Try the 4-Parameter Thermal Model for Servomotors
March 2, 2010
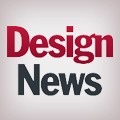
Dick Welch, a motor consultant, sent me four papers on thermal issues associated with servomotors or brushless-DC (BLDC) motors. We have posted these papers on the Design News site and you’ll find the links below. Welch also has written a 58-page Thermal Tutorial Book that deserves a look.
Early on, Welch and others taught engineers about a 2-parameter thermal model that treats a motor as the equivalent of a parallel R/C circuit, where R represents the thermal resistance between the motor and ambient conditions, and the C represents the thermal capacity of the motor. Motor data sheets usually provide these two values so engineers can model motor behavior.
Welch wrote: After taking my tutorial, a couple of students wrote to say there must be something wrong because they used this model and equations but their servomotors burned up, although the 2-parameter calculations indicated this shouldn’t happen! I asked them to verify they used the equivalent “total ambient condition” specified by the motor manufacturer and they assured me had… Furthermore, even though these servomotors had built-in temperature sensors/switches, the drive would not shut off power fast enough to keep the servomotor from overheating and even burning up.
He continued: I went into the lab, made extensive dynamic winding temperature measurements on servomotors from different manufactures and found when you apply more than the maximum continuous current to a servomotor, its winding heats up much faster than calculated by the 2-parameter model. I realized the motor’s winding must have its own dynamic operating temperature and thermal time constant that differ from the rest of the motor and this became the basis for my 4-parameter thermal model. The four-parameter model I teach now agrees with actual measured dynamic winding temperature.
In Welch’s tutorial book he discusses in detail how to obtain the correct 4-parameter model and how to extended it into a 6-, 8-, or higher-order model. “In the limit,” said Welch, “you are solving the Laplace heat flow equation in three dimensions which is what a finite-element analysis does using a “Mesh analysis.”
Here are the links to Welch’s papers:
2. Why a Servomotor’s Dynamic Motion Response Changes with Rising Operating Temperature.
3. If You Think a Temperature Sensor Will Always Protect a Servomotor from Overheating – Think Again.
4. Why a Servomotor Must Have a “Hot Spot” Temperature Safety Margin During Times of Peak Torque Output.
For information about Welch’s book and courses, contact him directly by email at: [email protected]. –Jon Titus
About the Author(s)
You May Also Like