Position transducer delivers improved accuracy
March 6, 1995
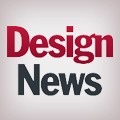
Lynnwood, WA-Linear Voltage Differential Transducers (LVDTs) play a major role in the position sensor market. A typical LVDT consists of an evenly wound primary coil and two evenly wound secondary coils. The amount of energy coupled from the primary to a secondary depends on the amount of the target or core located in the secondary coil.
These transducers produce a linear voltage output when the solenoid is near the middle of its range. But as the sensor's ferromagnetic core moves to either end of its stroke, the output voltage is no longer linear. In the nonlinear region, small variations are magnified, reducing the sensitivity and accuracy of the sensor.
As the target or core moves from the center to the ends of the secondary, the percentage error at full scale can grow. The result: Nonlinear end effects will occur because of the evenly wound coils. If the application calls for low error, the target can only operate in a short region about the center of the sensor's stroke. This limited range creates a small stroke/length ratio, so the sensor must be much longer than the operating stroke length. Basically, a uniformly wound transformer model sets a lower limit on the size and complexity of LVDTs used in a specific application.
Kevin Woolsey, a senior design engineer with ELDEC Corp., a subsidiary of Crane Corp., decided to use CAD to find a more efficient winding pattern. "What you need is an accurate linear output with a constant error over the entire stroke of the solenoid," Woolsey explains. His approach yields a computer-designed-and-calibrated position sensor
The sensor is symmetrical about an axis, so it can be modeled two-dimensionally, further simplifying the problem. An exotic winding pattern would create headaches at the manufacturing stage. To avoid such difficulties, Woolsey divided the coil into a number of small, flat coils that can be uniformly wound.
Other Applications |
|
Assume that some desired output function-such as the impedance, resistance, or inductance-must remain linear or nonlinear. Woolsey's optimization program adjusts the number of turns in each one of the coils until the desired output function-whether impedance, resistance, or inductance versus target position-is met. "With this method you attain the highest stroke/length ratio and lowest constant percentage error band throughout the entire stroke," says Woolsey. A computer calibration technique used in the manufacturing phase removes any error attributed to part machining, permeability, and conductivity tolerance.
In a conventional LVDT, there are six wires on the sensor, two for the primary and two wires each for the secondary coils. The number of wires becomes especially critical in aircraft, where their distribution can add weight, cost, and labor time.
In Woolsey's LVDT, if a differential electronic interface is desired, the transducer design contains three wires. For a single-ended design it contains two. Due to the novel wiring arrangement in Woolsey's LVDT, the sensor's impedance varies as the target moves through its stroke length.
"In the past an engineer would go through many design and test iterations to arrive at a final design," says Woolsey. "With this new optimization method, all analysis is done on the computer."
Additional details...Contact Kevin Woolsey, Senior Design Engineer, ELDEC Corp., Box 100, Lynnwood, WA, 98046-0100, or phone (206) 483-7568.
About the Author(s)
You May Also Like