Specifying Captive Panel Screws by Design
February 26, 2013
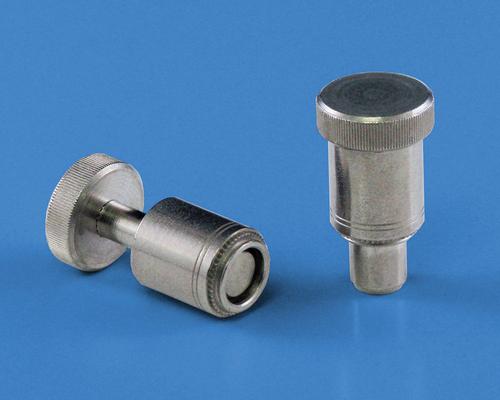
After a design engineer decides specify fastening hardware for an attachment application, the process turns to narrowing the field of candidates by evaluating application requirements. Engineers consider a fastener's mounting style, features, functions, costs, and other critical drivers. Understanding how a particular fastener does or does not conform to these requirements can make all the difference in an application's success.
One example offers universal lessons for the selection of other hardware -- a well-populated family of panel fastener assemblies that integrate captive screws. These assemblies are often considered for equipping panels, covers, drawers, racks, and other access points. In addition to providing secure attachment and controlled access, these fasteners are designed to keep the parts count to a minimum for easy and efficient handling and installation. They also mount permanently to eliminate the risks of loose hardware falling out, getting lost, or being misplaced, potentially damaging other components.
All panel fastener assemblies with captive screws deliver these fundamental advantages, and dozens of choices populate this hardware category. How should the design engineer proceed on the road to specification? By identifying which mounting style is best suited for the application and determining which features of the fastener will be appropriate for the application. The standard mounting styles of captive panel screws are self-clinching, flare mounted, and float/flare mounted.
Self-clinching types install flush (when using the shortest screw) on the backside of a panel, so there are no protrusions on the opposite side of the sheet. These screws require minimal panel preparation. No secondary operations will be necessary, which can maximize productivity along the line. The fastener is inserted into a properly sized hole in the mounting sheet and becomes a permanent part of the assembly when a press applies sufficient force. The sheet material surrounding the hole is forced into the fastener's undercut, preventing axial movement and rotation by a displacer.
For any self-clinching fastener, the relationship between fastener and sheet material is critical. There are three basic requirements. First, the metal sheets into which the captive panel fastener will be installed must have adequate ductility to allow displaced material to cold flow into the undercut. Next, these metal sheets must be softer than the fastener, so that the fastener itself does not deform during installation. Finally, these sheets must meet thickness requirements. As an example, one basic type of captive panel screw assembly requires a minimum sheet thickness of 0.036 inches (0.92mm). Typically, there is no specified maximum thickness, but sheet thickness may become a consideration, depending on the fastener's screw length.
Some applications may be inappropriate for self-clinching hardware, especially when stainless steel panels are involved, due to the relative fastener/panel hardness issue. But compatible solutions exist. An example is a captive panel fastener with a retainer made from 400 Series stainless, which installs reliably into a stainless sheet.
About the Author(s)
You May Also Like