How Industrial Networks and IO-Link Are Shaping Pneumatics
Manufacturing expert Erick Rudaitis of Parker Hannifin Corp. discusses how industrial networks are delivering new levels of intelligence to the plant floor.
March 14, 2017
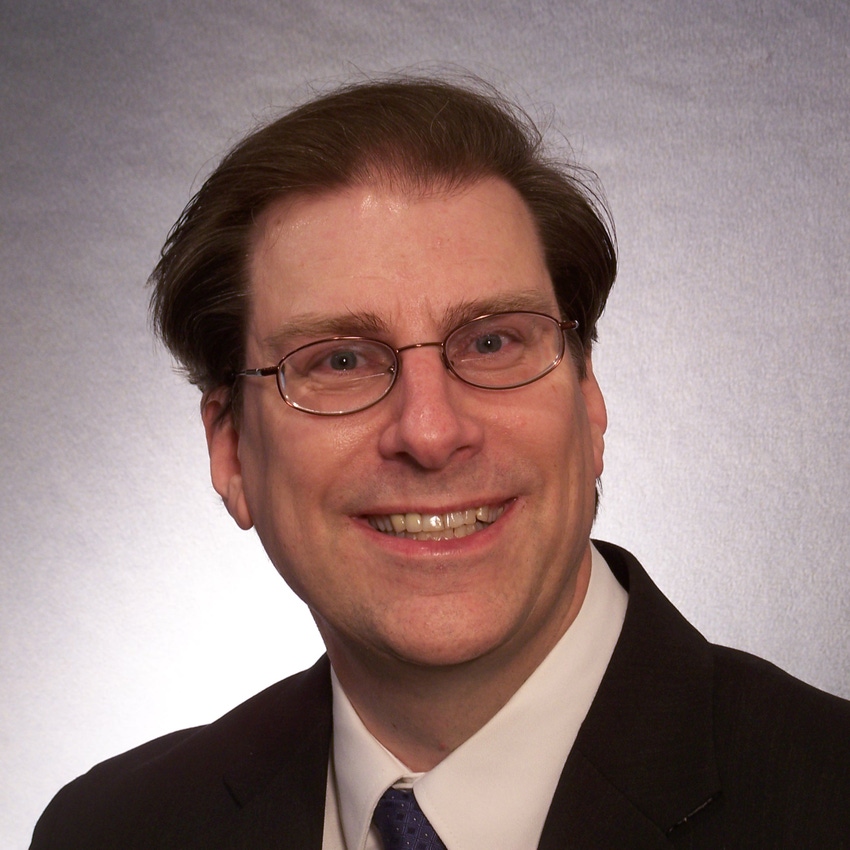
As enthusiasm for the Industrial Internet of Things grows, engineers are looking to industrial networks and communications protocols such as IO-Link to help unlock data from sensors on the plant floor. By doing so, they hope to apply diagnostic data and proactively identify potential problems before they have a chance to occur. Here, Design News talks to manufacturing veteran Erick Rudaitis of Parker Hannifin Corp. about what industrial networks and IO-Link will mean to myriad pneumatic components used on the factory floor. Rudaitis, who has served in advanced manufacturing for General Motors and numerous other companies, is a senior market development engineer working with an international team to develop network interface products for smart factories.
DN: Let’s start with a definition: How do you define industrial networks?
Rudaitis: Industrial networks are protocols that use Ethernet in an industrial environment to provide machine control. For example: EtherNet/IP; Profinet; EtherCat; Modbus TCP; CC-Link IE. Many of these protocols have been available for over 15 years. But their cost limits them to higher operations.
Fieldbus networks such as DeviceNet, Profibus and CC-Link were used for lower operations to save cost, but they sacrificed some functionality.
Parker Hannifin engineer Erick Rudaitis: “Customers have an interpretation of Industry 4.0, and the common theme is of added intelligence embedded in components. They want to get more intelligence onto the plant floor, versus holding it in a PLC.” (Source: Parker Hannifin Corp.) |
DN: When we talk about industrial networks for pneumatics, what kind of applications are we talking about?
