Plastic gears 101
March 25, 2002
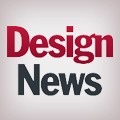
So you need a plastic gear set. Just crack open a catalog or design handbook. With a little basic information about center distances, pitch, and pressure angles in hand, you pick some matching gears. And presto, your new gear set is ready to roll.
Or is it? Plastic gear experts blame this kind of sketchy, yet common, design practice for many of the failures that in the past gave plastic gears a black eye. "There are a lot more factors to take into account with plastics than with metals," says David Sheridan, who works on plastic gear applications as a senior design engineer for Ticona (Summit, NJ). And the list of design sins doesn't stop with a lack of information. Many engineers still view plastic gears through metal lenses. As a result, they focus on design strategies that don't work well in plastics. "Most engineers already know metal gears, but for plastic gears they should forget some of what they know," says Art Milano, R&D manager for Seitz Corp., a gear molder in Torrington, CT.
Forget, first, about metal's mechanical properties. "They're typically at least an order of magnitude better than plastics in terms of temperature performance, strength, and stiffness," says Rod Kleiss, president of Kleiss Gears Inc. (Shoreview, MN). And forget about the one-size-fits-all approach. "For some really simple gears, you might get away with pulling something out of a catalog or the Machinery Handbook, but precision plastic gears are almost always custom gears," says Dr. Zan Smith, an engineering associate for Ticona and the company's resident gear guru. And finally, forget about those AGMA gear standards developed for metals. "Metals standards don't work for plastics in part because they don't address shrinkage and other properties of plastics," Kleiss points out. What's more, standards rooted in metal gears define the manufacturing accuracy rather than functional capability, adds Andy Ulrich, a senior project en-gineer who designs gear systems for UFE Inc. (Stillwater, MN). "People make the mistake of giving us drawings with a gear table based on metal standards and tell us, 'Just make it in plastics'," he says. "These are the gear designs that are most likely to fail."
With so much to forget about, why use plastics in the first place? Plastic gears, while hardly new, have come a long way and now routinely withstand conditions that once would have been unthinkable. "Early adventures in plastic gears had quality problems and failures," UFE president Martin Kellogg acknowledges. "But these failures had more to do with design inexperience than the use of plastics." And today, well-designed plastic gears in the right applications can outdo metals when it comes to cost, weight, noise reduction, and parts integration.
These benefits, however, only come to those who know how to design around those design pitfalls specific to plastics. Those who deal with plastic gears for a living caution against being too prescriptive, since molded gears tend to be so application specific-especially those designed to foster parts integration. "Every plastic gear design is different-or should be," says Kleiss. Even so, the tips that follow should head off some of the most common design mistakes whether you work with spur, helical, or worm gears.
Plastics aren't metals.
It may not get any more obvious than this, but engineers who design plastic gears for a living will tell you that unheeded differences between metals and plastics have ruined many a gear set. For one, the thermoplastics used for gears experience comparatively large changes in strength, stiffness, and dimensions in response to temperature, moisture, and chemicals. "These kinds of changes can mostly be ignored with metal gears," Smith says. "But they are critical with plastics." He adds that this difference becomes most apparent when a plastic gear works in conjunction with gears, shafts, or housings. "Plastics have a greater, faster response to their environment than the surrounding components," he says. "Engineers familiar with metal sometimes run simple load and wear calculations, come up with a nominal gear set, but they don't account for the ways plastics change, and with gears even small variations can cause big headaches." For another, injection molded plastics shrink-a lot. "Shrinkage changes everything about plastic gear design," Kleiss emphasizes. While metal gear dimensions stay close to stable during the manufacturing process, the thermoplastic grades commonly used for molded gears shrink by as much as 0.030 in/in, Kleiss reports. And they don't always shrink uniformly. If left completely unchecked, shrinkage can produce transmission errors and excess noise at best and gear failures at worst. And finally, with their lower strength and stiffness, plastics also deflect more than metals, potentially causing more transmission errors. Yet deflection can be a double-edged sword: Smith points out that deflecting teeth can allow the next tooth to be picked up sooner, allowing a load sharing that can offset some of plastics' strength disadvantage. "The important thing is to recognize the deflection and take it into account in your designs," he says.
Where will they live?
With these property differences in mind, the experts suggest that engineers next develop a true picture about environmental conditions in which the gears will operate. "Focus on what's really going on in the gear box," Ulrich says. And he stresses "really" because misconceptions about operating conditions can result in gear failures-or cause engineers to rule out plastics prematurely. "Misunderstandings have locked thermoplastics out of many good applications," Kleiss agrees. To take one example, conventional wisdom sometimes rules out plastic gears in wet operating environments because some gear materials absorb moisture so readily. But gear designers can offset swell, and gear molders can moisture-condition gears before shipping. "You actually can run in water as long as you take the moisture into account," Ulrich says.
