Five-axis gantry does it all
March 6, 1995
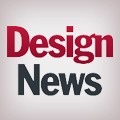
Dayton, OH--By combining compact, rigid construction with an innovative drive, a new five-axis gantry offers fast, accurate digitizing and machining. The huge system plows new ground for automakers, shipbuilders, and airframe manufacturers with its unprecedented combination of size and speed.
The gantry enables manufacturers to digitize large parts at speeds as high as 400 inches per minute, feed the design information to CAD/CAM systems, and then mill the parts in the same location. Combining speed, size, and rigidity, it eliminates the need for painstaking hand polishing and grinding of parts.
Prior to the development of the new system, manufacturers hand-polished large molds and dies. The reason: Their machining centers typically lacked the necessary size, speed, or flexibility to do the job.
Reportedly, the DMT1200 Series Gantry Center changes all that. Engineers at Dayton Machine Tool Co. managed to combined the seemingly incompatible qualities of size and speed. The gantry moves at unusually high speeds, despite a work envelope that measures an impressive 20- by 11- by 5-feet.
To achieve their objectives, they incorporated innovative designs in the gantry's drive system and spindles. One of the keys is a dual-pinion gearbox that uses timing-belt technology. Working in conjunction with the rack end of a rack-and-pinion system, the dual pinions provide linear movement of the gantry in both directions along the x-axis. Adjustable preloads on the gearbox's pinions take the "spring," or non-compliance, out of the system, enabling it to accelerate rapidly without losing its position.
Most critical to the drive's design, however, is the use of the timing belt. By employing a timing belt, rather than special gearing, Dayton Machine Tool engineer G. Dan Siler dramatically reduced the inertia of the system.
Dual-pinion gearboxes, available for half a century, typically use special gearing. But the special gearing adds to the inertia around the motor area, which is normally the greatest contributor of inertia to a gantry-type system. Siler estimates that the timing belt system reduces that inertia by as much as 60%. Timing-belt technology also cut the cost of the gearbox by close to $40,000, he says.
As a result, the DMT1200 gantry can accelerate far more rapidly than other large systems. The dual-pinion gearbox drives the gantry at feed rates of 1,200 inches per minute, and acceleration rates of 50 inches/second/second using ac servomotors.
The dual-pinion gearbox also provides a viable alternative to ball screw technology. Because of the long x-axis travel, Siler feared that ball screws would suffer from "stretch," and therefore compromise precision. Using the dual-pinion gearbox, rather than a ball screw, solved that problem. "We need to accurately accelerate this large machine over a broad envelope," Siler says. "The dual-pinion gearbox lends itself well to that application." A new patented feature of the gearbox also balances its output in both directions, thus making it possible to run at high speeds.
To carry out the machine's all-encompassing theme, Siler also designed a special spindle. The spindle is critical to the machine's performance for two reasons. First, its compact size adds rigidity, which, in turn, enables high-speed gantry movement and machining. Second, its broad performance envelope enables users to machine all kinds of materials without changing the cutting head.
Siler travelled the world to find an electric motor that would endow the spindle with high-speed machining capabilities and enough torque for conventional machining. Eventually, he settled on a custom-designed ac motor and vector drive that generates 50 hp, operates at speeds as high as 12,000 rpm, and achieves torques of 95 Nm at 0 to 5,000 rpm.
That combination permits use of the spindle for high speed machining of hard steels. Because machine tool customers typically operate tools at 12,000 to 35,000 rpm during high-speed machining of hard materials, the new spindle can be used for those applications. At the same time, its higher torque at lower speeds endows it with the ability to cut everything from wood to aluminum.
The real key to the design of the new spindle, however, is its compactness. During his preliminary design work, Siler concluded that a spindle more than 21 inches long would lack the necessary rigidity, and could therefore compromise the goals of the machine. "For stiffness' sake, the head must be as short as possible," Siler explains. Unfortunately, no spindle manufacturers could offer off-the-shelf units that would provide the necessary performance in a package less than 30 inches long.
As a result, Siler decided to design his own spindle. In the process, he packed the motor, spindle bearings, nose, release cylinder, and tool gripper into a 21-inch-long package. To do so, he developed a special drawbar. The tapered drawbar doubles the pull-in force of the tool gripper without requiring longer or larger springs. Siler achieved 2,100 pounds of pull-in force using springs designed for 1,100 pounds. In the process, he cut about five inches from the spindle's overall length. He eliminated the remainder by replacing the release cylinder, which typically measures between four and seven inches in length, with an air cylinder only 1.25 inches long.
With its broad performance range, the shorter spindle enables the DMT1200 to perform a wide variety of machining operations. "We were hoping to make a spindle that would handle everything from wood patterns to hardened dies for the automotive industry," Siler says.
|
|
Because of the DMT1200's design, large manufacturers can now dramatically reduce cycle times. The spindle's broad operating characteristics eliminate the need to constantly change the head. The innovative drive and light weight of the gantry crossrail enable it to operate at speeds exceeding those of large systems. And the rigidity, speed, and flexibility of the five-axis system permit it to operate at higher spindle speeds, while reaching features that large machines typically can't. Says Siler: "The large-envelope approach, combined with the ability to machine a wide variety of products and materials, set it apart as a product."
Additional details...Contact G. Dan Siler, Dayton Machine Tool Co., 1314 Webster St., Dayton, OH 45404, (513) 224-8528.
About the Author(s)
You May Also Like