the clock and in fog and rain, drivers run all the time with their lights on. With many classes of cars on the course, this is a courtesy extended to slower drivers to increase their awareness of cars overtaking them.
As the air moves along the sides of the car, Callaway notes it turns roughly 45 degrees down from horizontal. Here, the trick is to keep the air from going underneath, reducing road-holding downforce. He says, while some racers, such as CART (Championship Auto Race Teams), are allowed to contour venturi surfaces underneath to create road-holding low pressure, in GT cars the bottoms are a flat composite panel. "Keeping pressure low underneath impacts aerodynamics all the way to the front of the car." Callaway designers did this by incorporating horizontal rocker panel shelves along the bottom of the sides and contouring the body to block air from going underneath. A similar horizontal extension across the lower rear width of the car also helps but serves an even more important function. This shelf on the road car expands the shadow area, allowing mounting a wide, large-area wing on the upper rear for more downforce and thus higher speeds through curves.
In road racing, downforce, for greater road grip and control, is more important than drag from the wing. Callaway says that in racing trim, the car's coefficient of drag is around 0.42, while the road car is slicker at 0.30. He adds that racing rules and limits put designers in a box with little latitude as to what can be changed aerodynamically and otherwise.
Callaway is enthusiastic about tools now being made available for future projects. He cites the "DIGITAL PHYSICS, particle-based wind tunnel in a computer" software from Exa Corp. (Lexington, MA) as particularly promising. "Full-body aerodynamics that would take days on a Cray supercomputer can be done overnight on a SPARC workstation."
CART (rules) before the horse (power)
What's happened in CART (Championship Auto Racing Teams) since the cover story in last year's racing technology issue (Design News 5/4/98, p. 72)? As Team Rahal (Hilliard, OH) technical liaison Don Hayward notes, "CART has a stable rules package that puts a limit on technology." This keeps teams and racing competitive but there is not much new racing technology being introduced.
However, one major rule change has forced teams to focus on aerodynamic development. Hayward highlights the new requirement for smaller, non-flapped "super-speedway" rear wings as well as smaller forward wings for races on shorter oval tracks. Road course races will still use the more effective, larger two-element (flapped) rear wing, and bigger front wing, giving more downforce for a given speed. Such twisting courses have intrinsically lower speeds. These changes, aimed at increasing safety, reduce downforce, forcing drivers to go slower in turns. CART cars are capable of laterally pulling upwards of 5g in turns. By emphasizing driver skills, the change will make races more competitive.
Engineers are validating the smaller wing designs to wring out the most downforce. But design teams are also having to investigate car behavior under these changed aero loads in order to obtain the optimum suspension set up for best car handling.
According to Hayward, Fluent's (Lebanon, NH) Version 5 computational fluid dynamics (CFD) software is vital in such aero development. This package incorporates the UNS 2D and 3D fluid codes, as well as Gambit for producing a surface defining mesh. Slick file transfer from this into Parametric Technology Corp.'s (Waltham, MA) Pro/ENGINEER mechanical design code for part modeling and CNC production completes what Hayward sees as a seamless manufacturing operation. "We've been using Pro/E to the max in designing parts. It's just like a hand tool now, we're using it all the time. The software eliminates surprises early, as if drilling for oil but eliminating all the dry holes right away. We can look at many more ideas in a given time but still be faster in development."
Also helping Team Rahal's CFD work is its technical partnership with Ford. The automaker is using Fluent codes as well as NASA-developed software. Hayward adds, "This takes the load off Rahal engineers who are not just involved in development, but have to devote time to setting up the cars for races." And he concludes, the team also helps Ford in code validation work.
Once CFD work has narrowed down, say, candidate wing designs to a couple of contenders, scale and then full-size models can be fabricated for wind-tunnel or track testing. "Wind-tunnel time is expensive," says Hayward, "and you have to be judicious in what you use it for." For instance, tunnel testing can be useful in investigating overbody and rear-wing airflow, even without a moving ground plane to reproduce real-world road boundary-layer effects. Such tunnels are more costly to run and would be used only for directly applicable testing.
