Welding methods target tricky aluminums
October 2, 2008
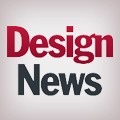
Columbus, OH -Fusion welding doesn't always live up to its name. With tough-to-weld aluminum alloys like 7075 or those in the 6000 Series, fusion welding can result in joints that don't really come together-at least, not without cracks, porosity, distortion, and poor fatigue resistance. Engineers from the Edison Welding Institute (EWI) have worked out two alternative processes for joining these difficult aluminum alloys without the problems.
The two methods-conductive heat seam welding from EWI and friction stir welding from England's Welding Institute-produce joints whose strength matches that of the parent material in its original-tempered condition, according to EWI Chief Engineer Jerry Gould. Both processes eschew any filler, producing seams whose composition matches the material around the joint line. Both can also create butt or lap joints. And finally, both welding methods show promise with magnesium too, Gould reports.
Here's a closer look at these emerging welding techniques, one best for thick sheets and the other best for thin ones:
Hot seams. A variant of resistance welding, conductive heat seam welding (CHSEW) uses an electrical current to heat the material in the seam. Yet unlike conventional resistance welding, this new welding process does so indirectly. Rather than directing the current into the aluminum itself, EWI instead passes the current into steel plates that surround the aluminum like a sandwich. The steel conducts heat into the aluminum, creating an hourglass-shaped "fusion zone" where the sheets meet. According to Gould, the conductively welded seams solidify from the inside out, under pressures of about 150 MPa. "The resulting joints are nearly defect free," says Gould, explaining that the direction of solidification and the high compressive loads prevent porosity and eliminate the tensile stresses that cause cracking.
Aside from producing high-quality joints, the process also works quickly. Gould cites speeds up to 3 m/minute. And it works with standard resistance welding equipment. CHSEW does require a supply of steel plates, but at 10-20 cents/lb for low-grade steel, the cost shouldn't hold the process back-especially given its speed and the $2/lb cost of aluminum welding materials.
The process' only real limitations relate to sheet thickness. It works best with sections from 0.25 to 3 mm. "Above 3 mm, the process is limited by how fast the heat sinks in," Gould says.
Conductive heat seam welding adapts traditional resistance welding equipment to "unweldable" aluminum alloys like 7075. Solidification takes place from the "fusion zone" center outward (regions 1, 2, and 3 in succession), lessening the tendency to produce pores and cracks. |
Stirred not shaken.
Friction stir welding forms joints by means of a rotating tool with a pin that plunges into the joint and a flat shoulder that spins on the surface of the sheets. This shoulder generates the bulk of the frictional heat, which then soaks down into the joint through the pin. During the welding process, the pin moves forward through the joint, creating a plasticized region that consolidates in the pin's wake. As a solid-state welding method, the friction-stir process heats the material to about 100C below its melting temperature. "The process brings the material to forging temperature rather than a melting temperature," Gould notes.
The resulting joints don't necessarily outperform fusion-welded joints strength-wise, but in EWI's tests they have exhibited twice the fatigue resistance, Gould reports, adding that the low processing temperatures eliminates distortion.
The process works best with sheets 1.5 to 100 mm thick. On thinner materials, the precision of the pin placement limits the capability of the process, Gould says. In addition to joining aluminum and magnesium, friction stir welding has been successfully applied to titanium, copper, and steel, Gould notes.
The process has found its first use in marine applications. It has, for example, joined the aluminum decking for European car ferries. Gould predicts that new aerospace and automotive applications will soon surface here in North America.
For more information about aluminum joining from EWI: Enter 538
About the Author(s)
You May Also Like