Modeling and Simulation for Motor Selection
June 4, 2011
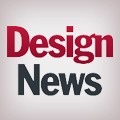
Multidisciplinary Engineering systems arecomplex and carry increased risk, development time and integration challenges.Model-based system design helps to manage the complexity and enhanceintegration while reducing the development time and risk. But just how doesmodel-based design improve the process of choosing a motor for a motionapplication?
First of all, consider thatsystem requirements dictate a desired end-point trajectory. ?The motion canbe defined as an electronic cam, characterized by different profiles andmaximum values of velocity, acceleration and jerk, which will affect the levelof mechanical stress, vibration and noise in the motor, transmission system andmechanical load. It is therefore essential that the desired motion profile bechosen first, because the required torque versus speed curve to size the motordepends on it. In addition, the motion profile has relevant implications on thetracking errors through the control system. ?A kinematic (geometry of motion) model of themechanical system is then developed and, through inverse kinematics, therequired motor motion profile is determined. The torque-speed requirements forthe motor are determined by first developing a kinetic (geometry plus alltorques and mass moments of inertia) model of the complete mechanical systemand then applying an appropriate feedback control system (e.g., PID) to thatmodel. ?Acomputer simulation (e.g., MatLab Simulink) of the mechanical and controlsystems will result in the necessary torque-speed curve of the load to size themotor.
Once this process is complete, candidate servo motors (e.g.,permanent-magnet synchronous motors) can be identified. Additionalrequirements, such as cost, energy efficiency and load-to-motor inertia ratio,will shorten the list. The chosen motor, including any flexible couplings orgearing, becomes an integral part of the system, and its properties must beincluded in the system model. The control system will have to be tuned or evenmodified because of the motor addition.
A computer simulation will reveal new torque-speed requirementsfor the system by presenting a number of issues to address. Is the motor'storque-speed capability satisfactory? Is the control system stable? Does thesystem meet application-specific requirements regarding time response, relativestability and steady-state error? If the answer to any of these questions isno, iteration is required.
With all of these factors addressed in detail, a model-baseddesign approach, together with computer simulation, can lead to optimal motorselection and all the benefits that implies to overall system performance.
About the Author(s)
You May Also Like