Breaking the glass barrier
October 6, 2003
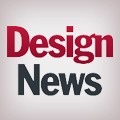
Do car windows have to be made from glass? The automotive industry has always answered "yes." But you may soon find yourself gazing through a very different kind of glazing. Recent advances in materials and processing technology have for the first time made polycarbonate a viable alternative to glass for mass-produced vehicles.
With its optical clarity and high impact properties, polycarbonate has drawn interest as an automotive glazing candidate for years. And the material has already seen limited use in production vehicles-notably in the SMART car's wraparound quarter windows. Until now though the plastic hasn't gone beyond what could generously be described as niche applications. Blame the auto industry's valid concerns about cost and some skepticism that polycarbonate can meet performance standards. In June, Exatec LLC, a Wixom, MI-based technology company formed by polycarbonate suppliers Bayer Polymers and GE Plastics, launched a proprietary materials and manufacturing system that could overcome those concerns.
The system addresses the technical limitations associated with plastics-including its sensitivity to UV light and its soft surface relative to glass. It could also parlay other aspects of injection-molded plastics into an advantage over glass as well. Chief among these are new styling possibilities that spring from plastics' design freedom. "Styling will be the main driver for polycarbonate," predicts Exatec manager Peter Reisinger. "So much of what cars look like today are related to the limitations of glass glazing," he continues, citing the constraints imposed by glass's relative flat geometries, limited color pallet, and decoration shortcomings. Polycarbonate also promises to aid other important engineering endeavors, including weight reduction and safety enhancement. And properly designed polycarbonate windows even offer the potential for function integration and parts consolidation.
Despite these potential advances, don't look for polycarbonate to overtake glass anytime soon for a couple of reasons. For one, glass gets better all the time. For another, current NHTSA safety regulations rule out plastic for windshields as well as for moveable side windows. "That leaves just the fixed vent window and back lights," says Paul Eichenberg, marketing manager for PPG Industries' North American glass business (www.ppg.com) in Troy, MI. And though regulations can always change to keep pace with new technology, Exatec itself has no current plans to tackle the windshield. "It will be the last area we target," Reisinger admits.
Even if some windows remain off limits for now, there are still plenty of places where polycarbonate glazing could add value. Panoramic roofs, increasingly common in Europe and making their way here, are a good fit. "It's where our weight and safety advantages matter the most," Reisinger says. He adds that Exatec's technology, despite its recent launch, has already garnered strong interest from OEMs and suppliers.
Systems Approach
Exatec has been working on polycarbonate windows for five years, but it took a big step toward making them a reality at the National Plastics Exposition in Chicago. There, the company unveiled a full-fledged technology package covering all the technologies needed to make polycarbonate windows that meet automotive standards. Available for license, this Exatec 500 system relies heavily on material technology. But it also includes the manufacturing know-how to produce the plastic glazing reliably.
Exatec has chosen to stick with polycarbonate grades that have proven themselves on headlamp applications. "These plastics have years and years of history," says Bill Curtis, the automotive program manager with Bayer's Industry Innovations Group. He explains that these materials already have the optical properties in excess of what glazing needs-including a light transmission value of about 90% for 4-mm thick glazing. And polycarbonate, which sometimes sees use as bullet-resistance glazing, already has about 200 times the impact strength of glass. The only changes made to the headlamp grades have been minor ones.
Curtis notes that the glazing materials grades must be manufactured to extremely tight cleanliness standards to avoid any contamination that could ultimately affect optical properties. And he says that they also have a greater need for UV-stabilizers than headlamp materials.
But in other ways, the material challenges are so severe that polycarbonate glazing would never be road ready without a coating that can add some scratch resistance and improve the UV performance beyond what stabilizers can provide. Exatec's system relies on two coatings to impart these properties: A wet coat provides the UV resistance, and a proprietary chemical vapor deposition (CVD) coating-a silicon oxide-adds the scratch resistance. "The coating provides a glass like layer," says Reisinger, who reports that the wet coat has allowed polycarbonate glazing to pass the standard Arizona and Florida weathering tests as well as the automakers own abrasion tests. "We pass the strictest automotive abrasion tests with less than 2% change in haze after 1,000 cycles," he says.
