Metal Zapper
May 17, 2004
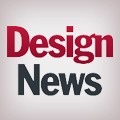
Most people have been warned about the dangers of putting metal in microwave ovens. Devendra and Satyendra Kumar didn't listen, and it's a good thing they didn't. These two brothers, both research and development managers for Dana Corporation, have invented a system that heat treats metals in microwave ovens no more powerful than those used to pop corn and heat up leftovers. "We've basically been able to get microwave energy from low power sources to do some things that haven't been done before," says Devendra Kumar.
That list of things includes such important metal treatments as brazing, hardening, carburizing, and sintering of powdered metal. When performed on a commercial scale, these processes normally take place in big furnaces that are costly to run and tough to control. Dana's Microwave Atmospheric Pressure technology promises to replace some of these furnaces with cheaper, faster microwaves ovens that inherently offer better thermal control. And the technology does more than heat-treat. Working at atmospheric pressures, the same system can deposit a variety of hard coatings normally applied under vacuum in chemical vapor deposition processes.
How It Works
Sure, metals and microwave ovens don't usually mix. But Dana's microwave technology avoids all the usual consequences of nuked metals, such as electrical arcing and magnetron destruction, by heating metals indirectly. This developmental system encloses the metal component within a ceramic insulating cavity containing microwave-absorbing plasma created from one or more inert gases. As microwaves pass through the cavity walls, they heat the plasma, which in turn heats the metal component.
And heats it quickly. Plasma temperatures can climb to more than 1,300C in a matter of seconds, reports Satyendra Kumar. This fast heating largely boils down to the plasma's efficiency as a heating medium. "It absorbs 95 percent of the microwave energy," he says, adding that it also has very low thermal mass. And because the plasma completely envelops the components, it promotes uniform heating, avoiding the hot spots that can occur in furnaces.
When used for coatings, the technology works similarly, except that microwave energy targets the plasma surrounding the part rather than the part itself. And the kind of gases used to create the plasma would also differ. In straightforward heat-treating applications, Dana creates the plasma from an inert gas such as argon. Coating jobs, by contrast, would typically start with a mixture of gases that contain the coating reactants. As with chemical vapor deposition, these reactants disassociate from the plasma when zapped with the microwave energy and reconstitute on the substrate surface, explains Devendra Kumar. "We can add a variety of things to the plasma and deposit them on the surface of the part," he sums up. This coatings line-up is still developing but currently includes silicon nitride, aluminum oxide, titanium nitride, and tungsten carbide. On-going research suggests that the system can also perform other types of surface modifications such as de-crystallization to impart anti-corrosion benefits.
The Kumars report that microwave technology can apply coatings to parts with geometries that spell trouble for chemical vapor deposition processes-including concave surfaces and the inside diameters of tubes. The technology has also been able to combine coatings with formerly separate process steps. For example, it can consolidate sintering, carburizing, and coating. "Three processes in situ," is how Satyendra Kumar describes it.
Distinguishing Features
Microwave atmospheric pressure technology, for which Dana has so far applied for 23 patents, has a couple of key elements that distinguish it from existing industrial microwave and coating technologies. One involves the plasma itself. As its name suggests, this system sustains the plasma at atmospheric pressures rather than the vacuum pressures required by most chemical vapor deposition processes. "Gases are much easier to ionize at the lower pressures," Satyendra notes. He won't divulge exactly how the system keeps the plasma going without lowering pressures other than to say it involves a "simple, inexpensive trick."
The technology's other distinguishing feature has to do with its microwave energy source. Rather than using powerful high-power magnetrons, the Kumars instead chose to work with inexpensive, low-power magnetrons like those found in consumer appliances. These mass-produced magnetrons would typically have output power between 1.3 to 2.3 kW, though many applications require just a half a kilowatt or so. The magnetrons in industrial microwaves, by contrast, can put out tens or even hundreds of kilowatts. Likewise, the frequencies used by magnetrons, usually around 2,450 MHz, also approximate those of a home oven and differ substantially from the 13.56-MHz energy sources typically used in comparable chemical vapor deposition processes. Satyendra Kumar acknowledges that this high frequency contributes to the ability to sustain the plasma at atmospheric pressures. "Our trick wouldn't be as effective at lower frequencies," he says.
To make up for the relatively low power of its individual magnetrons, Dana's technology includes provisions for ganging them together. A commercial scale system would likely consist of several magnetrons. Multiple microwave sources will ultimately help Dana build sealed-up systems that handle larger parts or increase throughput by heating several insulating cavities at once. The Kumars report that they have already used their two prototype systems to treat large parts weighing as much as several hundred grams and having a variety of shapes-including a 2-ft long, 3-inch diameter tube. They've also managed to anneal a 3-ft long piece of structural aluminum. "So far we think we can apply the technology to virtually any shape," Satyendra Kumar says.
Cost and Quality
With its reliance on low-cost microwave sources and its lightening-fast heating, the technology promises to impart some significant cost reductions to heat-treating operations. David Brosky, Dana's business development manager for microwave technology, estimates that commercial microwave systems will cost about 30 percent less to operate than conventional heat treating furnaces. He should know. "Dana is one of the biggest heat treaters in the world," he notes.
Part of that cost savings comes from a cycle time advantage (see sidebar). Brosky also expects commercial-sized microwave systems to cost less to build than large furnaces do. And they may cost less to run too. Brosky predicts the efficiency of the microwave systems will translate into roughly a one-third reduction in energy costs.
|
Microwave systems also seem likely to offer a quality edge too because of their fast consistent heating. Although the system can hit highs over 2,000C and perform high-temperature operations, its low-power nature also allows it to work at much lower temperatures. For example, many hard coatings go on at 200C or less, according to Devendra Kumar. Lower, consistent temperatures eliminate the thermal stresses that can "distort parts and change microstructures" in traditional heat-treating processes, he says.
Also helping out on the quality score is the inherently tight control of the system. Microwave all but eliminates the overshoot and guesswork that can plague industrial heating applications. Why? When the magnetron switches off, heating simply stops because the plasma has little thermal mass. "The possibility of overshoot is almost non-existent," Devendra Kumar says.
For all the potential of the microwave technology, prospective users may have to wait a bit to get their hands on one. Right now, Dana has just the two prototype systems and by year's end will launch a pilot-sized line in its own plant. It will initially use the system for its internal needs, but Brosky says the company also plans to license the technology. Dana is currently seeking development partners to build equipment and work on various coatings. Brosky predicts that some of these commercial systems could be available as early as next year.
Senior Editor Joseph Ogando can be reached at[email protected].
About the Author(s)
You May Also Like