The Case of the Missing Machines
August 11, 2011
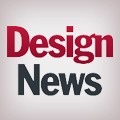
It began as a simple customer request. My company, the aerospace supplier Bertsche, was working with a tier-one manufacturer of large airplane structural assemblies. It needed to modify semi-finished and partially-assembled detail parts on a daily basis.
The parts are needed for large airplane structural assemblies, and they need to be in place just prior to final assembly. The manufacturer was searching for an all-purpose machine that could quickly be step up to run a wide variety of parts to support several different airplanes. It was using three older machining centers, and there were production and logistical problems.
Airplane manufacturers often start the manufacture of parts for a specific airplane order well before all detail parts for that airplane have been fully defined. This is great for the airlines, but it complicates the process of building planes on a tight schedule. Furthermore, airplane manufacturers must have considerable flexibility built into their processes, to allow last-minute modification to parts that will be needed shortly in final assembly.
The manufacturer needs to modify or rework every detail part for a specific structural assembly. On short notice, CNC (computer numerical control) part programs need to be created for virtually every part used in the subassembly, while special tools and fixtures need to be available and easily set up in machines. Thus, the parts must be manufactured just before they are needed at assembly. This is truly a "one off" manufacturing environment where the first part must be a good part with no margin for error.
The customer's initial request was simple: replace three small footprint machining centers with a single machine tool that could quickly reconfigure tools, workholding fixtures, and programs to manufacture the parts needed to complete a specific airplane. Specialized workholding, developed over many years for legacy (older model, mature) airplanes had to fit onto the new machine, as well as new workholding needed for the latest model airplanes. Set-up time needed to be minutes, or, at most, hours and not days.
Now comes the fun part and the real challenge for my team.
The customer wanted to reduce operating costs by reducing the number of people needed to run the machines, reduce set-up time, and improve productivity. The existing machines could only manufacture small parts fitting a 20-inch x 30-inch work envelope, but the new machine had to handle these parts, plus parts as long as 240 inches. There was neither budget nor floor space to replace the existing machining centers with new ones. Between the variety of work-piece sizes and the volumes involved, this was a very daunting task. We thought about many possible solutions to the problem but kept returning to the single-machine concept.
Having developed a long X-travel, raised-carriage, fixed-bed machining center (Xi-Mill) for single or dual work-zone long-part machining, our solution was to expand the capabilities of the existing machine design by developing a new type of machine, the X-Flex Center, configured with multiple pallet receivers instead of the typical T-slot tables. This allowed the customer to load multiple workholding fixtures into the machine and have them ready to run on short notice.
Equipped with a set-up changer, the machine could quickly be reconfigured by pulling new workholding fixtures from storage and loading them into the machine to match constantly-changing production requirements and schedule changes. Having the dual work zone feature with each work zone having its own dedicated tool changer, the operator was able to load newly tooled fixtures in one zone, while parts were being machined in the other.
Long parts, short parts, 4-axis machining, smart fixture control, automatic fixture recognition, integral thermal growth compensation, video camera actual cutting display, different materials, aluminum, titanium, composite parts, sandwich materials, materials separation, special water filtration, and other considerations arose, with each requirement mandating additional machine functionality.
To meet these requirements, a zero-point clamping system was incorporated into the base table, which allowed the pallet receivers to be decked with various long-part handling special tables. The zero-point clamping features meant that different tables could be quickly installed, with a high degree of repeatability (0.0002-inch repeatability for a 120-inch-long table). Large and heavy special tables could be craned overhead, lowered into place, clamped, and locked down to do production-ready machining in minutes.
About the Author(s)
You May Also Like