Even more important to gearing success is an accurate insight into temperature. "What are the most common sources of gear failure? Temperature, temperature, temperature," says Kleiss, who points to an all-too-common confusion between ambient and operating temperatures. The two often differ because of the nature of gear transmission. As Ulrich explains, "People have always been told that gears roll, but that's not exactly true. They roll on one point and slide everywhere else." Without some design intervention, such as modifying tooth profiles or lubricating the gear system, all the sliding adds up to excess heat-and wear. And if plastics' natural dimensional changes throw off nominal center distances, even more friction and heat can result. Ulrich recalls one case where he had to fix a plastic gear design that had come straight from a handbook and took neither sliding nor center-distance variation into account. "The gears melted even though the vacuum cleaner had a 73F ambient temperature specification," he says.
False impressions about gear loads can create problems too. Some experts break gears down into motion transmission or power transmission, depending on their function. But because plastics have a lower strength than metals, Kleiss instead argues that most plastic gears should be treated as power transmission components-even if their stated purpose has more to do with motion control. "You have to look at things from the plastics' point of view," he says, noting that detailed load calculations figure into nearly all the work he does. And according to Smith, gear designers rightly focus on fatigue but too often ignore other types of loading. "Static loads and creep can be important issues in some applications," he says. As an example, he cites a gear that has to hold a car window up in the August sun. And inertial loads can be important for motor-driven gears that must come to a sudden stop as the motor cranks along. "The motor inertia translates to extra torque that can be many times the operating torque of the system," he says. In both cases, he adds, engineers can avoid failures by basing their designs and materials selection on a complete picture of loads.
Designing to operating conditions in advance can be something of a guessing game. So Smith says to consider those conditions that produce the loosest and tightest meshes for a given design and then verifying that the design works in these worst-case conditions. Once gears have reached the functional prototype stage, life cycle testing can help. Kleiss cautions, however, that some accelerated tests, with their unrelenting heat and loads, can produce conditions that the gears will not see in real life. For this reason, Kleiss advocates an automated testing regiment-where sensors shut down a test when it reaches real-world conditions. "Try to test in the framework of a gear's actual duty cycle," he says.
Design differences
Because of their shrink, plastics lack some of the dimensional certainties of metals. "So there's a lot more tolerancing in plastics," Kleiss says. Consider, he says, the gear's base circle, the controlling geometric feature that determines the involute tooth shape. "Diametral pitch, pressure angle, and tooth proportions all flow from the base circle," he says. "And because of shrink in plastics, even the base circle needs a tolerance if you have any chance of making a good gear."
Expect the differences between plastics and metals to manifest themselves in the tooth profiles too. Plastic gears tend to have taller tooth profiles in part to make room for changes in center-to-center distance variations. "Tooth proportion is the biggest difference," says Ulrich, adding that the taller teeth also help offset plastics' lack of stiffness and boost their contact ratio. Just how much taller are the teeth? Ulrich says it can vary, depending on the application. High-load gears, for example, sometimes have to trade off tooth height in order to hold up to higher bending forces.
Plastic teeth can have all sorts of subtle variations, reflecting the custom nature of molded gears. "The only golden rule of plastic gear design is to keep contact ratios over one," says Milano. And in Smith's view, it's worthwhile sticking to the mathematically generated tooth forms at first. "You can always add variations to solve specific problems," he says. To stop excess sliding near the root, Ulrich sometimes fattens up the tooth. He also likes to design roots with a full fillet as opposed to sharper transitions in metal gears. "You want to minimize any molded in stresses in the root," he explains.
Gears are never alone.
Don't expect the plastic gears to be a drop-in replacement for metals. All the gear specialists here cite cases in which they were asked to patch up existing gear designs-usually based on metal gears. "Metal designs are not easily rolled into plastics," says Smith. "Lots of times people design a transmission and then try to work plastics into it. Then when it doesn't work, they ignore plastics for years." Given the skill level possessed by molded gear specialists today, they can oftentimes fix failing designs. But they all say that plastic's biggest advantages come when the entire gear box assembly has been designed for plastics from the get-go with a systems approach that combines traditional mesh analysis with design strategies specific to plastics. "Generally brand new product designs are the best fit for plastics," says UFE Engineering Manager Robert Sirany, who does add that metal-to-plastic can also work as production volumes climb.
The difference between a systems approach and a gear retrofit often comes down to efficiencies. Milano recalls a case in which Seitz engineers took on a noisy, failing gear-box design for a child's motorized car. "It was a real screamer," he says. After a complete overhaul, they managed to come up with a new design that Milano estimates to be 80-90% efficient. "But we had to work with their existing envelope instead of designing it from scratch," he says. "It could have been 95% efficient with a different layout."
Taking a systems approach also means recognizing that gears don't work alone. Motors, shafts, and gear box housings can all throw even the most capable gear set out of whack. Poorly designed housings are one of the chief culprits, the gear specialists say. "If the housing varies or isn't rigid enough, all the hard work you've done on gear designs is lost," says Sirany. The toy car transmission that Milano fixed up, for example, did have some tooth profile problems, but it also had a housing that flexed so much that the teeth wouldn't engage. "In this case, the failure mode had more to do with the structure of the box," he says. Other components can likewise throw plastic gears out of alignment. Milano points to inadequately mounted motors as one culprit. "Your gears may have small total composite error, but that won't matter much if the motor shaft is wiggling around," he says.