Molding Methods
Exatec's technology package also extends to the molding-and for good reason. Parts as big as automotive windows have enough projected area to require huge molding machines. An SUV backlight, for example, might encompass more than a square meter and measure more than 4 mm thick. "You would normally need a 4,000 ton press to mold it," Reisinger says. And presses as big as this are neither cheap to buy nor to run.
Big, optical polycarbonate parts also tend to suffer from molded in stresses. In the case of automotive glazing, these stresses may never rise to the point at which they create enough birefringence to hurt the optical properties, but they can cause stress cracks.
Exatec strongly recommends injection compression molding as a way to combat both of these problems-though Reisinger says the company has not made this molding technique part of the technology license. Performed on standard molding machines with machine controller changes and special tooling, this low-pressure molding technique involves shooting the plastic into partially open mold and then squeezing the mold shut part-way through the cycle to complete the filling. Injection compression molding is well known for the clamp forces needed for a given part and cut molded in stresses.
|
In a demonstration at the NPE Show, Exatec demonstrated just how well injection compression molding works. It turned out square-meter-sized windows on a 2,000-ton Battenfeld machine equipped with a proprietary injection compression tool built by Germany's Summeres Technologies. According to Reisinger, this injection compression variant cut the size of the press in half. "The typical reduction factor from injection compression molding is two," he notes.
As for the molded-in stresses, Reisinger won't say exactly how much they've dropped. Partly his reluctance springs from the difficulty in quantifying stresses in absolute terms. "There are still academic debates about the best way to measure molded-in stresses," he says. And Exatec considers its relative data on stress reduction part of its proprietary technical expertise. For now, the company has been showing the stress reduction in a way many molders understand-by holding a polarized light filter to the part and looking at stress lines.
Plastic Benefits
Glazing may lack glamour right now, but polycarbonate could change all that. Reisinger likens polycarbonate glazing's situation to that of headlamps 20 years ago. "Round or square was the only choice," he says. "No one thought of headlamps as a styling element." But as plastics hit the scene, headlamp designs flowered. "And they became a styling element," he says, predicting a similar trajectory for polycarbonate glazing. "No one picks a car because they really like the glazing. But they will."
He argues that polycarbonate can influence styling in three ways. For one, it offers complex shapes not practical with glass. "Injection molding can readily achieve three-dimensional shapes and deeper curves than glass," Reisinger points out. For another, polycarbonate takes color easily, opening up new tinting possibilities and the ability to match window tints with body colors. And finally, Exatec has developed a proprietary three-dimensional printing technology that can add all kinds of printed effects to the inside of the glazing-including translucent areas, pictures, decorative borders, or logos. "It has a similar resolution to silk screen printing," Reisinger notes.
Beyond styling, plastic glazing promises to have engineering implications too. The most obvious has to do with weight reduction. Polycarbonate has a specific gravity of 1.2, less than half that of automotive tempered glass at 2.5. In most designs, that translates to about a 50% weight reduction. The savings doesn't exactly match the specific gravity difference since the polycarbonate glazing would usually be slightly thicker than tempered glass-usually 4 mm thick for plastic versus 3.8 for comparable glass glazing.
What's more, specific gravity and thickness tell only part of the story. The weight savings could, in fact, be greater owing to plastic's ability to foster function integration and parts consolidation. Reisinger notes that all kinds of features can be molded into the plastic glazing, including handles, appliques, and assembly features like bosses and clips. The molding process can also add ribs, deep curvature, and other structural elements, all of which may offset plastic's inherent stiffness disadvantage relative to glass. "But we're not talking about an ugly rib down the middle of the window," Reisinger says.
|
Throw two-component molding into the mix, and the opportunities for function integration get even better. Exatec has demonstrated two-component molding as a way to encapsulate the glass as well as integrate more assembly and structural features. "In principle, two-component molding could integrate weather seals too," says Reisinger. The company and potential customers have started to look into the feasibility of molding glazing as part of a door module.
