Plastics Industry Is Hot for Conformal Cooling but Constrained by Additive Technologies
May 4, 2015
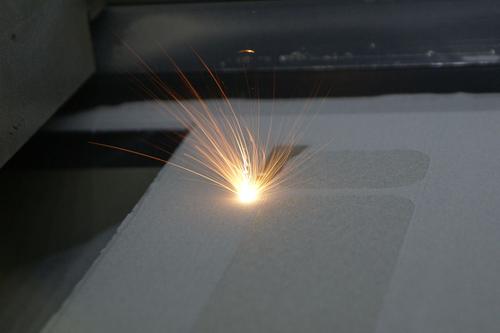
Manufacturers of plastic parts recognize the potential of conformal cooling to reduce molding cycle times. Problem is, conformal molds require additive manufacturing (AM), and technologies in that space are still evolving. Costs also can be high, and beyond that, many manufacturing organizations lack the knowledge and expertise needed to apply and incorporate additive technologies into their operations. This is particularly the case in emerging markets, where much of plastics manufacturing takes place.
"A lot of our customers are asking us about conformal cooling," said Tober Sun, manager for the technical research division at software provider Moldex3D, which makes a simulation solution for conformal injection mold designs. However, Sun, who is based in Taiwan, told Design News, "The big players in additive manufacturing have relatively few resellers over here, and there's not enough information about it, so people have a hard time finding solutions."
Business intelligence firm IBISWorld estimates that the global plastics manufacturing market is about $800 billion. Historically dominated by North America and Europe until 10 to 15 years ago, the market now belongs to China and the "North Asia" region, as defined by IBISWorld, with more than 25% of revenues.
US manufacturing has placed some of its hopes in its advantage in high-tech, with additive manufacturing an important driving area. While Asian moldmakers might be able to crank out CNC-machined injection molds at an economic advantage, the US could compete well in such higher-tech areas as conformal cooling, considering the country's greater expertise in the art of AM.
High-volume production injection molds require higher-strength metals like steel and titanium. That means conformal molds must be made with industrial-grade AM machines that use selective laser sintering (SLS) or similar processes that can heat and shape such metals.
MORE FROM DESIGN NEWS: How Additive Manufacturing Is Making Injection Molding Cooler
Rachel Gordon, technology analyst at research firm IDTechEx, says SLS machinery accounted for $217 million of additive manufacturing machine sales in 2014. "This is 18% of the market by value and 1% by number of machines," she told us.
Gordon describes injection tooling as "a large application for these machines," but adds that additive manufacturing "is expensive, and only becomes economically viable for very complex parts which are difficult or impossible to make in other ways."
Research from Wohlers Associates tends to bear out the comment by Sun of Moldex3D that Asia, so far, is lagging behind in AM expertise. Since the 1980s, the AM research firm says, 63.4% of industrial-grade systems have been sold in the US, and only about 5% to 6% of such systems are sold yearly in Asia.
Asia, then, understandably is at a "technological asymmetry" and disadvantage compared to Western competitors, both in availability of hardware and the expertise to put AM to work. Wohlers recently reported that the 3D printing and additive manufacturing industry grew at a compound annual growth rate (CAGR) of 35.2% to reach $4.1 billion in 2014.
Generally, an innovative technology will gain adoption at the margins of economics and performance. In other words, customers will try something new once it has become affordable enough and good enough to get the job done. While it might not be there just yet, additive manufacturing is increasingly reaching toward such tipping points in a number of applications, including injection molds, a critical path in the plastics manufacturing value chain.
Al Bredenberg is a writer, analyst, consultant, and communicator. He writes about technology, design, innovation, management, and sustainable business, and specializes in investigating and explaining complex topics. He holds a master's degree in organization and management from Antioch University New England. He has served as an editor for print and online content and currently serves as senior analyst at the Institute for Innovation in Large Organizations.
Design engineers, New England's premier design and manufacturing event, Design & Manufacturing New England, will take place in Boston, May 6-7, 2015. A Design News event, Design & Manufacturing New England is your chance to meet qualified suppliers, get hands-on with the latest technologies, be informed, and expand your network. Learn more here.
About the Author(s)
You May Also Like