Material concerns
The good news about gear materials is that there is a growing portfolio of thermoplastics available to meet rising thermal and load requirements. The bad news is that there are more grades to choose from-maybe too many for busy engineers. But before anyone sifts through a stack of data sheets, Kleiss says to take a close look at the gearing staples-straight nylon 66 and acetal-and avoid "overspecifying." "Some people say you always need filled materials," Kleiss says. But he argues that unfilled materials that meet application requirements have some important advantages over exotic grades. For one, the unfilled materials cost less, he says. For another, they can be smoother. "You can get a better surface finish with unfilled materials, which improves contact," he says. And most important of all, they may have an edge when it comes to quality. Competent molders with good tooling can achieve "nearly master gear quality" with unfilled materials. Some of that quality boost is rooted in experience. Gear molders have a long history with the shrink and other molding characteristics of the unfilled materials. "They shrink a lot, but it's a predictable, uniform shrink," Kleiss says. For all the advantages of the simpler materials, Kleiss does not suggest ruling out the exotic choices. "You can always step up to them if they can solve an identified cause of failure, but I always start with the most known materials."
|
One source of potential overspecification can be found on the data sheet pages. All those mechanical and thermal properties on data sheets should be treated as guidelines, not gospel. "Plastic gears will survive in conditions not suggested by the data sheet," says Kleiss. He recently did a gear, for example, for a valve lifter on a small engine. This gear, made from unfilled high-temperature nylon, has to hold up to temperatures of 310F. "The materials guys would tell you that the gears can't work, but they do," he says. The reason comes back to an understanding of operating environment: The brief impact loads and non-continuous temperatures experienced by these gears aren't reflected in ISO molding samples, he explains. "Material properties from datasheets can be more theoretical than real," Milano agrees, adding that he, too, has found thermal capabilities to be understated.
Lastly, be aware that machined plastics aren't the same as molded plastics. "A completely different beast" is the way Smith describes them. He explains that they have internal differences that affect strength-such as machined-in versus molded-in stresses. And he adds that machining can only produce metal-like tooth forms, while molding produces those tooth forms optimized for the behavior of plastics. As a result, machined plastic gears can have bending strengths as much as 50% lower than a well-designed plastic gear, Smith reports. Still, machined plastic gears can work as an initial prototyping method. Kleiss uses them as a confidence builder in metal-to-plastic conversions. As a quick and dirty test, he replaces metal gears with machined plastic gears. "If they last more than a couple of minutes there's a good chance that a well-designed molded gear set will do the job," he says.
Not so noisy
If you've chosen plastics solely for their noise reduction capabilities you may be in for a rude awakening. According to Dr. Don Hauser, an authority on gear noise who heads the Ohio State University gear lab, plastics have the potential to reduce gear noise. "But they don't always do so." Part of the problem lies in unrealistic expectations. As Smith explains, the lower flexural modulus of a plastic gear leads many engineers to the belief that the gears will be quieter. "But with the additional tooth deflection, the teeth can slam," he says. And the noise returns. Or often plastic gears suffer from surprising noise when they take the place of a lubed metal gear set. "The real issue is the lubricant," says Smith. "Grease and oil turn out to be dynamite noise dampers." Other sources of noise in plastic gears include irregular tooth shape, rough surface finish, and excessive sliding at the root. Fortunately, these problems can be designed away. "Plastics start off quieter and will stay that way if you design and mold them properly," Ulrich sums up. "But they won't inherently solve all your noise problems."
Avoid computer blunders
Solids-based CAD can either help or hinder the would-be plastic gear designer. Used properly, it has all the advantages of placing gears into the context of larger assemblies and providing that time-and-money saving link to manufacturing processes. Used improperly in lieu of a full mesh analysis? "Let's just say that CAD has gotten me a lot of work over the years," Kleiss jokes. The essential problem is that solid modeling easily turns out gear geometry that may lack gear functionality. Or as Seitz's Milano puts it, "Just because something looks like a gear doesn't mean it is a gear." In the most insidious cases, say Smith and Sheridan, CAD plug-ins can generate faux gear geometry that looks okay on screen but lacks a real gear's involute tooth profile. They tell cautionary tales of gears with arc-based tooth profiles making their way into production before anyone flagged the fact that they wouldn't work. "Be very careful with CAD," Sheridan advises.
The caution also applies to finite element analysis. According to Smith, commercial FEA codes have a poor track record simulating the sliding aspects of gear transmission. Sheridan adds that FEA also does a better job predicting the stress-strain behavior of metals. "The strength characterizations for metals are more highly developed," he says. But there's another reason for not relying too heavily on FEA: speed. Smith, Sheridan, and UFE's Ulrich report the ability to run through many cases in an hour when using gear analysis software-all three engineers use a package from Universal Technical Systems (UTS; Rockford, IL).
None of this is to say that CAD and FEA don't have a role. UTS president Jack Marathe suggests that both types of software have value when used at the right time. "First optimize the gear design, then feed the geometry into CAD for manufacturing purposes," he says. "Not the other way around." Likewise, he sees value in FEA only in those cases where you might want a final check of tooth stresses in an otherwise completed design.
About the Author(s)
You May Also Like