Rudaitis: Networks are mainly used in processing. They’re used heavily in automotive for end-of-arm tooling, holding fixtures, weld fixtures, turntable assemblies. Anything that’s going to hold a part or move a part is going to use pneumatics and be controlled by a pneumatic manifold.
DN: What is IO-Link and how does it fit in these applications?
Rudaitis: IO-Link is a dynamic new open protocol standard that’s gaining greater use in point-to-point serial communications. It was started in 2008 by Siemens and has really been taking off in the last five years. It’s targeted at Industry 4.0 intelligence and it’s especially good for communicating with actuators and sensors.
PLC and sensor manufacturers have united in an international consortium to advance IO-Link communication. It’s got a lot of backing from companies like Allen-Bradley and Siemens. A lot of the big players are part of this consortium. They see the move from the smaller networks to this as driving the IIoT (Industrial Internet of Things), or the smart factory.
So there’s a good push behind it. As of last April, 124 companies had joined and there were 3.5 million nodes in the field. So in a short time, IO-Link has really caught on.
|
DN: Why is it such a trend now?
Rudaitis: The new buzzword is the smart factory. Customers have an interpretation of Industry 4.0, and the common theme is of added intelligence embedded in components. They want to get more intelligence onto the plant floor, versus holding it in a PLC.
There are a lot of things you can do with this. It’s possible now to load configuration data into the sensors and actuators, and receive diagnostic data. That’s a feature you couldn’t do on standard DeviceNet of Profibus. So because of the features you get from IO-Link, you’ll get better control and diagnostics than you could get from a fieldbus.
DN: So how does this shape the future of pneumatic motion control?
Rudaitis: We still have a lot of customers who hard-wire their valve manifolds. They go from an I/O card, through all the connections, to the manifold.
But now they can move to a network style. We see this as a huge shift. Now, they’re beginning to see how much added time it took to wire the manifolds, and how hard it was to troubleshoot them. So they are seeing a lot of benefits.
Also, they now have the power to put diagnostics in their valve manifolds. They can now tell you if a coil is shorted, or if it’s running hot, or if the voltages are sagging. There’s a lot of information that they could never get before, but they can get now, because they have more intelligence in the valve manifold.
DN: What does this enable the manufacturers to do that they couldn’t do before?
Rudaitis: It’s about getting the right diagnostics to help them pinpoint their problems more quickly. In an air manifold that can sometimes be difficult, and smart devices can really help.
It also allows them to change parameters over the network. For example, on a photo-eye, you may be sensing a distance for a particular product, and then you want to run a different product down the same line. In the past, you had to change the sensor. But now, on the fly, you can send a command down to change the parameter setup in that photo-eye, and you can run your other product down that same line. So it fits into flexible manufacturing – using intelligent sensors that can be configured on the fly. That’s very, very powerful.
DN: What are the implications for the Industrial Internet of Things?
Rudaitis: With smart devices, you get a lot more data. In most IO-Link plant floor network architectures, the data is going to flow from the smart device, through the IO-Link master, to the PLC.
So one of the big questions manufacturers have to address is, how do they get that proactive diagnostic data to the maintenance manager to schedule a repair during off-hours to prevent downtime?
That’s the big thing: What do they do with all that data? Do they put it on the cloud? Do they put it on an internal server? Now they have a lot of data that changes the company from a reactive mode to a proactive mode. It’s just a matter of how to get it to the right person.
DN: Does it make the engineer’s life better?
Rudaitis: Yes, it does, by far. It’s better because of the simplicity of the architecture and the cabling. It’s far easier than a hard-wired design. The challenge is what to do with the diagnostics. Smart devices can give you the data, but it’s up to you to decide what you want to do with it.
Senior technical editor Chuck Murray has been writing about technology for 33 years. He joined Design News in 1987, and has covered electronics, automation, fluid power, and autos.
About the Author(s)
You May Also Like