Laser system detects and treats cancer
June 5, 2000
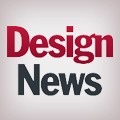
Fort Lauderdale, FL -Physicians and women patients alike will appreciate the Computer Tomography Laser Mammography (CTLM(TM)) breast-imaging system from Imaging Diagnostics Systems Inc. (IDSI). The reason: Not only does the instrument perform comfortable, non-invasive detection, but it potentially will be able to treat cancer as well, saving time.
To obtain a 3D image of the breast and its internal structures, a patient lies face down on the scanning bed. Her breast hangs free into a well in the bed called the scanning chamber. An infrared laser, emitted on a horizontal plane, rotates 360 degrees . The computer acquires data at one horizontal level "slice," then lowers the detectors and laser, typically 4 mm, to image another section.
A specially designed double-row detector array images both the absorption and florescence of breast tissue. The optical mammography system maps local changes in the optical scattering and absorption coefficients over the cross sections. When the absorption and fluorescence images are overlaid, a diagnostician can determine the exact location of any problem. "To the best of our knowledge, this is the first time this type of imaging has been done anywhere in the world," says Richard Grable, IDSI CEO.
Treatment too. Because the scanner images fluorescence, a surgeon potentially can use a biochemical florescence tag to locate the tumor and then turn around and use the same device to treat the disease through photodynamic therapy. In photodynamic therapy, specially developed photoresponsive drugs administered to the patient preferentially locate within cancerous tissue. When the compounds are illuminated by light at the activating wavelength, they release singlet oxygen that immediately kills the adjacent cells.
Redesign in 10 days. After five years in development, the instrument debuted in July 1999. But after its first clinical test, "We quickly saw that the real world environment of the hospital was quite hostile compared to our lab," says Grable. Not only did the quickly varying temperature in a hospital room create instabilities in the laser system, but also the size of the instrument was unwieldy.
So IDSI engineers went from a four-laser system down to one and reduced the size of the instrument by 45% in only 10 working days. This quick turn-around time was the result of fortuitous engineering from the start, says Grable. The scanner was designed so that one could change the detector or electronics without having a huge impact on the mechanical parts.
Realizing they may have had the answer in an older design, engineers "went back to the bone yard and pulled parts from a system that we developed a couple of years ago," says Robert Wake, IDSI director of engineering. "Manufacturing resurrected the instrument and engineering designed a way to incorporate the new laser diode."
The mechanical framework, the rotation and lift mechanism, and the fiberglass skins haven't changed for three years, says Wake, "yet we've made several different scanners. We're pleased with how much mileage we've gotten out of the original design."
Two diode-pumped solid-state lasers, one Ti-sapphire laser, and one regenerative amplifier were replaced with one diode laser and a proprietary controller for temperature and power.
Also, the 85 200-micron glass-fiber optic cables originally used to transmit captured light to the detector electronics were eliminated through a new detection layout. The first instrument performed at only 60% efficiency. "We were throwing away 40% of our light," says Grable. "This is fine if you are working with a powerful output, but we were losing part of the signal we were trying to detect." Engineers solved the problem by positioning the large area photo diodes closer to the breast, reducing the need for so many fiber-optic cables.
Between the move to one laser and the new detection design, engineers were able to eliminate many of the special optical amplifiers, says Grable. "All we have now is a single console with the computer, a 21-inch monitor, keyboard, and the scanning bed where the patient lies down."
Along with the decreased size and decreased cost of lasers came increased reliability. "Reliability is a big thing in hospitals. Down time doesn't help patients. The way the lasers were before, we didn't have the uptime we needed to get the throughput," Grable adds.
A classy finish. The scanner's high-gloss "automotive finish" is also unique for an instrument this size, says Grable. "A crackle finish hides a lot of sins. But we didn't want to go that route." So IDSI hired a design company to create an attractive physical appearance. But maintaining this high-quality finish while developing a precise mold became a challenge.
IDSI engineers originally drew the design in AutoCAD from Autodesk (San Rafael, CA). They later migrated the data to SolidWorks (Concord, MA). "We used stereo lithography to make tenth-scale models," says Wake. To create the fiberglass molds, engineers made a male part by cutting laminated cardboard sheets directly from CAD files, from which they made the female molds.
All the parts were designed on the computer, says Wake. Not one physical drawing was involved. "There is no other easy way to do this because all the compound curves would be difficult to draw and dimension," says Wake. "Ironically, our Q/A people are now asking for drawings so they can inspect the parts in production. We have to go back and generate them."
"We're very pleased with SolidWorks," says Wake. "It's a great tool with a reasonable learning curve. We tried a more expensive CAD system but the dollars per seat are far better."
For typical mechanical objects, IDSI sends prints and a disk with the DXF file to the vendor for use with the CNC machine, thus eliminating the need for someone to translate a drawing into CNC coordinates. "A dimensional drawing would be laughable for this," says Wake.
"For a company our small size, I think we are fairly progressive on how we handle these complex drawing problems. We can easily get the information about what we want into the hands of the vendor," says Grable.
"We no longer need high-end computers or computer graphic tools. These programs work quite well on reasonably priced PCs," says Wake.
It has been a real learning curve, says Grable. "We use the analogy that it's like peeling an onion. You peel back one layer only to find another. It's taken awhile to get to the center." The design continually evolves.
Life cycle testing. "From the start, we wanted to be confident that the design would survive the life span of the machine with virtually no maintenance of the mechanical parts," says Wake. So IDSI performed a one-million-slice life-cycle test on the fiber cable system and related mechanical parts including the drive chain, the mechanism for raising and lowering the platform, and the motor that rotated the lasers.
"We had to know if we were building a monster or not," says Grable.
And since none of the fiber optic venders knew if their product could survive such a test, "We bit the bullet and tested for 24 hours a day, 7 days a week, for six months," Wake says. IDSI engineers illuminated the fibers at one end and, once a day, took a frame grab video picture of the other end to ensure there was no leakage from micro fractures or broken fibers. "We were also careful never to violate the bend radius of the fibers, making sure the cable swept a very generous arc inside the machine," he added. And the results: no degradation whatsoever.
Although not quite ready for prime time, two clinical studies are currently under way at the University of Virginia and Nassau County, NY medical centers. Grable hopes to have some version of their scanner marketable by Thanksgiving.
About the Author(s)
You May Also Like