Fan Motors Protected from Electrical Bearing Damage
November 18, 2009
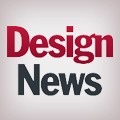
Because a single speck of dust could spoil a whole experiment at Purdue University's Birck Nanotechnology Center, the building's fast, forceful and flawless HVAC system includes carefully selected air-handling equipment plus the AEGIS(TM) SGR, a new sustainable motor shaft grounding device.
Research laboratories at the three-story facility in West Lafayette, IN have to be state-of-the-art. A dust particle could be 10 times larger than the group of atoms with which scientists there might be working. The building's HVAC system maintains the labs at 30-50 percent relative humidity and replaces the air at least 15 times per hour. Temperature is allowed to vary by no more than 1C; a rise of just one degree can cause a microscope or other high-precision device to expand enough to make measurements inconsistent. Some of the building's more tightly controlled "cleanrooms" are equipped with special dust-trapping filters and have as many as 120 air changes per hour, yet are not allowed temperature changes of more than 0.1C.
Key to maintaining such conditions are high-volume fans equipped with variable frequency drives (VFDs) that automatically change fan speed to adjust to the weather outdoors, laboratory occupancy levels and other factors. The contract to supply eight of these fans went to Colby Equipment Co., which in turn selected fans manufactured by Greenheck Fan Corp.
Colby's Tom Hall, a Purdue alumnus, knew that without grounding devices VFD-induced currents tend to discharge through a fan's motor bearings. Sparking pits the bearing race wall with fusion craters, which can cause noise and vibration until the bearings (and motor) fail altogether. VFDs can save energy, but if currents cause costly damage and downtime, these savings can be lost.
In his search for reliable grounding devices, Hall concluded that conventional metal grounding brushes would be difficult to attach to the already-installed fans. An Internet search turned up the easily installed AEGIS SGR Bearing Protection Ring(TM), manufactured by Electro Static Technology of Maine. Hall purchased eight of the rings, which are offered in standard sizes to fit virtually any NEMA motor from 1 to 1,500 hp regardless of rpm.
The SGR extends motor life by providing a safe path to ground for harmful shaft currents. Maintenance-free, it is unaffected by dirt, grease or other contaminants and provides the longest-lasting protection available. Unlike metal brushes, which wear out quickly, the SGR's microfibers work with virtually no friction or wear. Lasting for the life of the motor, the SGR is a "green" solution, providing sustainability for energy efficiency gains from using a VFD.
"Purdue has too much at stake for these fans to fail," Hall muses. "I would hate to have the glory of a scientific breakthrough go to some other school!"
About the Author(s)
You May Also Like