CART teams are also looking into aero effects of the engine exhaust, along the lines of what Hayward describes as opportunities for small gains within the rules. Similarly, engine developments are aimed at refining drivability--that is, making engines more linearly responsive and smoother running by optimizing their controller mapping for various conditions and driver input. Thus a driver is less likely to lose tire grip by spinning up or dragging the driving wheels, allowing him to competitively drive the course rather than the engine.
Horses for courses
Notice how Indy Racing League (IRL), CART, and Formula One (F1) cars all look alike? Well here are some of the under-the-skin differences.
PHILOSOPHY
F1--teams are required to build their own cars leading to a wide range of performance; deeper pockets may accomplish more; more people thus needed on a team.
CART and Indy--teams obtain cars from a handful of specialized builders, so everyone is more or less on the same playing field; these racers are produced with some economy of scale so teams can invest in refining rather than building cars.
WEIGHT
F1--1,100 lb
CART--1,550 lb
Indy--1,575 lb
ENGINES
F1--775-800 hp, naturally aspirated, 3**LITER** V10
CART--850-900 hp, turbocharged, 2.65**LITER** V8
Indy-700 hp, naturally aspirated, 4**LITER** V8
AERO
F1--flat bottom with rear diffuser and multiple, stacked wings
CART-aero tunnels underneath for downforce generation; wings must fit in proscribed "box"
Indy-wings, mounting angles, and locations are IRL specified
MATERIALS
F1--liberal use of composites allowed (carbon suspension components, gearbox covers, etc.) under rules umbrella, which leads to expensive, lighter cars; design innovations to get safety with light weight components
CART and Indy--composite chassis; steel suspension and more use of metals; rules dictate materials, and how and where they can be used
Learn the lingo
Here's some racing jargon to bring you up to speed:
Balaclava: Not a dessert but the protective, fire resistant hood or mask worn by drivers under their helmets.
Blowover: A drag racer pitching up and over from too much front lift--or rear wing drag.
Boost: Manifold intake pressure above ambient atmospheric pressure, which can be increased or decreased from the cockpit depending on competitive needs. Most mechanically-driven supercharged, and turbo boost somewhat, consume more fuel, so drivers use judgment and team feedback to govern its use.
Compound: A recipe which determines the different qualities and composition of a racing tire. Compounds are developed to maximize performance with each race track surface in mind. Wear, grip and temperature are important factors in determining the correct tire compound.
Drafting: The low-pressure wake of any fast-moving car which can often pull cars following behind. Drafting is not a significant factor in Indy-type car racing compared to full-bodied styles of racing because of the limited frontal area and small size of the cars.
Line: The quickest way around a race circuit, taking advantage of a racer's braking, cornering and acceleration techniques. A dark shading or "groove" often appears as the tire rubber is left in the line.
Oversteer (Loose): An often-heard driver complaint. A handling condition describing the tendency of a car's rear end to lean toward the outside of a turn. The condition can be remedied by a tire change or suspension adjustment.
Pop-off valve: A device maintained which limits manifold pressure.
Chicane: A quick right-left or left-right turn.
Hat dance: The ritual of photos taken after a race, with the top three drivers changing sponsor hats for each photo.
Take (or sneak) a peek: When a driver puts his car in a position to see if he has enough horsepower or is quick enough in a corner to pass a competitor.
Ground effects: The collection of devices which make the car hug the ground like a vacuum cleaner hugs a rug. Aerodynamics under the car create a low pressure area or partial vacuum between the race car and the race track.
Marbles: The 'dirty' part of the track so named because of the way little balls of worn rubber that gather there during a race.
Set up: Adjustments made by the crew to the various components of a car--spring tensions, shock absorber settings, stagger, gear ratios, wing angles, etc.--to try to gain optimum performance at a given track, including educated guesses as to the effects of weather and track conditions.
Shake: Frequency distortion of drag racer tires. If too high, energy can't be absorbed and "grip" is lost.
Stagger: The difference in circumference between right and left side tires. In oval events, it is preferable to have right side tires that are slightly taller to help the car turn.
Wicked up: Drag racer engine developing peak power.
Computational fluid dynamics (CFD), such as these streamline (left) and pressure (right) wing analyses from Fluent 5, is allowing more aerodynamic configurations to be initially evaluated. Thus, fewer candidate components need be fabricated for testing, and cutting design-to-track time. |
About the Author(s)
You May Also Like