Sign up for the Design News Daily newsletter.
PDM: Out-of-the-Box or Enterprise-Wide
DN Staff
February 1, 1999
7 Min Read
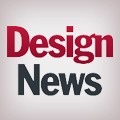
When selecting a software application to manage their design data, engineers have to choose from a dizzying array of products that run the gamut from out-of-the-box solutions to full-blown enterprise-wide solutions and everything in between. Out-of-the-box: "Our scalable approach works well" Robert R. Bauer, Senior Staff Engineer,The Ingersoll Milling Machine Co. The Ingersoll Milling Machine Co., located in Rockford, IL, is a world leader in the special machine tool and integrated manufacturing systems markets. Products range from high-speed automated transfer lines to giant, one-of-a-kind machines. Other special machines are for laying the latest graphite composite materials. We also have high-speed linear motor machines that remove material at high rates. Our policy is to supply innovative products and services that are of superior quality, delivered on-time, at a competitive price, and that fully satisfy all customer requirements. The Ingersoll Milling Machine Co. is known for technology leadership as indicated by five international awards for outstanding technology achievements. Starting in 1975, Ingersoll began building what developed into an extremely efficient CAD/CAM installation, centering around an IBM mainframe with over 500 CICS terminals and over 350 Cadam scopes. An extensive PC network infrastructure supports the migration from Cadam 2D to an associated solid modeling environment. Our solid modeling system of choice is SolidWorks. AutoCAD is an additional component in the data management scheme. Outside engineering houses provide designs in AutoCAD. Many of our customers also require us to deliver documentation of our products in AutoCAD, and we have 16 seats to support them. Windows environment a plus. SmarTeam is our product data management system of choice. SmarTeam was selected to manage our SolidWorks and AutoCAD files and to feed information into Ingersoll's award-winning, fully integrated Enterprise Resource Planning (ERP) system. SmarTeam was selected for its high level of integration to SolidWorks and supported our goal of moving from a mainframe to a Windows environment. Currently, SmarTeam has been configured for all three data streams: Cadam, SolidWorks, and AutoCAD. Our previous PDM system was "home grown" on the mainframe to support document control, plotting, and archiving for Cadam data. It was not capable of easily supporting an associative solid modeling environment. With SmarTeam's bottom-up, scalable approach to PDM, combined with its customization features, we were able to implement SmarTeam in a phased approach and did not have to "bet the company" on a full-blown PDM system swap out. Extensive functionality. The first phase, currently in production, allows for the introduction of SolidWorks data into the current ERP system. SmarTeam manages all SolidWorks files, including parts, assemblies, weldments, and drawings and then provides information about these files to the ERP system. It was approximately six months from the initial purchase of SmarTeam to approval of files via SmarTeam. We were able to establish basic functionality first, and we are now in the process of adding functionality and customizing the presentation of information to the users. SmarTeam's wizards and extensive API functionality make tailoring the system easy. A second phase that is also currently in production allows for the introduction of AutoCAD drawings into the current ERP system. SolidWorks and AutoCAD data is constantly synchronized between SmarTeam and the ERP systems. The tight integration capabilities allow us to maintain the flow of critical Engineering Notice of Change order information (ENOC) to the shop floor. Additional phases will entail more customization and the migration of more control from the mainframe to SmarTeam. Application notes PDM software user: The Ingersoll Milling Machine Co.
Company location: Rockford, IL
PDM package: SmarTeam from SmarTeam
Typical price (per user): $600 to $1,450
Operating platform: Windows NT
Installation date: 6/98
Number of seats installed: 50
Implementation time (to full deployment): Six months |
Types of data sources tied in and specific apps: MS Office, SolidWorks, Cadam, AutoCAD, CosmosWorks, Working Model
Major benefits reported: High level of integration to SolidWorks, tight integration capabilities, less risk than full-blown PDM package. For more information on PDM software from SmarTeam: Circle 545 Enterprise-wide: "Engineering and manufacturing are in sync" Harold Guptill, Documentation Control Supervisor,Gould Shawmut Gould Shawmut focuses on providing customers with a stream of new products that provide continually higher levels of circuit protection performance. We are a leading power fuse supplier in North America and have a growing presence in Europe and the Pacific Rim. As we pursue improved productivity, we seek more reliable and efficient circuit protection equipment to serve as our first line of defense against any costly downtime and product delays. In order to best maximize our production and optimize our performance, we selected Matrix Global Advantage (Matrix v6), MatrixOne's enterprise product development management (PDM) system, to streamline product development workflow. As our backbone solution, Matrix enables us to manage, control, and distribute critical engineering documentation throughout the entire enterprise easily and cost effectively. Truly enterprise-wide. With this software solution, our engineers don't waste valuable time searching for information, defining relationships among files, and answering questions from manufacturing and sales. As a result, people can move product down the development pipeline in a more timely fashion. Almost every department at Gould, from engineering and cost accounting to marketing, quality assurance, and manufacturing, uses Matrix. Gould Shawmut has 120 users of Matrix running on the Microsoft Windows and NT platforms, with plans to expand. Matrix integrates well with other applications we use, such as CAD and MRP systems. With Matrix, we can also accommodate conditional (if/then) branches among the various states of a process and develop custom functions using the Business Wizard to reduce such development processes as the report mechanism from 11 steps to only two. Users can filter data to produce custom views on the screen, keep multiple files open, and add descriptive data "tool tips" to objects in a business process. We have recently implemented bar code label printing using a Visual Basic integration. This information comes directly from the Matrix database and is printed using label software. Powerful, yet easy to use. Gould is running Matrix at all four of our electrical fuse plants. Matrix's flexible and easy-to-use modules are designed for systems and business administrators, as well as general users. We now use the software to efficiently automate many segments of our engineering change order process. Before implementing Matrix, the change would take several weeks to implement in all four of our production plants because of the amount of paper and copying involved. The implement segment of the cycle is accomplished in a matter of a few hours. At last measure our engineering change order cycle time went from 79 days to 39 days with the implementation of Matrix. Matrix Global Advantage helps Gould Shawmut ensure documentation accuracy, and, as a result, we can get a quality product out the door on time and within budget. Moreover, all of our engineering and manufacturing operations across North America are in sync. Application notes PDM software user: Gould Shawmut
Company location: Newburyport, MA
PDM package: Matrix Global Advantage from MatrixOne
Typical price (per user): $6,500/concurrent user
Operating platform: Windows NT
Installation date: 8/96
Number of seats installed: 120
Implementation time (to full deployment): Six months
Types of data sources tied in and specific apps: CAD (Cadra and SolidWorks); ERP (Infoflo); bar code printing (Visual basic and Loftware Label Manager); office documents (Microsoft Word and Excel)
Major benefits reported: Streamlined information and work flow, improved document accuracy, reduced ECO cycle time from 79 days to 39 days
About the Author(s)
You May Also Like