The Conundrum of Published Specs Versus Real-World Performance
January 23, 2015
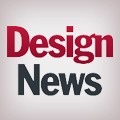
One topic seems to have been coming up lately among some of my engineering friends: What should be the perception of a product's real-world performance with regard to the published spec sheet? While it is easy to assume that the product will operate according to spec, what variables should be considered, and is that a designer obligation or a customer responsibility? Or both?
The phrase we often use is how much slop should be built into the design specs? Another way to put it is: How much consideration should we give to external factors over which we have no control (the customer using cheap connectors that may add resistance, for example -- Ohm's law didn't change the design, but a change in resistance did when poor quality connectors were used). Depending on the application, these factors may be completely negligible, or they may introduce a problem unbeknownst to the user.
Let me explain. You are designing a circuit that will do "such and such" (fill in here your current project). For the purposes of this discussion, it will be a commercial design and therefore in use for non-critical applications. You, the engineer, have been asked to calculate "such and such," and these numbers will be provided to the potential customer. Do you provide calculations that are 100% theoretical and would be correct in a perfect world, or do you add fudge factors into your numbers that could account for unknown variables such as those uncontrollable external factors I mentioned?
As much as electronics is a science with calculable results (Ohm's law is Ohm's law and doesn't change -- it is a law), the known resistance of a circuit trace can change due to temperature or environmental stress. How should a person account for the possibilities of those types of changes, and to what lengths should they go in doing so regarding their final design? When a customer buys that product, what can he or she reasonably expect regarding the product's operation? Should it match the specs perfectly every time? Should the specs include a tolerance due to customer expectation and unknown variables that could affect its performance? What factors drive these types of decisions?
Various factors come to mind, with an obvious one being cost. How much does it cost to produce the design in such a fashion that it will perform as expected even when experiencing some sort of stress, anticipated or not? Another factor that may be considered in the decision-making process is how performance is affected if the part is not quite up to spec due to an environmental factor.
For example, a product is typically used at room temperature, but what if someone decides to use it at 40F? Or, the product is being used in an exceptionally noisy environment with minimal shielding. Are the electronics affected by the noise in its specific application? Who has the ultimate responsibility for ensuring the product meets the advertised specification and under what conditions?
Different companies will have different approaches in place regarding published specs versus real-world performance, and within the same company sales and engineering often have different perspectives. By being aware of the possible issues that can arise because a product doesn't meet customer expectations (regardless of environmental factors that may seem obvious to you but the customer is either completely ignorant of or expects a certain level of performance regardless of factors beyond your control), you can save yourself and your organization much grief.
The important thing is to figure out your approach before moving forward in a design, and if the product is already designed, to make sure that engineering and sales are on the same page when quoting specs to customers.
Design engineers and professionals, the West Coast's most important design, innovation, and manufacturing event, Pacific Design & Manufacturing, is taking place in Anaheim, Feb. 10-12, 2015. A Design News event, Pacific Design & Manufacturing is your chance to meet qualified suppliers, get hands-on access to the latest technologies, be informed from a world-class conference program, and expand your network. (You might even meet a Design News editor.) Learn more about Pacific Design & Manufacturing here.
Nancy Golden started her electronics career at Dallas Semiconductor and moved to Optek Technology where she was a test engineer for several years, eventually moving up to test engineering manager. She became especially experienced in Hall effect characterization and test and also gained experience with photologics, LEDs, VCSELs, and fiber optic transmission. She was also the first person to become a Certified TestPoint Application Specialist (CTAS) by Capital Equipment Corporation and has done contract work for Hitachi and Andrews Corporation and control room software for NBC in Testpoint. Nancy owns a small business called Golden Technical Creations, a service-oriented company that provides consulting, teaching, PIC programming, course development, and web design to its customers. She also has a M.A.R. with a focus on intercultural studies and is an adjunct faculty member at Dallas Christian College.
About the Author(s)
You May Also Like