You Can't Just Say It's Reliable
January 19, 2011
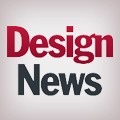
"A man's got to know hislimitations." This is one of the more memorable lines delivered by ClintEastwood in the movie "Magnum Force" and it possesses great wisdom. But howdoes this relate to engineering system reliability?
What do we mean when we say thata person is reliable? Is it possible to say that a person is reliable all thetime or just sometimes, in allcircumstances or in just some circumstances? The same questions need to be applied to an engineering system designbecause reliability cannot be an after-thought.
As we become more dependent oncomplex mechatronic systems, it is not sufficient to understand just how theywork; we must also understand how they fail. Fault-tolerant system design, notjust fault-tolerant component or subsystem design, has become paramount.Reliability is the probability that an item performs a required function understated conditions for a stated period of time. So an engineer needs to definethe functions a system must perform, the boundary conditions under which thesystem will operate and the time duration during which reliability is required.
To better understandreliability, I spoke with Tim Kerrigan, fluid power consulting engineer atMilwaukee School of Engineering's Fluid Power Institute, where he works toensure industrial and government systems are designed for reliability.
A physics-of-failure approachto reliability is consistent with the model-based approach of modernmechatronic system design. It uses modeling and analysis to design reliabilityinto a system, perform reliability assessments and focus reliability testswhere they will be most effective. The approach involves understanding andmodeling the potential failure mechanisms (e.g., fatigue, wear, temperature),the failure sites and the failure modes (the activation of the failure mechanisms).
The failure modes of amechatronic system include those of mechanical, electrical, computer andcontrol subsystems, i.e., hardware and software failures. A physics-of-failureapproach can improve reliability, reduce the time to field systems, reducetesting and costs, and increase customer satisfaction.
Asa euro 'mechatronica euro 'systemsa euro 'becomemore complex, the interactions among the subsystems - mechanical, electrical,computer and control - become more difficult to manage and the overall systemreliability is impacted by this integration. Therefore, an assessment ofoverall system reliability must have an adequate margin for safety. An usefulanalogy here is the feedback control system. It provides great benefits, butfeedback control systems can become unstable if there is an imbalance betweenstrength of corrective action (gain) and system dynamic lags (phase lags).Model uncertainty is quantified by assuming that either gain changes or phasechanges occur and the tolerances of gain or phase uncertainty are the stabilitymargins, gain margin and phase margin. Real systems must have adequatestability margins. Real systems must also have adequate reliability margins.
Mechatronics can enhance thereliability and fault-tolerance of a system with prognostics, diagnostics andbuilt-in test capabilities. The additional sensors and control elements must bevery reliable and do add additional cost. But the long-term cost ofunreliability is huge compared to the initial design cost of reliability. Inaddition, designing for reliability enhances energy efficiency andsustainability. Reliability and fault-tolerance is a competitive advantage inthe commercial market and an absolute requirement in the health care, militaryand transportation sectors.
About the Author(s)
You May Also Like