The final benefits of plastics relate to safety and theft prevention. You don't need to review impact data or start smashing windows with a sledgehammer to know that polycarbonate has a huge impact strength advantage over glass. And its ductile nature also keeps it from fracturing into shards when it does fail. "Tests that measure the size of glass shards don't apply to polycarbonate. It doesn't fail that way," Reisinger explains. These characteristics have paid off when Exatec subjected its glazing to standard crash tests, including rollovers. "All the polycarbonate windows remained intact," Reisinger says. And he adds that the windows have performed equally well in breakage tests-involving a large man trying to smash windows with a hammer.
All of plastics' style and engineering benefits can complement one another. When used in a panoramic roof, for example, polycarbonate's weight advantage could lower the vehicle's center of gravity, while the impact strength enhances passenger retention, Reisinger says. Or in a lift gate, he continues, the reduced weight of the glass could make the door easier to open-and perhaps even enable smaller motors for the automatic liftgate opening feature now appearing on minivans. The shape complexity, meanwhile, can have beneficial engineering implications too. "Molding allows us to produce deeper curves than glass, which not only enhances styling but also provides tremendous rigidity," Reisinger says. "With shape complexity, you get the additional rigidity for free." To show how some of the benefits might come together, Exatec engineers performed a design study for an SUV lift gate that integrates ten features-the center high-mounted stop light, three appliques, two hinges, two strut attachments, a handle, and a latch-and has a rigidity promoting curved design (see image on page 95).
Bumpy Road?
Despite all the potential benefits of polycarbonate, it may still have a bumpy road ahead of it for reasons having nothing to do with regulations. Most important, cost could weigh against polycarbonate. "I personally don't think polycarbonate will ever cost less than glass," says Hero Mori, author of several studies on glazing for the Automotive Consulting Group (www.automotiveconsultinggroup.com). "Look at it this way: The raw material for glass is sand. The raw material for polycarbonate is oil." Mori estimates that on a raw material basis glass currently costs about three times less than polycarbonate. But Mori acknowledges that as part of modules and "encapsulated structures," polycarbonate begins to make more sense from a cost perspective.
And Mori cites another potential trouble spot for plastic windows-NVH issues. "Mass and NVH have an inverse relationship," he points out. All else being equal, lower mass glazing would not reduce noise, especially low frequency noise, as well as a high mass glazing. And because polycarbonate glazing lacks the stiffness of glass, which has a Young's modulus of 10.6 Mpsi, it has some potential to "flop around" if not properly constrained, potentially adding to vibration problems. Eichenberg calls this problem "oil canning" and says it popped up in early OEM tests of plastic glazing.
But NVH reduction is rarely clear-cut, and proper design practice may offset any lack of mass and part stiffness. Reisinger notes that stiffness of the polycarbonate part can be easily fine-tuned with ribs or the curvature of the glazing. And the plastic itself, in part because of its lower modulus, also has some intrinsic damping characteristics that could actually reduce noise transmission, Reisinger argues. Exatec has subjected its glazing to NVH tests and found they "outperformed glass at frequencies above 2,000 Hz," he reports. "This is the frequency range for much of the wind noise," he says. And these test results are consistent with laminated glass, whose PVB interlayer acts to damp vibration. PPG has seen reductions in between 5 and 8 dB when replacing tempered with laminated glass, according to Eichenberg.
Whether it comes down to reducing cost and noise or to reaping the full styling and engineering advantages of polycarbonate glazing, Reisinger stresses that an upfront design for plastics is the key to success. "Polycarbonate glazing that just imitates glass doesn't offer a lot of value," he says.
Senior Editor Joseph Ogando can be reached at[email protected].
About the Author(s)
You May Also Like