Automakers to look to solid state welding of dissimilar metals
August 5, 2004
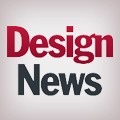
Gould: "Friction welding and magnetic pulse welding...are really coming on right now." |
As chief engineer for all resistance and forge welding activities at the Edison Welding Institute, Jerry Gould has focused on resistance spot welding and coated-sheet steels. He has published more than 75 technical papers on various aspects of resistance welding and welding metallurgy, and was the recipient of the American Welding Society James A. Lincoln gold medal award in 1995. Gould holds a Ph.D. in metallurgical engineering and material science from Carnegie-Mellon University.
In the past decade, Gould says, increased pressure on automakers to boost performance and fuel efficiency has led to renewed interest in new welding techniques, especially for such dissimilar metals as steel, aluminum, magnesium, and titanium. Design News asked Gould how the auto industry plans to deal with those materials science challenges.
Design News: Why does the auto industry need to be concerned with joining of dissimilar metals?
Gould: The auto industry is trying to figure out how to reduce vehicle weight. But while they're trying to cut weight out of their structures, they need to maintain high durability. So they need materials like aluminum to reduce weight and they need steel for high durability.
The problem is that it's very difficult to fusion weld aluminum to steel because one melts at a higher temperature than the other. Sometimes when you have materials with different melting points, they can form bad phases, called inter-metallic phases, which are detrimental.
So if you want to join dissimilar metals, such as aluminum and steel, you've got to look beyond fusion welding. Right now, the best alternatives are solid state processes and cold processes. The idea is to bring the dissimilar metals together and suppress the bad side effects.
Design News: Which dissimilar metals does the auto industry need to be looking at?
Gould: The most important ones right now are aluminum-to-steel, steel-to-magnesium, and aluminum-to-magnesium. All of those are material combinations that the auto industry wants to put into vehicles, with the idea of getting the best combination of weight reduction and performance.
In Europe's Smart Car, for example, magnesium cross members have been used on an aluminum sub-frame. Automakers also like to use dissimilar metals on sub-assemblies that they can hang on the vehicle frame. Shock mounts, for example, are sometimes
made from magnesium, and then attached to aluminum or steel frame rails.
The biggest use of dissimilar metals, though, is in steel sub-structures with aluminum skin panels on top. The idea is that steel provides rigidity and crashworthiness and aluminum provides corrosion resistance and light weight.
Design News: Some of the materials you mentioned are beginning to be used now. How are automakers joining them today?
Gould: What's really hot in the industry right now is the use of mechanical fasteners. We use self-piercing rivets, where we plunge a third body through the parts and create a mechanical joint that way. We also use what's called a "clinch," where we push a die in one side of the metal and form the other metal around it. That way, it makes an interference-type fit. We also combine these methods with adhesives. We actually glue the metals together as a way of making a joint without having a metallurgical reaction. All of these techniques are being investigated very heavily by automakers today.
Design News: So how do you plan to take this to the next level and begin welding these materials?
Gould: You need processes that allow you to break up the surfaces and bring the metals into intimate contact, without melting them. Those are more advantageous than the processes where you actually melt the material.
The way to do that is through solid state approaches. Right now, prop shafts are starting to go into vehicles here and in Europe, where steel end pieces are friction welded onto aluminum shafts. The other technology that's gaining a lot of attention is magnetic pulse welding. Magnetic pulse welding uses a magnetic field to accelerate one part, which we call the "flyer," into a static target part. With this technology, you're talking about impacting those parts at speeds of 1,000 feet per second.
Design News: How does that help solve the problems associated with conventional fusion welding of dissimilar metals?
Gould: At those kinds of speeds, you dissipate kinetic energy into thermal energy, so you get a very finely defined melt zone. Also, the thermal cycles are measured in double-digit microseconds. And as the thermal cycles get shorter and shorter, you can suppress a lot of the detrimental phases that you get with other material joining systems.
Design News: With the auto industry's emphasis on cost consciousness, can they actually use any of these processes? Can these be considered growth areas?
Gould: Friction welding, magnetic pulse welding and some of the other methods for joining dissimilar metals tend to be relatively inexpensive. They can be used for high volume manufacturing, so they're well suited for the auto industry. That's why friction welding and magnetic pulse welding are really coming on right now.
About the Author(s)
You May Also Like