Composites Cut Weight on Backcountry Aircraft
December 9, 2010
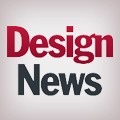
Direct long-fiber composite parts are replacing machined aluminumfor hatch covers on the amphibious versionof the Quest Kodiak, a single-engine turboprop, backcountry utility aircraftmanufactured in Sand Point, ID.
"The aluminum parts were too heavy while these new onesweigh less than two pounds," says Dan Garrett, the Wipaire R&D engineer incharge of the project. "Also, they were subject to dents and bending, and theycost too much - approximately five times the cost of the composite parts." Corrosionresistance and ease of replacement were also issues in moving from aluminum tothermoplastic composite.
The 14 x16 inch hatch covers are made with a new technologycalled Pushtrusion D-GMT. Hot charges of metered, long fiber-reinforcedpolypropylene compound are transferred to a compression press and immediatelypressed into finished parts, eliminating glass mat technology (GMT) sheettypically used in compression molding.
Composites Cut Weight on Backcountry Aircraft_A |
"The Pushtrusion process gives processors the flexibility tocustomize their specific formula by fiber loading, polymer type and color,"says Steve Bowen, president of PlastiComp, the system developer. "They are notlimited to standard GMT sheet offerings." Other thermoplastics that can be usedin the system include polyamide, thermoplastic polyurethane and PBT-typepolyester. Available fiber systems include E-glass, S-glass and carbon.
Garrett says he considered a thermoset sheet moldingcompound (SMC) with long fibers but was concerned with high material anddevelopment costs. Thermosets require curing cycles and are labor-intensive.
The hatch is molded in a precolored, black pigmented, UV-stabilizedmaterial and is then painted with a black non-skid coating on its exposedsurface to match the upper, walked-upon deck surface of the float. Foot trafficdictated sufficient load bearing stiffness as a primary criterion in thedesign.
The exposed upper surface of the hatch cover is mostlysmooth, with a channel for a sealing gasket. There are thicker sections at theperimeter for threaded fasteners as well as a perimeter wall. Ribs radiate tothe wall from a central boss where a standard, snap-in-place inspection port isinstalled.
Fast Development
The new long glass-reinforced thermoplastic hatch coverswere a joint development. PlastiCompprovided technical guidance on materials and processes plus the actual part moldingwhile Wipaire designed the partand made the mold in its in-house machine shop. The project was completed inless than four months.
The floats add approximately $250,000 to the 10-seataircraft's base cost of $1.1 million.
The hatch covers are the second application for the Pushtrusionprocess, which previously has been used to make covers and lids forwater-treatment units.
About the Author(s)
You May Also Like