For engineering plastics: evolution and innovation
July 24, 1995
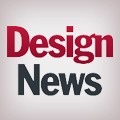
Sassenrath has been leader of Technical Polymers, one of the seven Hoechst divisions, and responsible for the worldwide business in engineering plastics since 1991. His career with Hoechst started in 1967 in the research and development department for fibers. In 1976 he moved to the Hoechst-Kehlheim plant and became leader of R&D for acryls and viscose fibers. A move back to Frankfurt in 1983 put Sassenrath in charge of process engineering for fibers. Five years later, he left for Hoechst Celanese Corp., Charlotte, USA, to become head of textile fibers research and development. Total leadership for fiber development, a post that brought him back to Frankfurt once again, preceded his present position. The percentage of plastics in cars, as well as in electrical and electronic products, will continue to grow, says Sassenrath.
Despite challenges, the plastics industry will continue to expand its market share in many fields, says Bernd Sassenrath.
Q: Throughout the 1980s, the use of plastics and elastomers made tremendous gains in automobile design. What are the growth markets for engineering plastics in the 1990s and beyond?
A: With our products, half of the total quantity is sold to the automotive industry and we believe that it will stay that way. The penetration of plastic materials in automobiles, however, will increase. In an European medium-sized car, currently an average of about 120 kg of plastics is used. Our estimation is that this will go up to 140 kg by the end of the decade due to a still-increasing level of comfort. Another growth market is the electrical/electronics sector, with about one quarter of the total quantity. And in both market sectors we have innovative applications, where thermoplastics offer a better solution or provide answers to problems that previously could not be solved. Security systems in cars, such as airbags and safety-belt systems, or electrical/electronic devices with highly-integrated, multifunctional components are examples.
Q: Are the barriers to furthering the widespread recovery of materials, plastics in particular, technical in nature, or are they simply the result of economic considerations?
A: Both. In general, easy solutions for the recovery of materials can be found if the various plastics are sorted, but unfortunately this is not always the case. The economic and technical value of "uncontaminated" plastics is much higher than that of a mixture of various polymers. Separation of the latter is too expensive for many applications. Although the economics of chemical recycling, preferably in closed loops, are still poor, this is the only way to resolve the issue permanently.
Q: To what extent does Hoechst produce materials with a view towards their eventual recovery and reuse?
A: One possibility to facilitate recycling is the reduction of the large numbers of different plastics in one component. Therefore, it's helpful to have a wide product range of one polymer type. For example, our polyacetal "Hostaform" offers a comprehensive range of grades. Users can select the most suitable ones for their purpose while remaining with polyacetal and so facilitating recycling. In addition, we pursue the goal of chemical recycling with polyacetal and PTFE.
Q: What new developments can design engineers look forward to with regard to engineering-grade plastics?
A: Classical engineering plastics like polyacetal and polyester are continuously improv ed according to customer requirements. The further development of such materials is driven by various factors, such as improved impact resistance, high UV stability and flame retardancy. This is an evolutionary, rather than a revolutionary, process.
A higher rate of innovation can be found with high-performance thermoplastics, such as polyphenylenesulphide (PPS) and liquid crystal polymers (LCPs). The higher level of mechanical stability in a wide range of end-use temperatures allows for further metal substitution. Look at our liquid crystal polymer Vectra: The unique property profile of LCP allows highly innovative applications in the electronic industry, such as molded interconnected devices (MID). These and other LCP applications can also be used in Surface Mount Technology (SMT). Such techniques allow for a higher degree of integration of components and, in addition, lead to further miniaturization.
Q: Of the families of engineering plastics, which ones are growing fastest?
A: Among the engineering resins, polyester shows the highest growth rates driven by applications and the substitution of polyamide in certain electric/electronic segments. Polypropylene and reinforced polypropylene are growing rapidly due to further product development and high-volume applications in the automotive industry, also through the substitution of ABS in interior trim parts. After a period of embryonic markets, high-performance polymers like PPS and LCP are now growing rapidly. Here we expect a growth rate of 10 to 15% a year.
About the Author(s)
You May Also Like