Wireless Medical Device Features Press-and-Fit Assembly
June 10, 2010
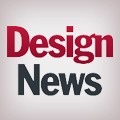
A new medical device monitors human body functionswirelessly in a fit-and-press assembly that requires no adhesives or mechanicalfastening.
Called ViSi Mobile, the wireless device is currently underdevelopment by DD Studio in concert with its client and manufacturer SoteraWireless Inc. of San Diego, CA. It was unveiled at Canon Communications' MD&M East show inNew York City this week.
Sensors attach to a patient's arm to monitor vital signs,such as blood pressure and heart rate so that clinicians can remotely monitorpatients' information. The system also includes an eight-port charging station.One of the benefits of the device is the ability to capture continuous bloodpressure measurement for ambulatory patients without the need for frequent cuffinflation. The system is compatible with standard Windows-based operatingsystems.
"When Sotera Wireless approached us with this medical-devicedesign concept, it wanted the look and feel of a small, user-friendly consumerproduct, but had a number of specific demands. The device had to be chemical-resistant,durable, easy to clean and submersible. We weren't sure the design waspossible," says Michael Swartz, growth strategist, DD Studio.
The device's lens, housing, printed circuit board assemblyand connectors are made with Eastman Tritan co-polyester MX711. Thecold-swaging capability of Tritan allows for fit-and-pressassembly of the device, offering a tight, smooth, continuous fit between parts.
The co-polyester also provides resistance to chemicals usedin disinfectants and cleansers without cracking or crazing. The material also exceededdurability requirements.
To protect the device from water and fluids found in thehospital environment, it had to meet IPX7 requirements (InternationalProtection Rating) of withstanding water submersion for 60 minutes at a depthof 1 meter. DD Studio relied on compatibility samples and testing results from PolyOneto select GLS Versaflex OM 3060 TPE, which adheres to the co-polyestersubstrate to seal the device housing, including speaker port and microphone,from water seepage and protect internal electronics.
The housing components use a two-shot injection moldingprocess, combining Versaflex TPE with the Eastman co-polyester substrate. Inaddition, insert-molded Versaflex is used to hold cables in place on the fourdevice connectors. This material provides firm adhesion to the cable assemblyand strain relief properties.
DD Studio and the product development team worked withPhillips Plastics Corp. to ensure the manufacturability of the design. Phillips Plastics Corp. of Hudson,WI took the designs DD Studio created and conducted a detailed DFM exercise andcreated market-entry prototype tooling.
Clinical testing on the device, which will be used inhospitals and homes, is now being conducted.
SoteraWireless, which changed its name from Triage Wireless in 2009, recently secured$10.75 million of a $15 million round of venture funding to develop itswireless monitoring technology. Investors in the company are Qualcomm Ventures,Intel Capital, Sanderling Ventures and Apposite Capital.
"Sotera's noveltechnology for monitoring all of the vital signs will be a valuable safety netfor seniors and people suffering from chronic diseases who want to live independently,but be connected to their doctor if there is a problem," says Gary West,founder and chairman of the West Wireless Health Institute (WWHI) in La Jolla,CA.
About the Author(s)
You May Also Like