Integrate TOP and POP
July 19, 1999
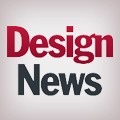
Over the past 10 years, many paradigms for improving development and production processes have been set forth. Their common objective is to achieve dramatic performance improvement through redesign of the firm's processes. Various terms identify them, such as Total Quality Management (TQM), Business Process Redesign (BPR), Concurrent Engineering (CE), Rapid Product Development (RPD), and Theory of Constraints (TDC).
Some of their implementations have been successful, many others have failed to live up to their promise. Most managers and their staff in the unsuccessful situations view these paradigms as "just more gimmicks" to be resisted, sabotaged, and rejected. Because of their background, training, and experiences, they refuse to believe that these paradigms, when properly implemented, could achieve their objective and dramatically improve the bottom line.
However, proper implementation requires close collaboration between what we will call a People-Oriented Perspective (POP) and a Task-Oriented Perspective (TOP). Unfortunately, collaboration seldom takes place without a lot of effort.
Concise background. Conceptually, TOP was introduced in the early 1900s as scientific management by F.W. Taylor, and others. It became the basis for most of the organizational forms and leadership styles that expedited the industrial revolution and was an important factor in the successful outcome of the World War II arms race. It still has an important place in management thought and action, as it should, especially now as we enter the knowledge revolution in the late 1900s.
TOP defines individual work tasks and their relationships within and between work processes. TOP usually focuses on schedule reduction, cost reduction, performance requirements, improving productivity, and error reduction. It uses hierarchical relationships that focus on quality, control, objectivity, analysis, and the bottom line.
POP's start. POP got its start in the mid-1940s. It focuses on getting people to work well together, improving teamwork, appreciating the value of diversity, sharing leadership, participating in decision-making, opening two-way communication, and developing flexibility.
In most traditional organizations, the TOP practitioners constitute the line-organization, and exercise most of the power and responsibility. They approach relationships objectively, and they devote little effort to personal or psychological issues, because they believe POP is irrelevant, especially in today's high-tech fast-paced organizations. They think they don't have time for that "touchy-feely soft stuff" when so much of their concentration is devoted to getting the work out.
As we enter the knowledge age, TOP and POP must collaborate to create and maintain successful organizations. Work tasks cannot always be specified in detail, and micro-management will not always be appropriate. Yet, TOP tools such as those for scheduling, planning, measurement and control must be used to some extent to achieve bottom-line success. At the same time, POP techniques such as those used for introducing change, motivating, empowering, power sharing, encouraging two-way communication, understanding and influencing organizational culture are also necessary, but not sufficient for organizational success. TOP and POP must be integrated.
Ask the Manager
Q: Why is it so difficult to collaborate TOP and POP?
A: From its beginning, TOP concentrated on how to do things better, cheaper, and faster. In his famous shovel experiment in the early 1900s, F.W. Taylor ran tests using Schmidt, whom he considered to be a "standard man,'' to handle the most material in a specified work day. There was no concern about Schmidt as a person, he was simply treated as an appendage to the shovel. The results were positive. By adopting a standard shovel size, output increased dramatically.
In those days, Taylor's decree was that workers were not supposed to think, other people are paid to do that.
POP from it's beginning concentrated on a people perspective. Its thesis: Involved and motivated people do better work.
In the late 1920s, an experiment using the TOP approach was conducted at a telephone relay assembly plant in Hawthorne, IL. Its intended purpose was to determine how the assembly process could be performed with high quality, at high speeds and for less money by manipulating the assembly conditions, a goal similar to finding the optimum shovel size.
A group of five women performed the assembly process in a separate room under various conditions. The results convinced Elting Mayo of Harvard University, and others, that the conditions imposed had very little to do with the assembly groups improved output! Rather, a people perspective (POP) was found to influence output improvements. The group members (who soon began to perform together as a team) were given some responsibility for improving the process.
Champions promote both TOP and POP and pass their favorite along to successive generations as being the "right way" without much attempt to integrate the two into a realistic paradigm.
Fax your management questions to Design News at (617) 558-4402 or e-mail your question to [email protected]
About the Author(s)
You May Also Like