Tips to simplify manufacturing
January 8, 2001
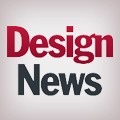
The focus of "design for manufacturing" is usually on designing in-house manufactured parts that are inexpensive to make and assemble. Yet there's another area of design for manufacturing that's often overlooked-selecting purchased parts that reduce assembly costs.
With the average cost of assembly time greater than $0.75 per minute, purchasing parts-even for a premium-can be cost effective. This arithmetic is simple, but there are often other factors which add another layer of complexity.
Enclosure manufacturing is one example that is directly applicable to many industries. These same principles apply to almost every type of manufacturing.
The parts of an enclosure that are purchased usually include handles, latches, hinges, locks, and gasketing; these are typically bought from specialized manufacturers. It is easy to merely select the cheapest hinge. A more difficult question is: "Does this represent the lowest overall costs?" So a better question may be: "Will this provide the best value?"
Examining each component in detail illustrates the trade-offs inherent in part selection.
Latches. Quarter-turn type latches are usually rugged and reliable. Remember that the ISO 9000 philosophy argues for non-adjustability during assembly, so selecting the correct non-adjustable cam can speed installation and remove the potential for error leading to under- or over-compression of the gasket. While the versatility of adjustable cams is attractive, they can be costly to install, and subject to misadjustment.
|
There are three typical attachment methods, all of which allow insertion of the latch through the cut-out without disassembly:
one nut; used for heavy duty or NEMA sealing-fast
spring clip; used for light duty, no tool required-faster
snap-in; used for nylon quarter turn latches only-fastest
Hinges.The engineer must consider an array of factors in hinge selection:
Many manufacturers find it more efficient to bring doors and cabinets together only after painting. This can be very difficult to do with weld-on or continuous hinges.
If hinges are positioned accurately, loads and stresses are shared. Otherwise, the door may "banjo," and either one hinge takes all the load or hinges are pre-loaded.
Less installation time leads to lower cost, as well as a higher capacity and faster response to customers.
When holes or cut-outs are punched or laser-cut, they have good accuracy and consistency. The alternative-using a new set-up for welding-yields larger tolerances, demands more handling, of course, and increases the probability of errors and misalignment.
A procedure that requires a high skill level almost always has an increased probability of error. And highly skilled people are relatively scarce and expensive.
If a door has to be replaced in the field, permanent attachment may be a problem. This can be significant with continuous hinges.
A hinge suitable for both left hand and right hand hinged doors avoids the need to hold inventory for both types, and the possible confusion of choosing between them.
Multi-point locking systems.For a company making enclosures of several different heights, there are three ways to buy locking rods:
Buy long rods and cut them to size. This requires time to cut and the extra cost of adapters. It incurs some extra cost, but is very flexible and needs a minimum of inventory.
Have rods made to length. This means that many rods must be inventoried in order to react quickly to new orders. The economic feasibility of this method depends on customer requirements.
Instead of using the top and bottom of the cabinet as latching points, install catches at specific locations. This reduces the number of rod lengths needed and can add value to the end user while reducing costs for the manufacturer (see drawing).
Conclusion. Selecting a purchased part with the best value is quite complex. It requires an understanding of current and potential manufacturing methods, the interaction of different parts, cost of inventory, the value to your customers of various features, and the value of customization.
Gasket table |
---|
|
|
|
|
|
About the Author(s)
You May Also Like