Molded Magnesium Parts Create Rugged Housing
December 14, 2009
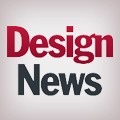
Injection molding magnesium? It sounds far out, but, in fact, it's increasing in popularity as a way of solving many design engineering problems.
Case in point: A Pittsburgh-based company called DynaVox Mayer-Johnson wanted a sturdy, but lightweight case to house one of its new speech communication tools - the DynaVox Xpress. It's for adults who suffer from strokes, ALS and brain injury, children with autism and Down syndrome, and others with speaking disabilities. The case also had to provide EMI/RFI shielding and be cost-competitive. And the product needed to be designed and launched in a hurry - in time for back-to school this past September.
"Part of the design goal was to make the Xpress as small and lightweight as possible," says Rick Severa, director of product design at DynaVox Mayer-Johnson. "But we also have to allow for all of the functionality, including speakers."
The Xpress is designed so it can project conversations outdoors, in restaurants, classrooms and even school cafeterias.
"One of the other big things for our users is the battery capacity," says Severa. "Laptop computers typically provide two to three hours of battery life. DynaVox devices require longer operating times. That means larger batteries."
Users of the speech communication tools have unique challenges. As a result, they must be rugged. "Children with autism and other conditions sometimes have behavioral challenges and will drop or throw devices. We need to make sure the device can stand up to everyday use in these environments," says Jim Shea, vice president of marketing at DynaVox.
DynaVox used a blend of polycarbonate and ABS for some early designs of its speech communication devices. The company's design and production partner, Phillips Plastics of Hudson, WI, recommended it consider cases made with the thixomolding process, in which liquid magnesium is molded. Phillips Plastics is unusual in the molding world because it molds plastics, powdered ceramics, powdered metals and molten magnesium.
"The magnesium moldings have thin walls and their strength-to-weight ratio is astronomical," says Severa.
The big advantage of thixomolding over die casting for magnesium is wall thinness, according to Dale Ek-Pangerl, the project engineer at Phillips Plastics' magnesium injection molding facility.
"You get lighter weight with thixomolding," he says. "We can do thinner walls with less draft in the thixomolding process, as opposed to magnesium die casting. Another big issue is that you can design the part as a plastic part and thixomold it. You have to redesign in order to die cast it."
DynaVox did in fact migrate a PC/ABS design from an earlier housing for use in the thixomolded housing for the Xpress. Housings made with plastic have thicknesses around 0.080 inch, or 80 mils (2.03 mm). More typical for molded magnesium is 0.060 inch, but in some applications gauge can drop to 0.030 inch. Severa also says the thixomolded magnesium walls hold tolerances very well.
There are other advantages, as well.
"We're using the magnesium housing as a giant heat sink," says Severa. "We attach the processor directly to the magnesium, and don't use fans for cooling." In addition to reduced weight, background sound is significantly reduced, he says.
The magnesium housing retains electromagnetic fields within the Xpress and protects against outside fields. Plastic boxes require various sophisticated solutions for electronics' shielding. For example, General Motors is debuting a new plastic case radio with insert-molded shielding on the Tahoe GMT900 family. In the patented innovation, steel mesh screens are robotically placed inside injection molds which are filled with 16 percent glass PC/ABS. Previous designs used a sheet metal case that required significant assembly.
The Xpress is equipped with a standard battery pack that lasts approximately 3.50 hours and weighs 1 lb 8 oz. An optional battery pack lasts approximately 8 hours and weighs 2 lb 1 oz.
The battery packs are self-contained with their own magnesium housings. The battery compartment has a slide and latch mechanism, requiring an undercut and action on the tool. In all, there are three molded magnesium components per unit.
Speakers are mounted to an IR transparent front grille made of polycarbonate. There are several other plastic components, which are primarily molded by Phillips Plastics from polyacetal.
DynaVox Mayer-Johnson began in 1983 as a Carnegie-Mellon University student project to help a young woman with cerebral palsy communicate. A product called the EyeTyper allowed individuals to spell messages with their eyes. Messages were then "spoken" by a computerized voice. DynaVox now sells a full line of speech devices that address various physical and cognitive needs. The Xpress, for example, can be loaded with software to enable speech for people who suffer from autism, ALS (amyotrophic lateral sclerosis or Lou Gehrig's Disease), cerebral palsy, Down syndrome, neurological conditions, stroke or traumatic brain injury.
Autistic children, for example, choose images that are translated to spoken words.
The devices can qualify for reimbursement from Medicare, Medicaid or private insurance. School districts may also buy devices for students. "DynaVox is the biggest company in the field and the market we're addressing is only 5 percent penetrated," says Jim Shea. "Many of the people who could use these devices don't even know they exist."
Because the Xpress is a portable device with a large potential student market, market timing was critical.
Phillips Plastics provided the design services, as well as prototyping, tooling and manufacturing for all of the relevant parts in the Xpress. Phillips Plastics is one of the largest custom magnesium injection molders in North America, with seven specially made injection molding machines ranging in clamping force from 220 to 850 tons. It's a fast-growing business with applications coming in the medical and military, as well as various consumer applications.
Temperatures and pressure are higher than plastics injection molding, requiring sturdy tools and presses. Magnesium melts at around 1,100F, compared to 300-400F for higher-level plastics. Designs are very close, but Ek-Pangerl recommends slightly more generous radii for magnesium parts to accommodate material flow.
Check out Phillips Plastics' full range of molding capabilities at www.phillipsplastics.com.
About the Author(s)
You May Also Like