Cordsets for Power Distribution
October 22, 2010
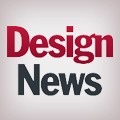
Cordsets have come along way. Because cordsets do not consist of continuous conductors, theNational Fire Protection Agency (NFPA) considered them "splices" and thereforeunusable for power distribution in many industrial applications. This rulingchanged in 2002 when NFPA 79 was revised to allow the use of molded-on cordsetsfeaturing quick-disconnect connectors and rugged cable for exposed-run installations.These connectors could now be used topower motors, pumps and othermachinery.
When "installed to closely follow the surface and structuralmembers of the machinery" (NFPA, 2006, 79-6), cordsets can now be used in placeof conduit and raceways - allowing engineers to design and install a systemmore efficiently than prior methods.
Before this revision to NFPA 79, hard wiring was the primaryoption for power distribution and all wires were required to be run throughprotective conduit to prevent wire damage. Junction and pull boxes werefrequently used for protection of the conductors and terminations, and usersneeded to install, support and run raceways from one part of the equipment tothe next to power multiple sections at once. In some cases, gutter boxes andother approved wire methods were also used.
Cordsets for Power Distribution_A |
These requirements resulted in excess equipment costs, while thelack of flexibility and the significant time required for installation led toexpensive downtime for many users. In addition, when large projects were commissioned at one site andinstalled at another, teams of electricians were often required to re-assemblethe equipment once it was moved to the site of installation. These issues werealso a factor when relocating or reusing equipment.
Multi-Environment Applications
To alleviate many of these concerns, molded-on cordsetswere introduced with a modular, quick-disconnect design for more efficientinstallation. In a cordset, all wires are bundled into a single cable clad witha jacket material designed to withstand diverse environmental conditions,including water, oil and temperature fluctuations. By eliminating the need forconduit and individual terminations for each wire, cordsets deliverplug-and-play connectivity.
Environmentally protected cable was developed to provide the samecrush and impact resistance as conduit to withstand the toughest industrialconditions. It can be used for distributing 15 to 40 amps of power from onemachine to another, including on conveyor lines and other large-scale systems.When used for loads such as motors or pumps, cordsets can lead to a decrease inthe equipment replacement time due to ease of installation. So long as theequipment load and other parameters do not change, molded-on cordsets do notrequire recommissioning, making relocating, rerouting or servicing of equipment- particularly in areas requiring certification - more convenient and,therefore, cost-effective. Additionally, cordsets do not require the high costof engineering and labor associated with the installation of conduit andraceways. As a result, labor can be reduced by up to 40 percent using molded-oncordsets, depending on the scope of the project.
Cordset Specifications
Once a type of cordsethas been selected to meet unique environment requirements (such as waterresistance or high temperatures), designers should consult tables providedwithin the NFPA 79 code to determine the appropriate ampacity of the cordset.Ampacity is dependent upon the number and size of the conductors. It isrecommended to use one conductor for a protective earth ground, and it shouldbe positioned as close as practical to the load conductors to minimizeimpedance in the protective earth circuit in case of a fault. Some cordsets aremanufactured to include a protective earth ground within the cord itself, whichensures that a protective ground is immediately adjacent, or as close aspractical to the power conductors.
Cordsets for Power Distribution_B1 |
Though the NFPA 79 code allows cordsets to be exposed on thesurface of the system, they must be protected from damage that could occur ifthe cordsets hang loose, droop or are obstructing doors or moving parts duringnormal everyday use. To prevent movement, as well as maintain support to theequipment, cables are to be supported and fastened "every 305 mm (12 inch) in anon-vertical run; every 914 mm (36 inch) in a vertical run; when suspended inair spanning a distance up to 457 mm (18 inch)" (2006, NFPA 79-36). Additionalprotection measures such as guard railings or walk/drive overprotective devicesmay be used to prevent damage. An alternative method is to install the cordsetin a wireway or deck cover. Sections of individual exposed lengths of cable areallowed in these applications up to 15m (50 ft).
Installation Design Considerations
While terminal blocks and enclosures are not required incordset installations, cordsets still must be supported at all terminations. This design reduces pressure caused by thecable pulling downward on the terminations and receptacles, thus increasingreliability and minimizing failures at these connections. Cable ties, supportsor clamps can be used to support both the cable and terminations. Cable tiesshould be snug, but not over-tightened, and cut flush to protect workers aswell as to prevent a possible snag point for other cables. Throughout thesystem design process, design engineers need to ensure that neither the cablenor the insulation in the selected cordset could be damaged during installationor during operation due to system design.
By adding service loops or extra length to the cables, designerscan make it easier for users to more easily connect or disconnect the cordsetto and from a load or device. For example, a loop may be used to connect asmall motor, so that it may be disconnected and removed without requiring thecable to be detached. Loops should be kept as small as possible to minimizespace consumption.
Quick-disconnect connectors are not intended for disconnectionunder a load. Therefore, no power should be delivered via any connectors withexposed male pins, as this would pose a shock hazard. The power should alwaysend on the female connector. To prevent damage or dirt from entering thedevices while unplugged, cover any externally mounted receptacles with closurecaps - protecting the cable until it is reconnected.
Jay Bartsias is product manager-connectivity at TURCK.
About the Author(s)
You May Also Like